Cleanroom validation is an essential process to ensure that cleanrooms meet the necessary standards for maintaining a controlled environment. This process involves testing and verifying the performance of the cleanroom and associated equipment, such as HVAC systems and filters. Cleanroom validation is particularly important in industries such as pharmaceuticals, biotech, and electronics, where even small levels of contamination can have a significant impact on product quality and safety.
Cleanroom Technology
Test | Description |
---|---|
Airflow velocity and direction | Measures the airflow velocity and direction to ensure proper circulation of air throughout the cleanroom, creating a controlled and uniform environment. |
Air changes per hour (ACH) | Measures the number of times that the entire volume of air within the cleanroom is replaced each hour, which helps to ensure that the cleanroom maintains the required levels of air cleanliness. |
Differential pressure | Measures the difference in pressure between the cleanroom and adjacent areas, which helps to ensure that contaminants from outside the cleanroom do not enter. |
Particle counts | Measures the levels of airborne particles within the cleanroom, which helps to ensure that the cleanroom meets the required standards for air cleanliness. |
Filter integrity | Ensures that air filters are functioning properly and removing particles from the air as intended. |
Temperature and humidity | Ensures that the cleanroom maintains the required conditions for manufacturing and storage of products. |
Microbial levels | Measures the number of viable microorganisms present within the cleanroom environment, which is particularly important for pharmaceutical and biotech applications. |
Recovery testing | Measures the time required for the cleanroom to return to its clean state after an outside disturbance, such as the opening of a door. |
Leak testing | Ensures that there are no leaks in the cleanroom enclosure that could allow contaminants to enter the cleanroom environment. |
Glove fingertip sampling | Measures the levels of viable microorganisms on the surface of gloves worn within the cleanroom environment. |
Surface sampling | Measures the levels of viable microorganisms on surfaces within the cleanroom environment, including floors, walls, and equipment. |
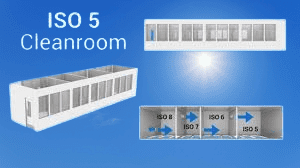
Cleanroom World & its Tests Limits
Test | Limits |
---|---|
Airflow velocity and direction | Velocity should be between 0.3 and 0.5 meters per second (60-100 feet per minute) with a uniform direction. |
Air changes per hour (ACH) | Generally, 20 ACH is recommended for ISO 5 areas (highest level of cleanliness) and 4-15 ACH for ISO 6 and ISO 7 areas. |
Differential pressure | Positive pressure should be maintained in the cleanroom to ensure that contaminants from adjacent areas do not enter. |
Particle counts | The maximum number of particles allowed depends on the classification of the cleanroom (e.g., ISO 5, ISO 6, etc.) and the particle size range being measured. For example, ISO 5 requires a maximum of 3,520 particles per cubic meter at 0.5 microns. |
Filter integrity | Filters should be tested to ensure that they are removing particles from the air as intended. Typically, the minimum efficiency required is 99.97% for particles 0.3 microns in size. |
Temperature and humidity | The temperature and humidity should be maintained within the required range for the manufacturing and storage of products. For example, a temperature range of 20-25°C (68-77°F) and a relative humidity range of 45-65% may be required. |
Microbial levels | The maximum allowable levels of viable microorganisms (e.g., bacteria, fungi) depend on the classification of the cleanroom and the type of product being manufactured. For example, ISO 5 may require a maximum of 1 CFU (colony forming unit) per cubic meter of air for bacteria and 1 CFU per 10 square centimeters of surface area for fungi. |
Recovery testing | The time required for the cleanroom to return to its clean state after an outside disturbance (e.g., door opening) should be within the required time frame. For example, ISO 5 may require a recovery time of no more than 3 minutes. |
Leak testing | No leaks should be present in the cleanroom enclosure that could allow contaminants to enter the cleanroom environment. |
Glove fingertip sampling | The maximum allowable levels of viable microorganisms on the surface of gloves worn within the cleanroom environment depend on the type of product being manufactured. |
Surface sampling | The maximum allowable levels of viable microorganisms on surfaces within the cleanroom environment depend on the type of product being manufactured and the classification of the cleanroom. For example, ISO 5 may require a maximum of 1 CFU per 10 square centimeters of surface area. |
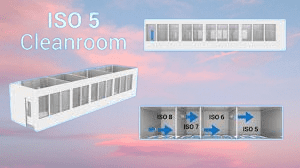
iso cleanroom standards
ISO Class | Maximum Particle Count (particles/m³) |
---|---|
1 | 10 |
2 | 100 |
3 | 1,000 |
4 | 10,000 |
5 | 100,000 |
6 | 1,000,000 |
7 | 10,000,000 |
8 | 100,000,000 |
The ISO cleanroom standards are widely used in various industries, including pharmaceuticals, medical devices, electronics, aerospace, and others, to ensure the quality and safety of products.
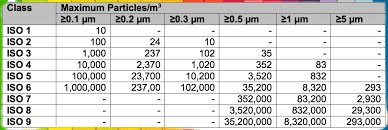
2 thoughts on “Cleanroom Validation 2023”