The vacuum pump is a mechanical device that is designed to create and maintain a region of low pressure, commonly known as a vacuum, within a specific area or system. It removes or extracts air and other gases from the desired space, leaving behind a reduced-pressure environment. Vacuum pumps play a crucial role in various industries and scientific fields where air or other gases can hinder specific processes or experiments. By creating a vacuum, these pumps enable the manipulation of gases, facilitate the production of high-quality materials, and allow for precise control over chemical reactions
Vacuum pump working principle
Vacuum pumps, those enigmatic devices that hold sway in the realms of industry and science, derive their power from a profound working principle. In this intriguing exploration, we embark on a journey to demystify their inner workings and shed light on their indispensable role. Prepare to be immersed in a world of complexity and fascination as we delve into the intricacies of the vacuum pump working principle.
At its core, the working principle of a vacuum pump revolves around the creation and maintenance of a region characterized by low pressure, aptly known as a vacuum. The intricate dance of forces and mechanisms employed by these devices is nothing short of mesmerizing.
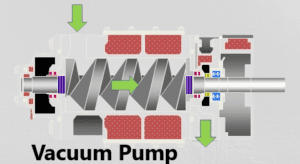
One of the fundamental concepts underlying vacuum pump operation is positive displacement. Through this mechanism, a cavity is expanded and contracted, creating a pressure differential that propels the movement of gases. This ingenious approach enables the evacuation of air and other gases from a confined space, leaving behind a vacuum.
Another captivating working principle employed by vacuum pumps is known as momentum transfer. By utilizing the momentum of a fluid or gas, these devices generate a force that drives the evacuation process. This fascinating phenomenon relies on the transfer of kinetic energy from the moving gas particles to the surrounding fluid, effectively creating a pressure gradient that leads to the establishment of a vacuum.
Moving into the realm of modern vacuum pump technology, we encounter the concept of entrapment. Employing the properties of sorbent materials, these pumps capture and retain gas molecules, gradually reducing the pressure within the system. This intricate process involves the adsorption of gas molecules onto the surfaces of solid materials, effectively trapping them and allowing for the creation of a vacuum.
Molecular drag, yet another captivating working principle, relies on the interaction between gas molecules and a rapidly moving fluid stream. As the fluid accelerates, it carries along gas molecules, dragging them toward the pump outlet and away from the vacuumed space. This elegant mechanism showcases the interplay between fluid dynamics and molecular forces, paving the way for efficient vacuum creation.
Components of the vacuum pump
Component | Description |
---|---|
Inlet | The entry point through which gases enter the vacuum pump |
Outlet | The exit point through which gases are expelled from the pump |
Pumping Chamber | The main area where the gas is compressed or evacuated |
Rotor | The rotating element that creates the pumping action |
Stator | The stationary element that interacts with the rotor |
Vanes | Sliding blades that create chambers and assist in pumping |
Diaphragm | A flexible membrane that oscillates to create pressure changes |
Scroll | Interlocking spiral elements that compress and move gases |
Bearings | Support mechanisms that allow the rotor to rotate smoothly |
Seals | Prevents leakage of gas and maintains the vacuum |
Drive Mechanism | The power source that enables the rotation of the rotor |
Control Valve | Regulates the gas flow and pressure within the pump |
Oil Reservoir | Stores lubricating oil for certain types of pumps |
Critical formulas & oil grade of the vacuum pump
When it comes to vacuum pumps, there are certain critical formulas and considerations related to their performance and the selection of appropriate oil grades. Here are a few important aspects to understand:
Pumping Speed (S):
- The pumping speed of a vacuum pump refers to the volume of gas it can remove from a system per unit of time, typically measured in liters per second (L/s) or cubic meters per hour (m³/h).
Pumping Speed Formula:
- The pumping speed (S) of a vacuum pump can be calculated using the following formula: S = Q / (p · V) Where: S = Pumping speed (L/s or m³/h) Q = Gas flow rate (m³/s or L/h) p = Pressure (Pa or Torr) V = Volume (m³ or L)
Oil Grade Selection:
- The selection of vacuum pump oil grade depends on the specific type and design of the pump. Different pumps have different oil requirements, such as viscosity, additives, and temperature characteristics. It is crucial to refer to the manufacturer’s guidelines or technical specifications to determine the recommended oil grade for a particular vacuum pump model.
Viscosity:
- Viscosity refers to the thickness or resistance to the flow of the vacuum pump oil. It is typically measured in units of centistokes (cSt). The viscosity grade recommended by the pump manufacturer ensures optimal lubrication and performance in different operating conditions.
Additives and Properties:
- Vacuum pump oils may contain additives to enhance their lubricating properties, oxidation resistance, and thermal stability. These additives help prevent oil breakdown, foaming, and corrosion within the pump, ensuring its longevity and efficient operation
Types of Vacuum Pumps
vacuum technology, a myriad of pump types exist, each with its own distinctive features and applications. As we embark on this enlightening journey, we delve into the fascinating world of vacuum pumps, exploring their diverse forms and unraveling the secrets behind their functionality. Prepare to be captivated by the wide range of vacuum pump types that shape industries and scientific endeavors.
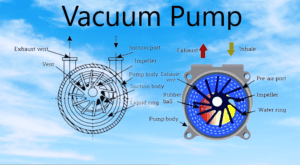
- Rotary Vane Pump:
- One of the most common and versatile vacuum pumps, the rotary vane pump operates through the use of rotating vanes within a cylindrical chamber. These vanes create chambers of varying volume, allowing for the intake and compression of gases. With their robustness and ability to achieve moderate vacuum levels, rotary vane pumps find applications in industries ranging from laboratories to HVAC systems.
- Diaphragm Pump:
- Known for their oil-free operation, diaphragm pumps utilize a flexible diaphragm that oscillates to create pressure differentials. This mechanism enables the transfer of gases and the establishment of a vacuum. Diaphragm pumps are valued for their ability to handle corrosive gases and find applications in analytical instruments, medical devices, and laboratories where contamination must be minimized.
- Scroll Pump:
- A relatively newer addition to the vacuum pump family, the scroll pump operates on the principle of two intermeshing scrolls. As the scrolls rotate, gas is trapped and progressively compressed, leading to the creation of a vacuum. These pumps offer oil-free operation, low vibration, and reduced noise levels, making them ideal for applications in semiconductor manufacturing, vacuum furnaces, and research facilities.
- Turbo Pump:
- Harnessing the power of high-speed rotation, turbo pumps rely on a combination of centrifugal and molecular drag forces to achieve high vacuum levels. These pumps typically consist of a series of stages, each comprising a rotor and stator. Turbo pumps find their niche in high-vacuum applications such as mass spectrometry, electron microscopy, and semiconductor fabrication.
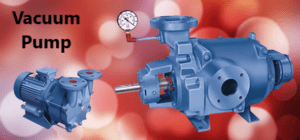
- Diffusion Pump:
- Ideal for achieving ultra-high vacuum levels, diffusion pumps employ the principle of vapor jet diffusion. In this process, vapor molecules collide with gas molecules, transferring momentum and propelling the gas molecules toward the pump outlet. Diffusion pumps are commonly utilized in applications such as vacuum metallurgy, space simulation chambers, and particle accelerators.
- Ion Pump:
- Operating on the principle of ionization, ion pumps create a vacuum by extracting gas molecules through the use of high-energy ions. These pumps find their utility in high-vacuum systems where extreme cleanliness and reliability are paramount, such as in particle physics experiments and ultra-high vacuum chambers.
- Cryogenic Pump:
- By employing extreme cold temperatures, cryogenic pumps freeze and capture gases, effectively creating a vacuum environment. These pumps utilize cryogenic fluids or solid-state refrigeration to achieve low temperatures. Cryogenic pumps are particularly valuable in applications where rapid pumping speed and the removal of condensable gases are critical, such as in vacuum coating and space simulation chambers.
Uses of vacuum pump in Pharmaceuticals
Uses | Description |
---|---|
Vacuum Drying | Removes moisture from pharmaceutical products or equipment |
Freeze Drying | Facilitates the lyophilization process for drug preservation |
Distillation | Separates and purifies components in pharmaceutical solutions |
Filtration | Assists in filtering and clarifying pharmaceutical liquids |
Tablet and Capsule Packaging | Enables vacuum sealing to maintain product integrity |
Vacuum Mixing | Homogenizes pharmaceutical ingredients efficiently |
Vacuum Coating | Deposits thin films or coatings on pharmaceutical surfaces |
Sterilization | Supports vacuum-based sterilization processes |
Degassing | Removes gases from pharmaceutical formulations |
Formulation and Compounding | Facilitates the preparation of pharmaceutical compounds |
Applications of vacuum pump
Industry | Applications |
---|---|
Manufacturing | – Vacuum distillation |
– Composite molding | |
– Vacuum packaging | |
– Vacuum impregnation | |
– Vacuum casting | |
– Vacuum drying | |
– Vacuum filtration | |
– Vacuum sealing | |
Scientific Research | – Mass spectrometry |
– Electron microscopy | |
– Surface science experiments | |
– Analytical instrumentation | |
– Particle physics experiments | |
– Vacuum experiments | |
– Vacuum chambers and systems | |
Healthcare | – Medical imaging (MRI, CT) |
– Blood collection and processing | |
– Negative pressure wound therapy | |
– Surgical procedures (e.g., laparoscopy, endoscopy) | |
– Laboratory equipment (e.g., vacuum ovens, freeze dryers) | |
– Vacuum-assisted delivery in obstetrics | |
– Dental procedures (e.g., suction systems) | |
HVAC Systems | – Air conditioning and refrigeration |
– Vacuum pumps for HVAC maintenance and repair | |
Power Generation | – Steam condenser evacuation |
– Turbine sealing | |
– Vacuum insulation | |
– Gas handling in nuclear power plants | |
Semiconductor Manufacturing | – Thin film deposition |
– Ion implantation | |
– Etching and cleaning processes | |
– Wafer handling and transportation | |
Food Processing | – Freeze drying |
– Vacuum packaging | |
– Vacuum sealing | |
– Deaeration and degassing of food products | |
– Flavor and fragrance extraction | |
Environmental Applications | – Waste management (e.g., landfill gas collection) |
– Water treatment (e.g., vacuum filtration, degasification) | |
– Pollution control (e.g., air scrubbers, vacuum systems) | |
– Vacuum evaporation for wastewater treatment |
Vacuum pump manufacturers
vacuum pump manufacturers in India and worldwide:
India:
- PPI Pumps Pvt. Ltd.
- Everest Blowers Pvt. Ltd.
- Dolphin Vacuum Systems
- Alpha Vacuum Technology
- Garuda Pumps
- Airtech Vacuum Process Solutions
- Precise Vacuum Systems Pvt. Ltd.
- Promivac Engineers
- Turbo Blower Manufacturer
- Trivac Vacuum Pumps by Leybold India
Worldwide:
- Leybold GmbH (Germany)
- Edwards Vacuum (United Kingdom)
- Busch Vacuum Solutions (Germany)
- Pfeiffer Vacuum Technology AG (Germany)
- Gardner Denver Holdings Inc. (United States)
- Atlas Copco AB (Sweden)
- Becker Vacuum Pumps and Systems (Germany)
- KNF Neuberger GmbH (Germany)
- Oerlikon Leybold Vacuum (Switzerland)
- Tuthill Vacuum & Blower Systems (United States)
Frequently Asked Questions:
What is the working principle of a rotary vane vacuum pump?
Answer: The rotary vane vacuum pump operates by using rotating vanes to create varying chambers, allowing the intake and compression of gases through positive displacement.
What are the advantages of a diaphragm vacuum pump?
Answer: Diaphragm vacuum pumps offer oil-free operation, making them suitable for applications where contamination must be minimized. They are also known for their ability to handle corrosive gases and provide reliable performance.
How does a scroll vacuum pump work?
Answer: A scroll vacuum pump operates using interlocking spiral scrolls that create chambers, compressing and moving gases to achieve vacuum levels. They are characterized by oil-free operation, low vibration, and reduced noise levels.
What is the purpose of a backing pump in a turbo molecular vacuum pump system?
Answer: The backing pump is responsible for evacuating the larger volumes of gas from the system, enabling the turbo molecular pump to operate efficiently at high vacuum levels.
How does a diffusion pump achieve high vacuum levels?
Answer: Diffusion pumps achieve high vacuum levels by utilizing vapor jet diffusion. Vapor molecules collide with gas molecules, transferring momentum and propelling the gas molecules towards the pump outlet, effectively creating a vacuum.
What is the role of an ion pump in a vacuum system?
Answer: Ion pumps operate by using high-energy ions to extract gas molecules from a vacuum system. They are utilized in high-vacuum applications where extreme cleanliness and reliability are crucial.
How does cryogenic cooling assist in the operation of a cryogenic vacuum pump?
Answer: Cryogenic cooling lowers the temperature within the pump, causing gases to condense and freeze. This freeze-out process allows the cryogenic pump to capture and remove gases, creating a vacuum environment.
What are the benefits of using a dry vacuum pump over oil-sealed pumps?
Answer: Dry vacuum pumps eliminate the need for oil lubrication, resulting in reduced maintenance, cleaner operations, and no risk of oil contamination. They are particularly advantageous in applications where oil-free environments are required.
What is the significance of ultimate vacuum in vacuum pump specifications?
Answer: The ultimate vacuum refers to the lowest pressure that a vacuum pump can achieve. It is an important specification as it determines the pump’s suitability for specific applications that require specific vacuum levels.
How does a vacuum gauge assist in monitoring and controlling vacuum levels in a system?
Answer: A vacuum gauge measures and displays the pressure within a vacuum system, allowing operators to monitor and control the vacuum levels. It helps ensure the system operates within the desired pressure range and enables troubleshooting if pressure deviations occur.