A depyrogenation tunnel is a pharmaceutical manufacturing equipment designed to remove or reduce pyrogen contamination from glassware, containers, and other equipment used in the production of sterile pharmaceutical products. Pyrogens are fever-causing substances that can be present on the surfaces of equipment and can cause adverse reactions in patients if they enter the bloodstream during drug administration. The de-pyrogenation tunnel uses high-temperature dry heat to sterilize and remove pyrogens from the equipment, ensuring that the finished pharmaceutical product is free of contaminants. This equipment is essential in ensuring the safety and efficacy of pharmaceutical products and is widely used in the pharmaceutical industry.
Working Principle of Depyrogenation Tunnel
The working principle of a depyrogenation tunnel involves the use of high-temperature dry heat to sterilize and remove pyrogens from glassware, containers, and other equipment used in pharmaceutical manufacturing.
The equipment is first loaded onto a conveyor belt and passed through a pre-heating zone to ensure that the temperature of the equipment is uniform before entering the main heating zone. The heating zone typically consists of a series of heating elements that are arranged to provide a uniform temperature distribution throughout the tunnel.
During the heating process, the equipment is exposed to high temperatures, usually ranging between 250°C to 400°C, for a specific period of time, typically ranging from 15 to 45 minutes. This heat treatment destroys any bacteria or other microorganisms present on the equipment and also removes any pyrogens that may be present.
After the heating process is complete, the equipment passes through a cooling zone to lower its temperature to a safe level before being unloaded from the conveyor belt. The equipment is then ready for use in the production of sterile pharmaceutical products.
Overall, the depyrogenation tunnel provides an effective means of ensuring that glassware, containers, and other equipment used in pharmaceutical manufacturing are free from pyrogens, thereby minimizing the risk of contamination and ensuring the safety and efficacy of the final pharmaceutical product.
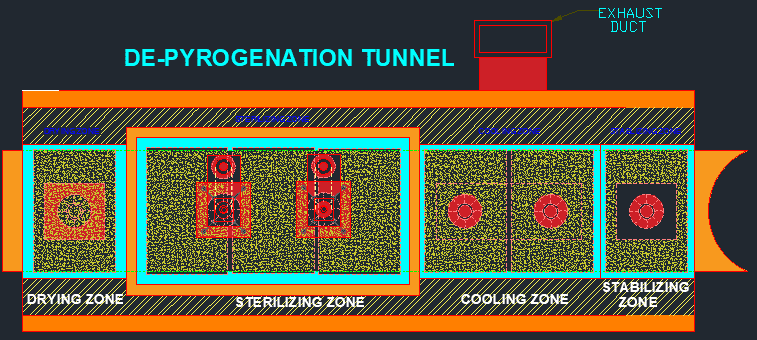
Depyrogenation Process :
Depyrogenation is the process of removing or inactivating pyrogens from materials such as glassware, containers, and other equipment that are used in pharmaceutical manufacturing or in the production of medical devices. Pyrogens are substances that can cause fever when introduced into the body, and they can be found in various sources such as bacteria, bacterial endotoxins, and other microbial contaminants.
Depyrogenation is important in pharmaceutical manufacturing because the presence of pyrogens in injectable drugs, for example, can cause adverse reactions in patients. The process of depyrogenation typically involves exposing the equipment to high temperatures, usually above 250°C, for a specific period of time in a depyrogenation tunnel or oven, which can effectively destroy or inactivate pyrogens. Depyrogenated equipment is then used in the production of sterile pharmaceutical products to minimize the risk of pyrogen contamination.
Technical features of a depyrogenation tunnel:
Technical Feature | Description |
---|---|
Temperature Range | 250°C – 400°C |
Exposure Time | 15 – 45 minutes |
Heating Elements | Quartz or ceramic heating elements |
Conveyor Belt Speed | Adjustable |
Airflow System | Forced hot air circulation system |
Control System | Programmable logic controller (PLC) |
Validation System | In-built data logger with temperature sensors for process validation |
Material of Construction | Stainless steel |
Safety Features | Interlocks, alarms, and emergency stop buttons |
Power Supply | 3-phase electrical supply |
Available Sizes | Various sizes ranging from small laboratory models to large industrial models |
Regulatory Compliance | Meets international regulatory standards such as cGMP and FDA guidelines |
These are general technical features, and specific depyrogenation tunnels may have variations in their design and specifications based on the manufacturer and intended use.
Major Parts of the depyrogenation tunnel:
- Loading area: This is where glassware, containers, or other equipment to be depyrogenated are loaded onto the conveyor belt for processing.
- Pre-heating zone: This is a section of the tunnel where the temperature is gradually increased to ensure that the equipment is uniformly heated before entering the main heating zone.
- Main heating zone: This is the core part of the tunnel where the equipment is exposed to high temperatures for a specific period of time to destroy microorganisms and remove pyrogens.
- Cooling zone: This is a section of the tunnel where the equipment is cooled down to a safe temperature before being unloaded.
- Conveyor belt: This is a continuous belt that carries the equipment through the tunnel at a controlled speed.
- Heating elements: These are quartz or ceramic heating elements that generate heat and maintain the desired temperature within the tunnel.
- Airflow system: This is a forced hot air circulation system that ensures that the hot air is distributed evenly throughout the tunnel, providing uniform heating and sterilization.
- Control system: This is a programmable logic controller (PLC) that regulates the temperature, conveyor belt speed, and other parameters of the depyrogenation process.
- Safety features: Interlocks, alarms, and emergency stop buttons are installed to ensure the safety of operators and prevent equipment damage.
- Validation system: A data logger with temperature sensors is used to monitor and record the temperature and other process parameters for validation purposes, ensuring that the depyrogenation process meets regulatory requirements.
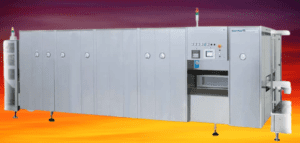
Endotoxin control in depyrogenation tunnels
Endotoxin control is a critical aspect of depyrogenation tunnels because endotoxins are a type of pyrogen that can cause fever and other adverse reactions in patients if present in pharmaceutical products. Endotoxins are produced by Gram-negative bacteria and are commonly found in the environment, including in the air, water, and soil.
To control endotoxins in de-pyrogenation tunnels, several measures can be taken, including:
- Proper cleaning and sanitization of the tunnel: A clean and sanitized tunnel reduces the risk of bacterial contamination and, consequently, endotoxin contamination.
- Regular maintenance and calibration of the equipment: Proper maintenance and calibration of the depyrogenation tunnel ensure that it is operating at its optimal performance and that the temperature and other critical parameters are accurate and consistent.
- Validation of the depyrogenation process: Validation of the depyrogenation process involves testing and monitoring the effectiveness of the tunnel in removing or inactivating endotoxins. This includes the use of biological indicators, such as bacterial endotoxin testing, to ensure that the process meets regulatory requirements.
- Use of high-efficiency particulate air (HEPA) filters: HEPA filters are used in depyrogenation tunnels to remove airborne particles, including endotoxins, from the air.
- Strict control of the manufacturing environment: Strict control of the manufacturing environment, including air quality, water quality, and personnel practices, can help minimize the risk of endotoxin contamination in pharmaceutical products.
depyrogenation tunnel Validation and Qualification
Validation Point | Description |
Heat Distribution | Ensuring that the heat is uniformly distributed throughout the tunnel and that all parts of the equipment being depyrogenated are exposed to the appropriate temperature for the required time. |
Temperature Uniformity | Ensuring that the temperature within the tunnel is consistent and maintained within a specified range. |
Cycle Time | Establishing the appropriate cycle time to achieve the desired level of pyrogen removal or inactivation. |
Conveyor Belt Speed | Verifying that the conveyor belt speed is consistent and that the equipment is processed at the appropriate speed. |
Biological Indicators | Using biological indicators, such as bacterial endotoxin testing, to confirm the effectiveness of the depyrogenation process. |
Validation of Cleaning Procedures | Ensuring that the tunnel is properly cleaned and sanitized to prevent cross-contamination or contamination of the equipment being depyrogenated. |
Operational Qualification | Ensuring that the depyrogenation tunnel is installed and functioning properly and meets the specified design requirements. |
Performance Qualification | Verifying that the depyrogenation tunnel consistently performs as intended and achieves the desired level of pyrogen removal or inactivation. |
Maintenance and Calibration | Ensuring that the tunnel is properly maintained and calibrated to ensure continued performance and accuracy. |
Environmental Monitoring | Monitoring the manufacturing environment, including temperature, humidity, and air quality, to ensure that the depyrogenation process is not compromised by external factors. |
Standard Operating Procedures | Developing and implementing standard operating procedures for the depyrogenation process to ensure consistency and compliance with regulatory requirements. |
Training | Providing training to operators and maintenance personnel to ensure proper use and maintenance of the depyrogenation tunnel. |
Documentation | Maintaining detailed documentation of the validation process, including protocols, reports, and any deviations or corrective actions taken. |
Regulatory Compliance | Ensuring that the depyrogenation process meets all applicable regulatory requirements, including those of the FDA, EMA, and other regulatory agencies. |
Revalidation | Conducting periodic revalidation to ensure that the depyrogenation process continues to perform as intended and meets regulatory requirements. |
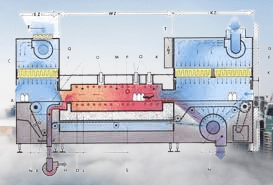
Frequently Asked Questions:
What is a depyrogenation tunnel?
Answer: depyrogenation tunnel is a specialized piece of equipment used in pharmaceutical manufacturing to remove pyrogens, including endotoxins, from equipment such as glassware and containers.
How does a depyrogenation tunnel work?
Answer: A depyrogenation tunnel works by exposing the equipment to high temperatures for a specific period of time, usually above 250°C, to destroy or inactivate pyrogens.
What are pyrogens?
Answer: Pyrogens are substances that can cause fever when introduced into the body. They can be found in various sources such as bacteria, bacterial endotoxins, and other microbial contaminants.
What are endotoxins?
Answer: Endotoxins are a type of pyrogen that are produced by Gram-negative bacteria and can cause fever and other adverse reactions in patients if present in pharmaceutical products.
How are endotoxins controlled in depyrogenation tunnels?
Answer: Endotoxins are controlled in depyrogenation tunnels by implementing measures such as proper cleaning and sanitization, regular maintenance and calibration, validation of the process, use of HEPA filters, and strict control of the manufacturing environment.
What is the temperature range for depyrogenation?
Answer: The temperature range for depyrogenation is usually above 250°C, with a typical range between 250-350°C.
What is the difference between depyrogenation and sterilization?
Answer: Depyrogenation is the process of removing or inactivating pyrogens from equipment, while sterilization is the process of killing or removing all microorganisms, including bacteria, viruses, and fungi, from equipment or surfaces.
What materials can be depyrogenated in a depyrogenation tunnel?
Answer: Materials that can be depyrogenated in a depyrogenation tunnel include glassware, containers, and other equipment used in pharmaceutical manufacturing.
How long does a depyrogenation cycle take?
Answer: The length of a depyrogenation cycle depends on several factors, including the equipment being depyrogenated, the temperature used, and the required level of pyrogen removal. Typical depyrogenation cycles range from 30 minutes to 2 hours.
What is the role of validation in depyrogenation tunnels?
Answer: The role of validation in depyrogenation tunnels is to test and monitor the effectiveness of the tunnel in removing or inactivating pyrogens, including endotoxins. This includes the use of biological indicators, such as bacterial endotoxin testing, to ensure that the process meets regulatory requirements.
What is the difference between depyrogenation tunnels and ovens?
Answer: Depyrogenation tunnels and ovens both use high temperatures to remove or inactivate pyrogens, but depyrogenation tunnels are typically larger and can process larger quantities of equipment. They also have a conveyor system that allows for continuous processing, while ovens are usually smaller and require batch processing.
What is the purpose of the cooling zone in a depyrogenation tunnel?
Answer: The purpose of the cooling zone in a depyrogenation tunnel is to cool down the equipment to a safe temperature before being unloaded.
How are depyrogenation tunnels cleaned and maintained?
Answer: Depyrogenation tunnels are cleaned and maintained by following the manufacturer’s instructions and standard operating procedures. This may include regular cleaning and sanitization, inspection and replacement of parts, and calibration of equipment.
What safety measures are in place in depyrogenation tunnels?
Answer: Safety measures in depyrogenation tunnels include interlocks, alarms, and emergency stop buttons to ensure the safety of operators and prevent equipment damage.
thanks, it is very good