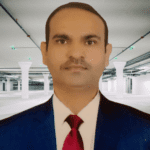
- Jag Parvesh Bhardwaj
- Manager-QA, Lead Auditor ISO- 9001 (QMS), GxP Consultant & Auditor
- linkedin.com/in/jag-parvesh-bhardwaj-7a7b1b31
The training program in pharmaceutical plants plays a pivotal role in shaping a knowledgeable and skilled workforce. It serves as the bedrock for maintaining high standards of quality, safety, and efficiency throughout the manufacturing process.
The key roles of the training program are as follows:

- Ensuring Compliance:
- Training programs are instrumental in educating employees about Good Manufacturing Practices (GMP) and regulatory requirements. By instilling a deep understanding of industry guidelines, the training ensures that all processes and operations align with legal standards, minimizing the risk of non-compliance.
- Enhancing Product Quality:
- Quality is of paramount importance in the pharmaceutical industry. Training equips employees with the necessary expertise to adhere to Standard Operating Procedures (SOPs), implement quality control measures, and identify and mitigate deviations, thus ensuring the production of safe and effective medicines.
- Promoting Safety:
- Pharmaceutical manufacturing involves handling hazardous materials and operating complex machinery. Proper safety training reduces the risk of accidents, injuries, and exposure to harmful substances, creating a secure working environment for all employees.
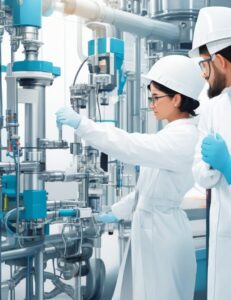
- Optimizing Efficiency:
- Well-structured training imparts knowledge on efficient manufacturing practices, equipment handling, and Lean principles. This streamlines processes, reduces waste, and enhances productivity, ultimately contributing to cost-effectiveness and operational excellence.
- Adapting to Technological Advancements:
- The pharmaceutical industry continually evolves with technological advancements. Training programs keep the workforce updated with the latest technologies, ensuring seamless integration and optimal utilization of sophisticated equipment.
- Encouraging Innovation:
- Training fosters a culture of continuous learning, empowering employees to explore innovative approaches and problem-solving techniques. This cultivates a workforce capable of adapting to changing circumstances and driving process improvements.
- Developing Specialized Skills:
- Different roles in pharmaceutical manufacturing demand specific skill sets. Targeted training programs enable employees to acquire specialized skills, such as analytical techniques, quality assurance, or cleanroom practices, enhancing their expertise in their respective fields.
Different types of Training Programs in Pharma Manufacturing Plants
Training Type | Description |
---|---|
GMP Training | Focuses on Good Manufacturing Practices (GMP) to ensure products are consistently produced and controlled to meet quality standards. |
Safety Training | Educates employees about potential hazards in the workplace and provides guidelines to maintain a safe and accident-free work environment. |
SOPs (Standard Operating Procedures) Training | Teaches employees the prescribed steps and protocols for various manufacturing processes to ensure uniformity and minimize errors. |
Quality Control Training | Instructs personnel on how to perform quality control tests and inspections to maintain the high quality of pharmaceutical products. |
Equipment Handling Training | Instruct personnel on how to perform quality control tests and inspections to maintain the high quality of pharmaceutical products. |
Cleanroom Practices Training | Covers practices and protocols to maintain cleanroom environments, ensuring minimal contamination and adherence to industry standards. |
Regulatory Compliance Training | Educates employees about relevant regulations and guidelines to ensure the manufacturing process complies with legal requirements. |
Lean Manufacturing Training | Introduces Lean principles to streamline processes, reduce waste, and enhance efficiency in pharmaceutical manufacturing operations. |
Data Integrity and Security Training | Focuses on data accuracy, confidentiality, and cybersecurity measures to safeguard critical information in pharmaceutical processes. |
Leadership and Team Management Training | Equips supervisors and managers with skills to effectively lead teams and manage operations in a pharmaceutical manufacturing setting. |
Continuous Improvement Training | Encourages a culture of continuous learning and improvement, fostering innovation and adaptability within the manufacturing workforce. |
Environmental Sustainability Training | Raises awareness about sustainable practices and environmentally friendly approaches in pharmaceutical manufacturing processes. |
Steps to Enhance the Quality of the Training Program:
- Training Needs Assessment: Conduct a thorough analysis of the organization’s training needs by identifying skill gaps and performance deficiencies. This will help tailor the training program to address specific requirements.
- Engage Subject Matter Experts (SMEs): Collaborate with experienced professionals and SMEs from different departments to design and deliver training content. Their expertise ensures relevance and accuracy.
- Interactive Training Methods: Utilize diverse and interactive training methods, such as hands-on workshops, simulations, case studies, and group discussions, to keep employees engaged and promote active learning.
- Regular Training Reviews: Periodically review training materials and update them to align with the latest regulations, industry practices, and advancements in technology.
- Feedback Mechanism: Implement a robust feedback mechanism to gather input from trainees. This allows for continuous improvement of the training program based on the learners’ needs and preferences.
- Performance Evaluation: Conduct post-training assessments to evaluate the effectiveness of the training program. Use the results to identify areas that require further reinforcement or improvement.
- Continuous Learning Culture: Foster a culture of continuous learning and skill development by encouraging employees to seek additional training opportunities and certifications.
- Incorporate Soft Skills Training: In addition to technical skills, include soft skills training, such as communication, teamwork, and problem-solving, to enhance overall employee effectiveness.
- Supervisor Involvement: Involve supervisors and managers in the training process to reinforce the importance of training and provide ongoing support and guidance to employees.
- Reward and Recognition: Recognize and reward employees who demonstrate exceptional performance and apply their training knowledge effectively. This encourages others to take training seriously.
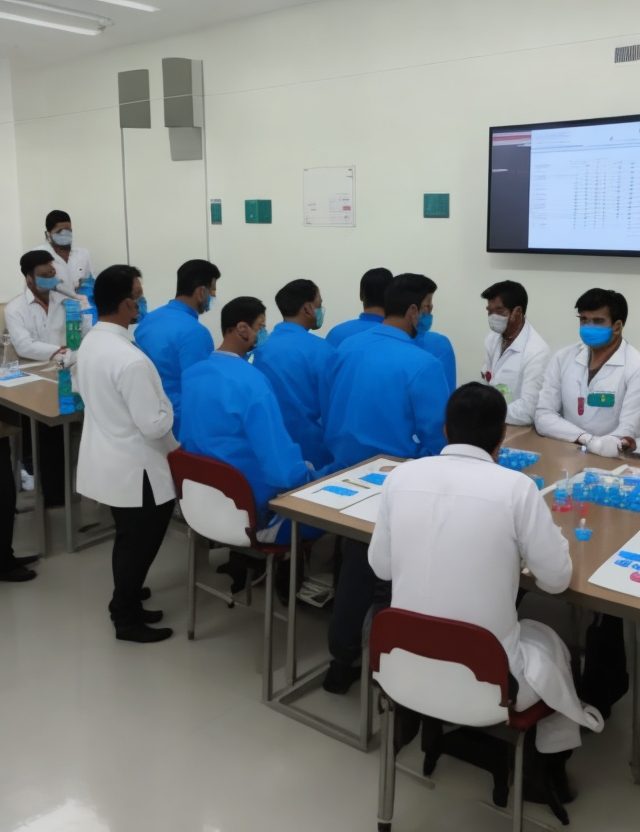
Advantages of the Good Training Program
Advantages | Description |
---|---|
GMP Compliance | Ensures adherence to Good Manufacturing Practices, leading to consistent quality products and regulatory compliance. |
Enhanced Safety | Promotes a safe working environment by educating employees on handling hazardous substances and emergency protocols. |
Consistency in Processes | Standard Operating Procedures (SOPs) training leads to uniformity in manufacturing processes and reduces errors. |
Optimal Equipment Usage | Proper equipment handling and maintenance ensure peak performance, minimizing downtime and production disruptions. |
High-Quality Products | Quality control training helps identify and prevent defects, ensuring the production of safe and effective medicines. |
Cleanroom Efficiency | Training in cleanroom practices maintains cleanliness and minimizes contamination risks during pharmaceutical production. |
Traceability and Compliance | Emphasizes meticulous documentation, aiding traceability for audits and ensuring adherence to regulatory requirements. |
Adapting Lean Principles | Introducing Lean Manufacturing principles improves efficiency, reduces waste, and boosts overall productivity. |
Fostering Teamwork | Encourages teamwork and effective communication, promoting synergy among different departments and better collaboration. |
Environmental Sustainability | Raises awareness about sustainable practices and responsible waste management, aligning the industry with eco-friendly goals. |
Handling Contingencies | Equips employees with problem-solving skills to address unexpected situations and deviations during manufacturing. |
Audit Readiness | Cultivates a culture of compliance and preparedness for internal and external audits, ensuring a smooth auditing process. |
Data Integrity and Security | Focuses on data accuracy, confidentiality, and cybersecurity measures to safeguard critical information. |
Essentials of Pharmaceutical Technology
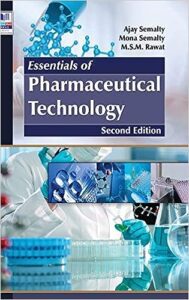