The purpose of this Standard Operating Procedure for Preventive Maintenance of Dispensing and Sampling Booth is to provide guidelines and instructions for the preventive maintenance of the Dispensing and Sampling Booth to ensure its optimal performance, cleanliness, and compliance with quality and safety standards.
SOP for Preventive Maintenance of Dispensing and Sampling Booth
- OBJECTIVE:
- To lay down the Procedure for Preventive Maintenance of Dispensing and Sampling Booth.
- SCOPE:
- This SOP is applicable to the Preventive Maintenance of Dispensing and Sampling Booth installed .
- RESPONSIBILITY:
- Technician/ Operator / Engineer / User shall be responsible for proper execution of preventive maintenance as per SOP.
- Engineering – Head shall be responsible for reviewing the SOP and for ensuring proper execution of preventive maintenance
- ACCOUNTABILITY:
- Engineering – Head shall be accountable for proper implementation of the SOP.
- DEFINITIONS:
- Nil
- PROCEDURE:
- Preventive maintenance shall be executed as per the SOP No.: SOP/EN/XXXYYY – Execution of Preventive Maintenance.
- Ensure that the spare parts are available at the time of preventive maintenance.
SOP for Preventive Maintenance of Dispensing and Sampling Booth and its checklist
- Preventive Maintenance: – Mechanical
- Clean the pre-filters and fine filters
- Mention filter cleaning procedure is applicable for QC and warehouse areas. Remaining area sampling and dispensing booth filter cleaning is carried out inside the area as per user respective SOP.
- User will provide the pre and fine filter intact in poly bag to HVAC operator for cleaning as per below mention procedure.
- With the help of spanner, loosen the front plate on to the pre and fine filter.
- Remove the front plate from the front side.
- Remove the filter manually with utmost care.
- Check the filter and clean the filter as per filter cleaning SOP No. SOP/EN/XXXYYY.
- After cleaning the pre and fine filter mount the pre and fine filter with utmost care.
- After proper adjustment, attach the front plate.
- With the help of spanner, tighten the front plate on to the pre and fine filter.
- Checking of the pre and fine filter frequency shall be every three months.
- Filter cleaning should be carried out if Pressure drops across the pre and fine filters on “breakdown requisition memo” or define frequency whichever will occur first.
- Check the installed instruments
- Ensure the installed instruments are calibrated.
- Check the end connections of instruments; if required tighten the same.
- The checking of frequency shall be after every six months.
- Lubrication of motor bearings
- Check the lubrication of blower motor bearings, if required do the lubrication with recommended lubricant.
- The frequency of checking of lubrication shall be after every three months.
- Preventive Maintenance – Electrical
- Checking of terminations and wiring
- Ensure that the power supply to the machine is switched OFF.
- Visually check all the power and control wiring and terminations in the electrical panel and for control elements mounted on the machine for any loose connection and damage.
- Check and ensure by using the screwdriver that all the wires are properly tightened at the distribution terminals inside the electrical panel and on the terminals of all the control elements.
- Checking shall be done six monthly.
- Checking and maintenance of contactors
- Switch OFF the Electrical supply to the Machine.
- Remove all the power and control wires from the contactor terminals.
- Remove dust from control panel with air blower.
- Remove the contactor from the panel and visually check all the contacts for the signs of pitting and deposit of carbon on the contacts.
- Clean the contacts, terminals and all the moving parts of the contactor by spraying contactor cleaner.
- Replace the contacts if found damaged / welded.
- Put back the contactor in the panel and re-terminate all the power and control wires properly to their original locations.
- Checking of contactors shall be done six monthly.
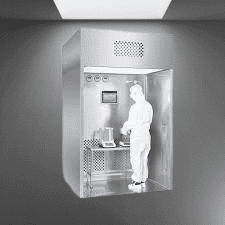
- Checking of motor
- Check the insulation resistance of motor winding with the help of megger.
- Check the phase continuity and winding continuity of motor with the help of tong tester.
- Physically check the motor terminal box and terminal connections.
- Check the voltage drawn by motor with the help of multimeter
- Check the current drawn by motor with the help of tong tester.
- Physically check the direction of rotation; it should be as per recommended direction.
- Checking shall be done after every six month.
- Checking of earth connection
- Check earthing wire and thimble for any damage. If observed any replace the same.
- Tighten the earth connection with appropriate tool.
- Check the earthing of the panel body.
- A good earthing shall show less than 2 Volts between the Neutral Wire of the Incoming Power supply and Panel Body.
- Checking shall be done six monthly.
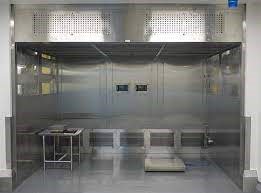
- Checking and replacement of tube light
- Check the luminous intensity with the help of lux meter.
- If the luminous intensity is low, replace the tube light.
- Switch off the power supply
- Remove the electrical connections.
- Remove the tube light from fixture; and replace with new one.
- Make the connection as before.
- Check the luminous intensity after replacement of tube light.
- Post Preventive Maintenance – Check List
- Record the PM details as per the Format No.: SOP/EN/XXXYYY “Preventive Maintenance Checklist & Record for Dispensing and Sampling Booth”.
- Whenever any modifications and major works are carried out to the equipment, the same shall be mentioned in the equipment history card as per the respective SOP.
- Connect the equipment main power supply and start the equipment.
- Ensure that the equipment is running smoothly, without any abnormality.
- If any abnormality is observed in the above, same will be attended in co-ordination with User department Head.
- ABBREVIATIONS:
- CRF No. : Change Request Form number
- QA : Quality Assurance
- SOP : Standard operating procedure
- HVAC : Heat Ventilation Air conditioning.
- QC : Quality control
- REFERENCES:
- Nil.
- DISTRIBUTION LIST:
- SOP shall be distributed to following departments Quality Assurance, Engineering as per user request.
- ANNEXURES:
- Preventive Maintenance Checklist & Record for Dispensing and Sampling Booth: SOP/EN/XXXYYY