The FACTORY ACCEPTANCE TEST (FAT) document is the major document and part of the master validation plan in every pharmaceutical organization. It’s a process that is performed at the OEM factory/Site, a pre-check before the delivery of the machine to the pharma organization site. Below details of are factory acceptance test examples.
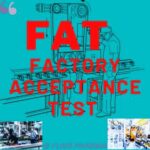
OBJECTIVE & SCOPE:
The main purpose of this document is to establish the factory acceptance test for the equipment. This document provides evidence & approval that the machine is manufactured as per the requirements approved in URS/ purchase order & DQ given by the pharma company to the machine manufacturer & verifies the features as agreed to be provided in the equipment by the manufacturer.
- This report covers the critical parameters, physical verification; MOC verification, installation and operational checks to be carried out at the manufacturers’ site during the inspection.
- This will ensure that appropriate interconnection or provision is made for utilities & that all safety features are defined before the equipment is despatched.
- This will ensure that the system meets the current good manufacturing practices requirements.
- This will identify & verify the key functions of the equipment.
- To establish that all the operations of the machine as specified in the DQ documents are met. FAT Qualification verifies that the machine has been installed in accordance with installation drawings and/or specifications.
- The FAT procedure is set for the complete satisfaction of the customer and to build the confidence of the user about the machine.
- To provide a record of the key features of the equipment and components installed
- Ensure that there is enough information available to enable the machine to operate and be maintained safely, effectively, and consistently.
- Confirm with Current Good Manufacturing Procedures (cGMP) requirements.
Scope: The scope of this FAT for the machine will cover the following elements:
- Verification of documents.
- Verification of machine nameplate.
- Verification of major bought-out components.
- Verification of sensors & alarm annunciators.
- Verification of components for calibration.
- Verification of safety components
- Verification of stickers and symbols.
- Verification of manually operated components.
- Verification of alarms and safety interlocks.
- Verification of user matrix & access level.
- Verification of performance test.
ACCEPTANCE CRITERIA:
- The equipment shall conform to the specifications and requirements specified in the design qualification.
- The physical verification of the subassemblies and parts shall be carried out in the manufacturer’s premises as per specifications and requirements.
- The performance test shall be demonstrated after installation at the site i.e. at the user’s Premises.
RESPONSIBILITIES:
Pharma Company: Provide complete technical specifications for design or approved design qualification document (DQ), along with Purchase Order approved from all concerned departments like QA, QC, Micro, Production Etc.
Qualify the equipment along with OEM.
OEM: To prepare FAT protocol according to design specifications / URS.
To manufacture and supply the equipment incorporating all the specifications as per purchase order and URS & DQ requirements.
To assist clients with successful installation & commissioning at the site.
To build the machine as per the scope of supply in accordance with PO/Contract.
Conduct FAT along with the Customer.
To prepare the report and organize the implementation of the recommendation made during FAT.
Revision Control:
Reason for Current Revision: To perform a factory acceptance test
Rev No. 00 Details of Revision
Technical specification & verification of major components:
- Equipment name:
- Equipment type:
- Machine size and machine layout
- Machine weight (Net)
- Machine weight (Gross)
- Working capacity
- Product container volume
- Material of construction
- Contact parts: SS 316l
- Non-contact parts: SS304
Manufacturing of Assemblies as per location:
- Main body: production area
- other units: technical area
- Control panel: production area, near equipment.
- Power Panel: technical area,
- Verification of major components
- Field instruments (electrical & pneumatic)
- Surface finishing & painting
- Safety features checklist
- Specific checkpoints
- Fat qualification checklist
- Dimensional checklist
- System inter-lock checklist
- Key functionality
Key functions: The key functions will be classified in specific headings. Each function test shall be recorded in a separate test data sheet specifying each test function, action, expected output/results, and actual output/results.
Functional Checks: To check and ensure that different functions for the correct operation of the subjected equipment/system are working as specified/expected.
Equipment / System Start-up: To check and establish the standard sequence to be followed for the start-up of the subjected equipment/system in Auto / Manual mode for correct operation and to avoid any damage to the product, equipment, and personnel.
Equipment / System Shut down: To check and establish the standard sequence to be followed for the shut-down of the subjected equipment/system in auto/manual/emergency mode to avoid any damage to the product, equipment, and personnel.
Safety features/security checks: To check and ensure that the safety/security functions (such as program logging, process control, personnel safety systems, etc) for the protection of the product, process, and personnel are working as specified/expected.
Deficiency and corrective action report:
- Description of deficiency and date observed.
- The person is responsible for corrective action and the date assigned.
- The person is responsible for corrective action and the date assigned.
Conclusion: The equipment is technically cleared for despatch
Factory acceptance test report approval:
APPROVED / NOT APPROVED
If approved The equipment is released for despatch.
Frequently Asked Questions:
If you want a draft copy or any other details about the Machine FAT document, please write us at: admin@flairpharma.com
1 thought on “FAT Best Value of Factory Acceptance Test 2023”