Fault Tree Analysis (FTA) is a deductive failure analysis technique used to identify and analyze factors that can lead to a specific undesirable event (referred to as the “top event”). Originally developed for the aerospace industry in the 1960s, FTA has since been adapted for use in various fields, including pharmaceuticals. In the context of pharmaceutical manufacturing, FTA helps ensure product quality and safety by systematically identifying potential causes of failure and their relationships.
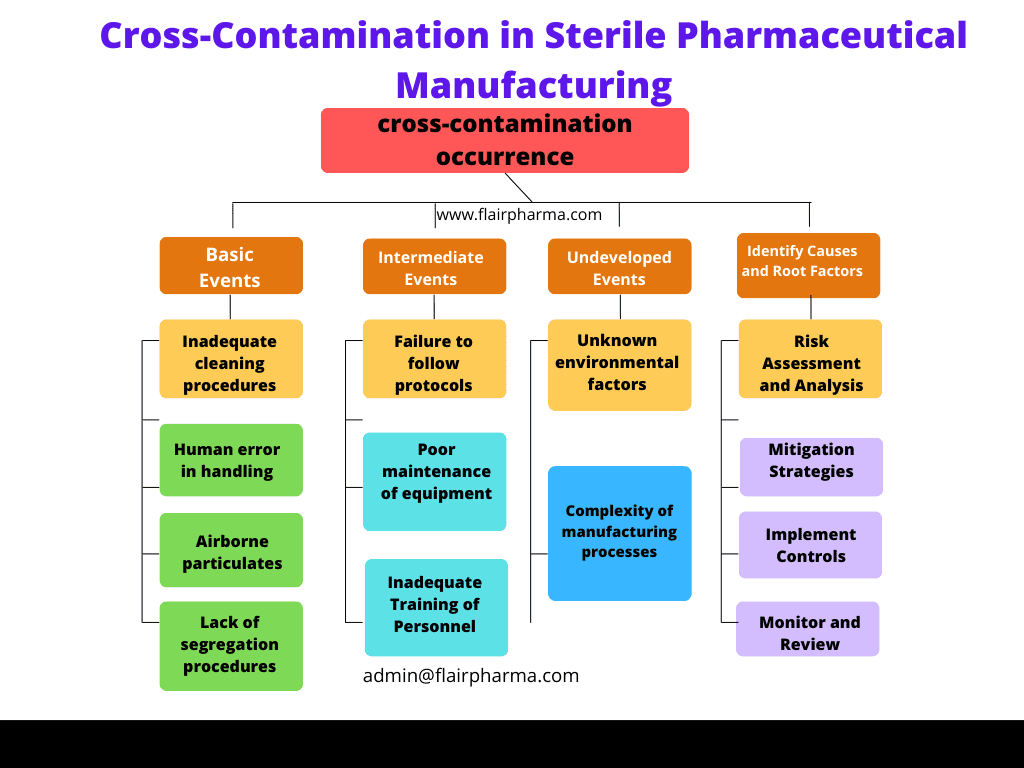
Concept of Fault Tree Analysis
FTA involves constructing a fault tree diagram that visually represents the logical relationships between different events and their causes. The process begins with defining the top event, which is the failure or undesirable outcome that needs to be prevented. The analysis then works backward, identifying intermediate events and basic events that can contribute to the top event. These events are connected using logical gates such as AND, OR, and NOT to depict their interdependencies.
Basic Components of FTA
- Top Event: The primary failure or undesirable event being analyzed.
- Intermediate Events: Events that lie between the basic events and the top event.
- Basic Events: The root causes or initiating events that can lead to intermediate events or the top event.
- Logical Gates:
- AND Gate: All input events must occur for the output event to occur.
- OR Gate: At least one input event must occur for the output event to occur.
- NOT Gate: The output event occurs if the input event does not occur.
Application of FTA in Pharmaceutical Manufacturing
Pharmaceutical manufacturing is a highly regulated industry with stringent quality and safety standards. FTA can be applied at various stages of the manufacturing process to identify potential failure modes, assess risks, and implement corrective actions. Here are some key areas where FTA can be beneficial:
1. Process Design and Development
During the design and development of manufacturing processes, FTA can be used to anticipate potential failures and design robust processes. For instance, when developing a new drug formulation, FTA can help identify critical process parameters and potential sources of variability that could impact product quality.
2. Equipment Validation and Maintenance
Pharmaceutical manufacturing relies on complex equipment that must operate reliably to produce high-quality products. FTA can be used to analyze equipment failure modes and develop preventive maintenance strategies. By understanding the potential causes of equipment failure, manufacturers can schedule maintenance activities to minimize downtime and avoid production disruptions.
3. Quality Control and Assurance
Quality control (QC) and quality assurance (QA) are critical components of pharmaceutical manufacturing. FTA can be used to analyze potential failures in QC and QA processes, such as errors in analytical testing, contamination risks, and deviations from standard operating procedures (SOPs). By identifying these risks, manufacturers can implement controls to ensure consistent product quality.
4. Risk Management
Risk management is an essential part of pharmaceutical manufacturing, encompassing the identification, assessment, and mitigation of risks. FTA provides a structured approach to risk management by systematically identifying potential failure modes and their consequences. This helps manufacturers prioritize risks and allocate resources effectively to mitigate them.
Steps in Conducting Fault Tree Analysis
Conducting FTA involves several steps, from defining the scope of the analysis to implementing corrective actions. Here is a step-by-step guide to performing FTA in a pharmaceutical manufacturing setting:
1. Define the Top Event
The first step in FTA is to clearly define the top event, which is the failure or undesirable outcome that needs to be analyzed. In pharmaceutical manufacturing, the top event could be a product defect, contamination, equipment failure, or any other critical event that could impact product quality or patient safety.
2. Identify Intermediate and Basic Events
Next, identify the intermediate and basic events that can contribute to the top event. This involves brainstorming potential causes and breaking them down into more specific events. It is important to consider all possible factors, including human error, equipment malfunctions, environmental conditions, and process variations.
3. Construct the Fault Tree Diagram
Using the identified events, construct the fault tree diagram by connecting the events with logical gates. The diagram should visually represent the relationships between the events and how they contribute to the top event. Ensure that all possible pathways leading to the top event are included in the diagram.
4. Analyze the Fault Tree
Once the fault tree diagram is constructed, analyze it to identify critical events and pathways. This involves evaluating the probability and impact of each event and pathway. Quantitative analysis can be performed using probability data and reliability models to assess the likelihood of the top event occurring.
5. Identify and Implement Corrective Actions
Based on the analysis, identify corrective actions to address the critical events and pathways. This may include process improvements, equipment upgrades, training programs, and changes to SOPs. Implement the corrective actions and monitor their effectiveness to ensure that the risks are mitigated.
6. Review and Update the Fault Tree
FTA is an iterative process that requires regular review and updates. As new information becomes available or as changes are made to the manufacturing process, update the fault tree diagram to reflect the current state of the process. This ensures that the analysis remains relevant and effective in identifying and mitigating risks.
Case Study: FTA in Sterile Pharmaceutical Manufacturing
To illustrate the application of FTA in pharmaceutical manufacturing, let’s consider a case study involving a sterile manufacturing process. The top event in this case is the contamination of a sterile product, which can have serious implications for patient safety.
Step 1: Define the Top Event
The top event is defined as “contamination of the sterile product.”
Step 2: Identify Intermediate and Basic Events
Potential causes of contamination are identified, including:
- Equipment failure (e.g., sterilizer malfunction)
- Human error (e.g., improper aseptic technique)
- Environmental factors (e.g., HVAC system failure)
- Raw material contamination
Step 3: Construct the Fault Tree Diagram
The fault tree diagram is constructed with the top event at the top, followed by intermediate events such as equipment failure, human error, environmental factors, and raw material contamination. Basic events, such as specific equipment malfunctions, operator mistakes, and environmental conditions, are connected to the intermediate events using logical gates.
Step 4: Analyze the Fault Tree
The fault tree is analyzed to identify critical events and pathways. Quantitative analysis is performed using historical data on equipment reliability, human error rates, and environmental conditions. This helps prioritize the events based on their likelihood and impact.
Step 5: Identify and Implement Corrective Actions
Corrective actions are identified for the critical events. For example, to address equipment failure, preventive maintenance schedules are implemented, and redundant systems are installed. To reduce human error, additional training programs and automated processes are introduced. Environmental controls are enhanced by upgrading the HVAC system and implementing stricter monitoring protocols.
Step 6: Review and Update the Fault Tree
The fault tree is reviewed and updated regularly to reflect changes in the process and new information. This ensures that the analysis remains current and effective in preventing contamination.
Benefits of FTA in Pharmaceutical Manufacturing
FTA offers several benefits for pharmaceutical manufacturing, including:
- Systematic Risk Identification: FTA provides a structured approach to identifying potential failure modes and their causes, ensuring that all possible risks are considered.
- Enhanced Process Understanding: By analyzing the relationships between different events, FTA helps manufacturers gain a deeper understanding of their processes and the factors that can impact product quality.
- Improved Risk Management: FTA enables manufacturers to prioritize risks and allocate resources effectively to mitigate them, reducing the likelihood of failures and improving overall process reliability.
- Regulatory Compliance: FTA supports compliance with regulatory requirements by providing a documented and systematic approach to risk assessment and mitigation.
- Continuous Improvement: FTA is an iterative process that promotes continuous improvement by regularly reviewing and updating the analysis to reflect changes in the process and new information.
Challenges and Limitations of FTA
While FTA offers many benefits, it also has some challenges and limitations:
- Complexity: Constructing and analyzing fault trees for complex processes can be time-consuming and require specialized knowledge.
- Data Availability: Quantitative analysis requires reliable data on the probability and impact of events, which may not always be available.
- Subjectivity: The identification of events and their relationships can be subjective, potentially leading to incomplete or biased analysis.
- Dynamic Nature of Processes: Manufacturing processes can change over time, requiring regular updates to the fault tree to ensure its relevance and accuracy.
Conclusion:
Fault Tree Analysis is a valuable tool for pharmaceutical manufacturing, providing a systematic approach to identifying and analyzing potential failure modes and their causes. By applying FTA, manufacturers can enhance process reliability, improve risk management, and ensure compliance with regulatory requirements. Despite its challenges, FTA offers significant benefits in maintaining product quality and safety, ultimately contributing to better patient outcomes.
Frequently Asked Questions (FAQ’s)
What is fault tree analysis in pharma?
Answer: Fault Tree Analysis (FTA) in pharmaceuticals is a systematic method used to analyze the causes of failures in manufacturing processes. It identifies potential faults and their interrelationships to ensure product quality and regulatory compliance.
What is the purpose of a fault tree analysis?
Answer: The purpose of FTA is to identify and evaluate the root causes of a specific undesirable event (top event) and to assess the probability and impact of these causes to prevent failures and improve system reliability.
What is the FTA used for?
Answer: FTA is used for risk assessment, failure analysis, and reliability engineering. It helps in identifying potential failure points, assessing the likelihood of failures, and implementing corrective actions to mitigate risks.
What is fault tree analysis in chemical process?
Answer: In chemical processes, FTA is used to analyze and prevent potential failures that could lead to accidents, equipment malfunctions, or process deviations. It ensures safety and efficiency by identifying and mitigating risks.
How to calculate fault tree analysis?
Answer: FTA calculation involves quantifying the probabilities of basic events and using Boolean algebra to combine these probabilities through logical gates (AND, OR). This provides the overall probability of the top event occurring.
What is the difference between fault tree and FMEA?
Answer: FTA is a top-down, deductive method focusing on a single failure event and its causes, while Failure Mode and Effects Analysis (FMEA) is a bottom-up, inductive approach that identifies potential failure modes of individual components and their effects on the system.
What is the use of fault analysis?
Answer: Fault analysis is used to identify, evaluate, and mitigate potential faults in systems and processes. It helps in enhancing reliability, safety, and performance by preventing failures and reducing their impact.
How to build a fault tree analysis?
Answer:
- Define the top event.
- Identify intermediate and basic events.
- Connect events using logical gates.
- Analyze the fault tree for critical paths.
- Implement corrective actions.
- Review and update the fault tree regularly.
What is fault tree analysis or symbol?
Answer: FTA uses specific symbols for different events and gates:
- Basic Event: Circle
- Intermediate Event: Rectangle
- AND Gate: Flat-topped symbol
- OR Gate: Curved-topped symbol
What is FTA used for?
Answer: FTA is used for identifying potential failure causes, assessing risk, and improving reliability in various industries, including pharmaceuticals, aerospace, and chemical processes.
What is the main purpose of FTA?
The main purpose of FTA is to prevent failures by systematically identifying their root causes, evaluating their probabilities, and implementing effective mitigation strategies.
What are the basics of FTA?
- Define the top event.
- Identify contributing events.
- Use logical gates to connect events.
- Perform quantitative and qualitative analysis.
- Implement corrective measures.
Is FTA inductive or deductive?
Answer: FTA is a deductive method. It starts with a general undesirable event and works backward to identify specific causes.
What is a common cause fault tree analysis?
Answer: Common cause fault tree analysis examines failures caused by common factors or events that affect multiple components simultaneously, enhancing understanding of systemic vulnerabilities.
Is a fault tree analysis qualitative or quantitative?
Answer: FTA can be both qualitative and quantitative. Qualitative FTA identifies potential causes and relationships, while quantitative FTA assigns probabilities to events and calculates the likelihood of the top event.