The acronym COBB stands for “Capacity (or Cobb) Absorbency Test,” named after its inventor, F.N. Cobb. The COBB test is used to measure the absorbency and resistance to liquid penetration of paper or paperboard materials.
The Cobb sizing test provides valuable insights into the suitability of paper materials for specific applications, allowing manufacturers to select materials that meet required standards for absorbency and resistance to moisture. Consequently, this test contributes significantly to quality control and assurance processes within the paper industry, ensuring that the paper and paperboard used for various purposes meet the necessary criteria for effective and reliable use.
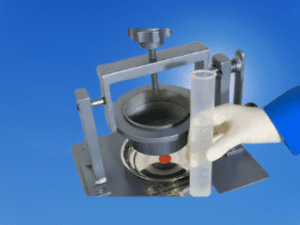
Working principle of the COBB Tester in the QC Lab
The COBB tester operates based on a relatively straightforward principle, aiming to measure the absorbency and resistance to liquid penetration of paper or paperboard materials. Here’s an overview of its working principle in the QC lab:
Principle of Operation:
- Sample Preparation: Paper or paperboard samples of a specified size are cut and placed on the testing platform of the COBB tester. The size is typically determined by the standardized requirements for the test.
- Liquid Application: A specific volume of the testing liquid (usually water) is poured into the liquid container of the COBB tester. This liquid is designed to simulate the conditions the paper might face in practical applications.
- Sample Exposure: The prepared sample is clamped securely onto the testing platform, ensuring it remains in position during the test. It’s crucial to avoid any sample movement that could affect the consistency of the results.
- Testing Duration: The timer on the COBB tester is set according to the standardized testing time for the specific test being conducted. This time is usually predetermined to maintain consistency in testing.
- Absorbency Measurement: The sample remains in contact with the testing liquid for the specified duration. After the test period, the sample is removed, and the weight of the liquid absorbed by the material is measured using the weighing scale integrated into the COBB tester.
- Result Analysis: The absorbed liquid weight indicates the material’s absorbency and its ability to resist liquid penetration. This value is then calculated and expressed in grams, providing a measurement known as the “Cobb value.”
Working Focus:
The key focus of the COBB tester’s operation is to simulate the impact of liquid exposure on paper or paperboard, enabling the evaluation of the material’s absorbency and its resistance to liquid penetration. The standardized procedure ensures consistency in testing, allowing for the comparison and assessment of different paper materials based on their Cobb values. This information is critical for various industries, especially in packaging, where the ability of the paper material to resist moisture is crucial for maintaining the quality and integrity of packaged products.
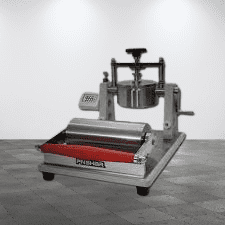
Major components of the COBB Tester:
Component | Description |
---|---|
Testing Platform | Flat, level surface where the paper or paperboard sample is placed for the test. |
Testing Liquid Container | Holds the specific liquid (e.g., water) used to wet the paper sample during the test. |
Clamping Mechanism | Holds the paper sample securely in place during the wetting process to ensure consistency. |
Timing Mechanism | Controls the duration of exposure to the testing liquid, typically standardized for accuracy. |
Weighing Scale | Measures the weight of the paper before and after exposure to determine liquid absorption. |
Sizing Area Template | Defines the area of the paper to be wetted, ensuring a standardized testing sample size. |
Control Panel/Interface | Allows for setting test parameters, initiating the test, and displaying test results. |
Data Display Screen | Shows pertinent information such as test duration, absorbed liquid weight, and test status. |
Technical specifications of the COBB Tester
Technical Details | Specification |
---|---|
Testing Standards | Complies with industry standards such as TAPPI (Technical Association of the Pulp and Paper Industry) or ISO (International Organization for Standardization). |
Sample Size | Standard sample size typically ranges from 10 to 200 square centimeters. |
Testing Liquid Volume | Controlled volume applied uniformly over the paper surface, often standardized (e.g., 100 mL). |
Test Duration | Typically lasts for a standardized time (e.g., 60 seconds) to ensure consistent testing. |
Accuracy | Precision measuring scale ensures accurate weight readings to within a few decimal places. |
Resolution | The measuring scale can have a resolution of up to 0.01 grams for precise measurements. |
Calibration | Periodic calibration to maintain accuracy and adherence to testing standards. |
User Interface | User-friendly interface for setting parameters, initiating tests, and viewing results. |
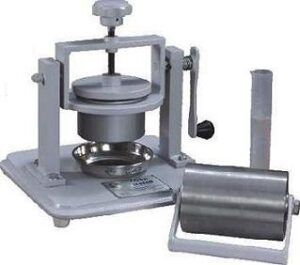
Benefits of the performing Cobb size test:
Benefits of Cobb Sizing Test | Explanation |
---|---|
Quality Assessment | Provides an effective method to evaluate the quality of paper and paperboard in terms of its absorbency, ensuring consistency in the material’s ability to resist liquid penetration. |
Packaging Integrity | Ensures the paper’s capacity to maintain its structure and integrity, particularly in packaging applications, preventing undesirable liquid ingress and maintaining the quality of packaged contents. |
Product Protection | Safeguards sensitive products, such as food items and pharmaceuticals, by determining the material’s ability to resist moisture, ensuring the preservation of product quality and safety. |
Standardization | Helps in setting standardized parameters for the quality of paper and paperboard, allowing for consistency in manufacturing and product performance, meeting industry standards and specifications. |
Material Selection | Aids in the selection of appropriate paper materials for specific applications based on their absorbency characteristics, ensuring the chosen materials meet the required criteria for intended use. |
Quality Control | Forms an integral part of quality control processes within the paper industry, enabling manufacturers to validate the suitability of materials, ensuring they meet the necessary standards for absorbency and resistance to liquid penetration. |
Enhanced Performance | Allows manufacturers to create and maintain high-performance paper and paperboard products that deliver reliable moisture resistance, supporting various industries’ needs for dependable packaging materials. |
Customer Satisfaction | Contributes to customer satisfaction by delivering products made from materials that have undergone stringent testing, ensuring the quality and performance of the paper-based materials used in products. |
Frequently Asked Questions:
What is Cobb tester?
Answer: The Cobb tester is an apparatus used in the paper and packaging industry to measure the absorbency and resistance to liquid penetration of paper or paperboard materials.
What is the purpose of Cobb sizing tester?
Answer: The Cobb sizing tester is used to assess the absorbency and the ability of paper or paperboard to resist liquid penetration. Its primary purpose is to evaluate the material’s effectiveness in preventing liquid ingress, especially in applications like packaging.
How do you test Cobb value?
Answer: The Cobb value is tested by placing a specific area of paper or paperboard in contact with a testing liquid (usually water) for a defined duration. The weight of the liquid absorbed by the material during this period is then measured to determine its Cobb value.
What is Cobb value?
Answer: The Cobb value is a measure of the weight of liquid, typically expressed in grams, absorbed by a specific area of paper or paperboard during a standardized Cobb test. It indicates the material’s ability to resist liquid penetration and is crucial in assessing its quality for various applications.
What is the ISO standard for Cobb test?
Answer: The International Organization for Standardization (ISO) standard for the Cobb test is ISO 535, titled “Paper and board – Determination of water absorptiveness – Cobb method.”
What is the Tappi method of Cobb test?
Answer: The Technical Association of the Pulp and Paper Industry (TAPPI) also has a standardized method for the Cobb test. TAPPI T 441 is the method used for measuring the water absorptiveness of sized papers using the Cobb test.
What is Tappi testing?
Answer: TAPPI, known as the Technical Association of the Pulp and Paper Industry, conducts various standardized testing procedures to evaluate the properties and quality of pulp, paper, and related materials. These tests, such as the Cobb test, aim to ensure industry-wide standards and consistency in paper and pulp product quality assessment.
What is a COBB tester used for?
Answer: The COBB tester is used to measure the absorbency and resistance to liquid penetration of paper or paperboard materials.
How does a COBB tester function?
Answer: A COBB tester involves placing a specific area of paper or paperboard in contact with a testing liquid for a set duration. The weight of the liquid absorbed by the material is then measured to determine its absorbency.
What types of industries commonly use the COBB tester?
Answer: Industries such as paper manufacturing, packaging, printing, and pharmaceuticals often use the COBB tester to assess the absorbency of paper-based materials for various applications.
Why is the COBB test essential in the paper industry?
Answer: The COBB test is crucial in the paper industry as it evaluates the paper’s ability to resist liquid penetration, maintaining its integrity, and is vital in assessing the paper’s suitability for packaging and various applications.
What factors does the COBB test measure?
Answer: The COBB test measures the absorbency and penetration resistance of paper, providing information on its ability to repel liquids and maintain its structural integrity.
How is the COBB test result expressed?
Answer: The COBB test result is expressed in grams and indicates the weight of liquid absorbed by a defined area of the paper or paperboard material during the test.
What are the potential consequences of poor paper absorbency in industries?
Answer: Poor paper absorbency can result in compromised packaging, reduced product protection, and potential damage to enclosed items due to increased moisture penetration.
What parameters need to be considered during COBB testing?
Answer: Parameters such as standardized sample size, type and volume of testing liquid, test duration, and environmental conditions need consideration for accurate COBB testing.
How does the COBB test benefit the quality control process in the paper industry?
Answer: The COBB test ensures that paper and paperboard materials meet specific absorbency and penetration resistance standards, maintaining quality and consistency in manufacturing.
What maintenance practices are recommended for a COBB tester?
Answer: Regular calibration, cleaning after each use, adherence to manufacturer’s guidelines, and following a maintenance schedule are essential for the upkeep of a COBB tester to ensure accurate testing results.
Standard Operating Procedures (SOP) for Operating and Cleaning the COBB Tester in the QC Lab
Objective: To provide a systematic guide for the proper operation and cleaning of the COBB tester in the Quality Control (QC) laboratory, ensuring accurate and reliable testing of paper absorbency and penetration resistance.
Equipment Required:
- COBB tester
- Testing liquid (e.g., water)
- Lint-free cloth
- Mild cleaning solution
- Distilled water
- Protective gear (gloves, goggles, lab coat)
Operating the COBB Tester
Preparation:
- Environment Check: Ensure the work area is clean, organized, and free from any potential contaminants.
- Calibration Check: Verify that the COBB tester is calibrated as per the manufacturer’s guidelines. If not, contact the responsible personnel to conduct calibration.
- Safety Gear: Wear the necessary protective gear, including gloves and goggles, before handling the equipment.
Operation:
- Sample Preparation: Cut the paper or paperboard samples according to the specified size and shape using the sizing template provided with the tester.
- Liquid Dispensing: Pour the specified amount of testing liquid into the testing liquid container of the COBB tester.
- Placing the Sample: Securely place the prepared sample on the testing platform, ensuring it fits within the designated sizing area.
- Clamping: Use the clamping mechanism to secure the sample in place to avoid any movement during the test.
- Testing Duration: Set the timer or duration on the COBB tester according to the standard testing time required for the specific test.
- Initiating Test: Start the test and allow the sample to be in contact with the liquid for the specified duration.
- Record Results: Note the absorbed liquid weight displayed on the weighing scale to determine the material’s absorbency.
- Clean-Up: Remove the sample, dry the testing platform, and clean the equipment thoroughly after each test.
Cleaning the COBB Tester
Post-Operation:
- Power Off: Turn off the COBB tester and disconnect from the power source.
- Liquid Disposal: Properly dispose of the used testing liquid according to the lab’s waste disposal guidelines.
- Cleaning Procedure:
- Dampen a lint-free cloth with a mild cleaning solution.
- Gently wipe the testing platform, liquid container, and all accessible areas of the COBB tester to remove any residues.
- Use distilled water on a separate cloth to wipe away any remaining cleaning solution.
- Ensure all parts are completely dry before the next use.
- Documentation: Record the cleaning activity in the equipment logbook, including date, time, and the name of the personnel performing the cleaning.
Note: Regular maintenance and calibration schedules should be followed as per the manufacturer’s recommendations to ensure the proper functioning of the COBB tester.
This Standard Operating Procedure (SOP) for the operation and cleaning of the COBB tester in the QC lab serves as a guideline to ensure accurate and consistent testing while maintaining the equipment in good working condition.