The chemical and pharmaceutical sectors are big users of automatic ampoule inspection machines. Before releasing ampoules to the market, a highly advanced system called the Automated Ampoule Inspection Machine automatically tests them for contamination. After the successful filling of the ampoule by the filling machine, the ampoule will be inspected for different defects like sealing defects, glass particles, fibers, fill volume, and foreign particles. It can be altered to meet different medicinal needs. Together with other related characteristics, it has an autonomous vision system and a washing and drying system for ampoules. A sophisticated piece of machinery is the Automatic Ampoule Inspection Machine. This machine guarantees the greatest possible level of product quality.
Comparison Between Human & Automated Inspection
Machine | Humans |
Better sensitivity for some types of defects. | More flexible for new products and packages |
More repeatable process | Quicker response to new defect types |
Better efficiency, higher throughput | Cost-effective for small batches with slow rates |
Reduced ergonomic injury risk | Reference standard for all compendia |
Often higher false reject rate | – |
High initial cost (0.7 MM to 3.0 MM) | Low initial Cost |
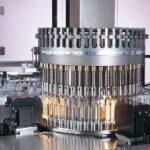
Description of the Automatic Ampoule Inspection Machine
Use the machine vision principle to identify and inspect the visible foreign matters; the testing products is stopped and to be motionless from high-speed rotation; capture images continually by the industrial camera; detect and inspect whether the products are qualified or not via computer system analyzing and comparing; and automatic classify the qualified and unqualified products.
Applications of the Automatic Ampoule Inspection Machine
- This machine can be used to inspect the liquid level and visible foreign particulates which the grain diameter
- or length is no less than 50um (such as chips of glass, metal filings, fibers, etc.);
- Inspect the appearance of the ampoule tip or vial cap (such as burnt spots, and shape defects);
- The machine can detect 1~5ml ampoule and vials;
- The machine can be used for the inspection of white bottles and brown bottles, colorless transparent liquid, and color transparent liquid.
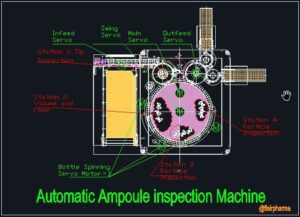
Working Principle of the Automatic Ampoule Inspection Machine
Feeding Device: Made by mesh belt, screw, and roller. Undetected products are transported to screw by mesh belt. The drive plate turns them into the roller. Use machine visual principle. Get the picture of the bottle from the imported industrial camera, and transfer the picture to the industrial computer. Foreign matter and disqualified products will be detected automatically.
Use machine visual principle. Transfer the light-protective picture to the industrial computer. The foreign matter will be detected automatically. Use the light radiation method to check the liquid level to separate the disqualified product. Separate the empty bottle with accuracy.
Light Radiation Method Use optical imaging to check the drawing defect and carbonization. Use all servo light sources and cameras to track the ampoule or vial system. Stable running and onsite picture.
The Machine has a high frame rate visual camera. 60 frames per second. Low loss ratio. Use LED light source control technology to extend service life.
Servo controls bottle circling. High circling accuracy, convenient and accurate speed adjustment, and stable picture. Equipped with online circling speed monitor function.
Equipped automatically adjust system on the bottle circling break point. Accurate control of the brake point for different size bottles. Improve the detection accuracy.
The bottle press system is easy and fasts to adjust without a tool. The separation device has a bottle separator and servo motor. The bottle separator has front and back channels. One channel is for qualified products. When meets unqualified products, the computer will control the servo to control the separator. Unqualified products will be turned into another channel. Has HP’s large high-speed graphics computer. Fast speed and high detection resolution. Equipped with real-time fault monitoring alarm. Offer the fault point on time. Have remote technical support and diagnosis. It is suitable for 1-20 ml. Easy for assembling and disassembling.
Specification of the Automatic Ampoule Inspection Machine
Number of Heads: 90
Environment temperature varies between 20~30
Relative humidity: 50%~60%
Power Supply380V ± 10%3Phase/50Hz;
Performance Specification of the Automatic Ampoule Inspection Machine:
Capacity Size Stable operation speed
1-2ml 600 bottles/min
3-5ml 450 bottles/min
Bottle broken rate ≤0.3‰
Missing inspection rate ≤0.5‰0.8‰
Suitable for ampoules and vials of 1-10ml
Stations Description of the Automatic Ampoule Inspection Machine:
- Bottle loading station
- Appearance inspection station
- Bottom lighting and side lighting inspection station 1
- Backlighting inspection station
- Bottom lighting and side lighting inspection station 2
- Qualified bottle output station
- Unqualified bottle-removing station
- Control system
- Machine frame and outer cover
- Main drive mechanism
- Tracing mechanism
Bottle Loading Station:
- This station includes a belt conveyor and bottle-loading star wheel.
- The belt conveyor adopts PU material and food grade belt; is driven by a gear motor, and can be frequency controlled.
- The belt conveyor adopts oil-free lubrication bearings.
- The material of the belt conveyor frame is SS304.
- Bottle loading star wheel adopts polyacetal material; white color.
- The Star wheel is driven by a gear set and main drive motor.
- There is an alarm function for lack of a bottle.
Appearance Inspection Station:
- This station inspects the bottle tip appearance of the bottle in the star wheel.
- Detect the appearance of ampoule tip or vial cap (such as burnt spot, and shape flaw).
- In this station, the bottle does not spin, use a reflective mirror; take 360-degree photographs of the ampoule tip or cap with one camera.
- The camera frequency is 15 frames.
Bottom and Side Lighting Inspection Station 1:
- Take photos of static bottles after high-speed rotation; rotation speed is 800~2000 R/Min.
- Ampoule/vial bottle rotation is driven by a servo motor.
- Light illuminate through the bottle from the bottom and side.
- There are two cameras to take photos of the bottle, the camera frequency is 30 frames.
- Press and rotate the ampoule/vial bottle at a high speed; the pressing force can be slightly adjusted prevent to breaking the bottle.
Back Lighting Inspection Station 1:
- Take photos of the static bottle after high-speed rotation, rotation speed is 800~2000 R/Min.
- Ampoule/vial bottle rotation is driven by a servo motor.
- Light illuminate through the bottle from the back side.
- There are two cameras to take photos of the bottle, The camera frequency is 30 frames,
- Press and rotate the bottle at a high speed; the pressing force can be slightly adjusted prevent to breaking the Bottle.
Bottom and Side Lighting Inspection Station 2:
- Take photos of static bottles after high-speed rotation; rotation speed is 800~2000 R/Min.
- Ampoule or vial bottle rotation is driven by a servo motor.
- Light illuminate through the ampoule or vial bottle from the bottom and side.
- There are two cameras to take photos of the bottle; the camera frequency is 30 frames.
- Press rotate the ampoule or vial bottle at a high speed; the pressing force can be slightly adjusted prevent to breaking the bottle.
Qualified Bottle Output Station
- This station conveys the qualified bottles to the main convoy system, Output the qualified bottle by the star wheel.
- Bottle loading star wheel adopts polyacetal material; white color.
- The Star wheel is driven by a gear set and main drive motor.
- The qualified ampoule or vial bottle is placed in the stainless steel trays.
Unqualified Bottle Remove Station
- This station removes the unqualified bottles from the main convoy system.
- Remove the unqualified bottles from the star wheel.
- It is driven by a servo motor.
- The unqualified ampoule or vial bottle is placed in the stainless steel trays.
Control System for the Automatic Ampoule Inspection Machine
- The control system consists of an operation interface, image processing Industrial Personal Computer (IPC), and electronic control system.
- The operation interface is a 19 inches touch screen.
- There are three Industrial Personal Computers to conduct the image processing.
- The motion controller is the core component of the electronic control system.
- The batch report can be printed out.
- The operation interface can be switched to English to show the production status, technical parameters, and also the process situation during running.
The software has the following functions of an Automatic Ampoule Inspection Machine:
- Unqualified images can be saved.
- A communication interface is reserved; remote monitoring can be achieved.
- Five-level operating authorities.
- Meet CFR21 Part 11 standard.
- A soft copy is provided.
- When the machine failure happens, it can be automatically stopped and alarm; the failure information is shown on the touch screen.
- The control system is equipped with a UPS, which can supply electricity for 20 mins after the power failure.
As per USP: As stated in Injections and Implanted Drug Products, all items intended for parenteral administration must be visually screened for the presence of particle matter.
As per WHO: Filled containers of parenteral products should be inspected individually for extraneous contamination or other defects the process should be validated and the performance of the equipment checked at intervals Results should be recorded.
Different OEMs for the Automatic Ampoule Inspection Machine:
World wide there are many manufacturers of Automatic Ampoule Inspection Machine, Some of the well-known manufacturers are:
- Trucking.
- Syntegon.
- NKP Pharma Private Limited.
- CMP PHAR.MA. SRL
FAQ For the Automatic Ampoule Inspection Machine:
What is the working principle of an Automatic Ampoule Inspection Machine?
Answer: The working principle of an Automatic Ampoule Inspection Machin is when the ampoules are feeding devices, Made of a mesh belt, screw, and roller. Undetected products are transported to screw by mesh belt. The drive plate turns them into the roller. Use machine visual principle. Get the picture of the bottle from the imported industrial camera, and transfer the picture to the industrial computer. Foreign matter and disqualified products will be detected automatically.
What is an automatic inspection machine?
Answer: As per the above information when the inspection of the filled ampoules is held with the help of an Automatic Ampoule Inspection Machine by cameras & automated techniques.
What are the advantages automated optical inspection?
Answer: The main advantage of automated optical inspection is better sensitivity for some types of defects. More repeatable process and quicker response. Better efficiency, higher throughput Cost-effective, Reduced ergonomic injury risk.
What is automatic inspection system?
Answer: Automatic inspection system is the system in which the inspection of the filled ampoules is held with the help of the Automatic Ampoule Inspection Machine. This is part of the manufacturing activity.
What is the important role in automated inspection ?
Answer: The automated inspection of the ampoules increase the quality of the product. Automatic Ampoule Inspection Machine has a more accurate and reliable solution with much productivity. Also, this will inspect very low micron particles in the glass ampoules.