Safety shower systems in pharmaceutical settings exhibit a remarkable degree of complexity, embodying the perplexity necessary for optimal performance. These systems consist of a network of intricate piping, valves, and controls, designed to deliver a continuous flow of water in emergency situations. The complexity lies in the careful integration of these components to facilitate rapid decontamination, ensuring that any hazardous substances are thoroughly rinsed off the affected individuals.
Types of safety shower
There are several types of safety showers designed to meet specific safety needs in different environments. Here are some common types of safety showers:
- Standard Safety Showers:
- These showers are the most widely used and consist of a fixed overhead shower head that delivers a large volume of water in a uniform pattern. They are typically activated by pulling a handle or chain, and they provide thorough rinsing to remove hazardous substances from the body.
- Combination Showers:
- Combination showers are equipped with both a shower head and an integrated eyewash station. They offer a comprehensive solution for emergency decontamination, providing simultaneous rinsing for the body and irrigation for the eyes in case of exposure to hazardous materials.
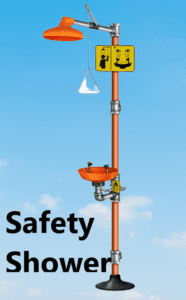
- Plumbed Safety Showers:
- Plumbed safety showers are connected directly to a water supply system. They ensure a continuous flow of water during emergencies, eliminating the need for manual refilling or limited water capacity. Plumbed showers are commonly found in facilities where a constant water supply is readily available.
- Tank-Type Safety Showers:
- Tank-type safety showers feature an integrated water tank that stores a certain volume of water for emergency use. These showers are particularly suitable for locations with limited water supply or areas where plumbing connections are not feasible.
- Mobile Safety Showers:
- Mobile safety showers are portable units designed for temporary or remote work environments. They are equipped with wheels or handles, allowing them to be easily transported to different locations as needed. Mobile safety showers provide flexibility in situations where a fixed shower installation is not practical.
- Freeze-Protected Safety Showers:
- Freeze-protected safety showers are specifically designed for use in cold environments where water lines may be at risk of freezing. These showers are equipped with insulation and heating elements to ensure that the water supply remains unfrozen and readily available during low-temperature conditions.
- Decontamination Showers:
- Decontamination showers are specialized units used in environments where workers may be exposed to hazardous substances or chemicals. They feature multiple showerheads strategically positioned to provide comprehensive rinsing and decontamination.
Safety shower parts name
Safety Shower Parts | Description |
---|---|
Shower Head | A device that releases a high-volume flow of water for rinsing |
Pull Handle/Chain | Mechanism to activate the flow of water in case of emergency |
Shower Pipe | Vertical pipe connecting the shower head to the water supply |
Valve | Controls the water flow to the shower head |
Piping | Network of pipes that deliver water to the shower head |
Mixing Valve | Adjusts the water temperature to prevent scalding |
Signage | Clearly visible signs indicating the location of the shower |
Drain | Allows water to drain away from the shower area |
Activation Alarm | Optional alarm system to alert others when the shower is used |
Safety Eyewash Station | Additional eyewash station attached to the safety shower |
Foot Treadle | Alternative activation method using foot pressure |
Drench Hose | Flexible hose with a nozzle for targeted rinsing |
Pressure Gauge | Indicates the water pressure in the system |
Safety Shower Enclosure | The vertical pipe connecting the shower head to the water supply |
Safety shower test kit
A safety shower test kit is an essential tool used to verify the proper functioning and readiness of safety shower systems. It allows organizations and facility managers to perform regular testing and maintenance of safety showers to ensure they are in optimal working condition.
A typical safety shower test kit may include the following components:
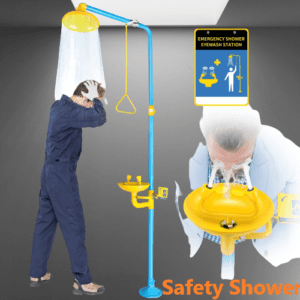
- Test Manifold: The test manifold is a device that connects to the safety shower system and allows for controlled testing and flow measurements.
- Flow Meter: A flow meter is used to measure and monitor the water flow rate from the safety shower. It provides accurate readings to ensure that the flow meets the required standards.
- Pressure Gauge: The pressure gauge is used to measure the water pressure within the safety showr system. It helps verify that the pressure is within the acceptable range for effective operation.
- Temperature Strip: A temperature strip is often included to check the temperature of the water being delivered by the safety showr. It ensures that the water is within the recommended temperature range for the comfort and safety of the individuals using the shower.
- Test Buckets or Containers: Test buckets or containers are used to collect and measure the water discharged from the safety showr during the testing process. They help assess the flow rate and ensure that an adequate volume of water is being delivered.
- Testing Instructions: The safety showr test kit typically includes detailed instructions on how to perform the tests, interpret the results, and maintain the safety showr system effectively. These instructions provide guidance to the user and ensure standardized testing procedures.
- Carrying Case: To keep all the components organized and easily transportable, a carrying case is often provided with the safety showr test kit. It allows for convenient storage and ensures that the kit is readily available when needed.
By utilizing a safety showr test kit on a regular basis, organizations can confirm that their safety showr systems are functioning properly and can promptly address any issues that may arise. This proactive approach helps maintain a safe working environment and ensures that the safety showrs are prepared to effectively respond to emergencies and protect the well-being of workers.
Applications of safety shower
Industry/Environment | Application of Safety Showers |
---|---|
Laboratories | Emergency decontamination of personnel exposed to hazardous substances |
Manufacturing Plants | Quick rinsing and removal of chemicals, oils, or other contaminants from the body |
Chemical Plants | Immediate response to chemical spills or splashes on workers’ bodies |
Oil and Gas Facilities | Decontamination of personnel exposed to hazardous materials or hydrocarbons |
Construction Sites | Rapid rinsing of workers involved in accidents or incidents involving hazardous substances |
Research Facilities | Emergency showering for personnel handling hazardous or toxic materials |
Pharmaceuticals | Decontamination of workers in case of accidental contact with chemicals or hazardous drugs |
Mining Operations | Quick removal of harmful substances from miners’ bodies after accidents or exposure incidents |
Agriculture | Emergency showering to rinse off pesticides, fertilizers, or other agricultural chemicals |
Hospitals | Decontamination of staff exposed to hazardous chemicals or infectious materials |
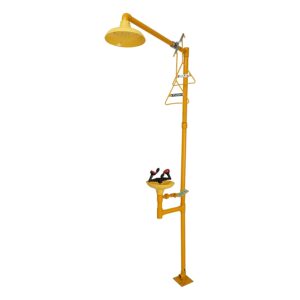
Important topics:
Frequently Asked Questions
What is the recommended water flow rate for a safety shower?
Answer: The recommended water flow rate for a safety showr is typically between 75-113 liters (20-30 gallons) per minute.
What is the purpose of a mixing valve in a safety shower?
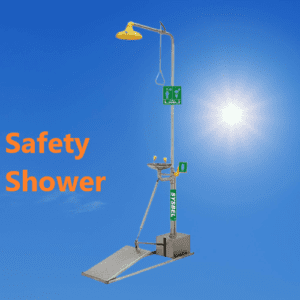
Answer: The mixing valve in a safety showr is used to regulate and control the water temperature to prevent scalding or discomfort during use.
What are the minimum requirements for the water temperature in a safety shower?
Answer: The ANSI Z358.1 standard recommends that the water temperature in a safety showr should be tepid, between 16-38°C (60-100°F).
How often should safety showers be tested and inspected?
Answer: Safety showrs should be tested and inspected on a regular basis, typically once a week, to ensure they are in proper working condition.
What is the role of an activation alarm in a safety shower system?
Answer: An activation alarm is an optional feature in safety showrs that alerts nearby personnel when the shower is activated, helping to summon assistance and enhance emergency response.
What is the required duration for operating a safety shower during testing or an actual emergency?
Answer: Safety showrs should be capable of providing a continuous flow of water for a minimum of 15 minutes to effectively rinse and decontaminate affected individuals.
What are the guidelines for the location and accessibility of safety showers?
Answer: Safety showrs should be located within a 10-second travel distance (approximately 15 meters or 55 feet) from areas where hazardous materials are handled, and they should be easily accessible and clearly marked.
Can safety showers be installed outdoors?
Answer: Yes, safety showrs can be installed outdoors, but they should be designed and protected to prevent freezing, overheating, or damage from environmental elements.
Are there any specific requirements for the height and coverage area of a safety shower’s spray pattern?
Answer: The ANSI Z358.1 standard recommends that safety showrs provide a spray pattern that covers the entire body from the neck down and that the shower head height be positioned at a minimum of 203 cm (80 inches) above the floor.
What are the maintenance requirements for safety showers?
Answer: Safety showrs should undergo regular maintenance, including flushing of water lines, testing of valves and controls, inspection of plumbing connections, and replacement of any worn or damaged parts. Maintenance activities should follow manufacturer guidelines and applicable regulatory standards.