Compressed air dryers serve as vital components in industrial systems, ensuring the purity and reliability of compressed air. Understanding their working principle unveils the mechanisms behind effective moisture control. In this article, we delve into the intricacies of compressed air dryers, shedding light on their fundamental operation and the importance of moisture management.
Working Principle of the Air Dryer
Compressed air dryers stand as essential guardians against moisture-related issues in industrial applications. By comprehending their working principle, we uncover the methods employed to extract moisture from compressed air effectively. Mechanical refrigeration, condensation, cooling, and desiccant adsorption all play integral roles in moisture management
Moisture Management: The primary objective of a compressed air dryer is to remove moisture from the compressed air, safeguarding equipment and processes from potential damage or malfunction. Moisture intrusion can lead to corrosion, impaired performance, and compromised product quality. By comprehending the working principle of compressed air dryers, we unlock the means to conquer this moisture menace.
Mechanical Refrigeration: One common type of compressed air dryer utilizes mechanical refrigeration. It follows a refrigeration cycle akin to household refrigerators. The process begins as warm and moisture-laden air enters the dryer. The air encounters a refrigeration system comprising a compressor, condenser, expansion valve, and evaporator. The compressor pressurizes the air, elevating its temperature.
Cooling and Condensation: Within the condenser, the hot, pressurized air encounters a cooling mechanism that lowers its temperature. As the air cools, moisture vapor begins to condense, transforming into liquid water. This condensed water is then drained away, eliminating it from the compressed air stream.
Further Cooling and Drying: After the condensation stage, the air passes through an expansion valve, causing a rapid decrease in pressure. This pressure drop leads to further cooling, lowering the air’s dew point. The dew point represents the temperature at which the air becomes saturated with moisture. By reaching and surpassing this dew point, the compressed air dryer effectively dries the air, minimizing the risk of subsequent condensation downstream.
Moisture Capture: To ensure optimal drying, some compressed air dryers incorporate desiccant materials. These desiccants possess a remarkable affinity for moisture. As the air flows through the dryer, the desiccant adsorbs any remaining moisture molecules, extracting them from the air stream. This additional step reinforces moisture removal, enhancing the dryer’s effectiveness.
Regeneration: Over time, desiccants become saturated with moisture and require regeneration to maintain their drying capabilities. Depending on the dryer’s design, this regeneration may involve the application of heat or a separate air stream. The process liberates the captured moisture from the desiccant, restoring its moisture-adsorbing capacity for subsequent air treatment cycles.
Types of Air Dryers
Air dryers are essential components of industrial air compressor systems, responsible for removing moisture from compressed air to maintain its quality and prevent damage to downstream equipment. Several types of air dryers are employed in various industrial applications. In this article, we explore the common types of air dryers used in conjunction with industrial air compressors.
- Refrigerated Air Dryers:
- Refrigerated air dryers are widely used in industrial settings due to their efficiency and cost-effectiveness. These dryers employ a refrigeration system, similar to household refrigerators, to cool the compressed air. The cooling process causes moisture to condense, allowing it to be separated and drained away from the air stream. Refrigerated air dryers can achieve dew points as low as 3°C (37°F), effectively reducing moisture content in the compressed air.
- Desiccant Air Dryers:
- Desiccant air dryers utilize a desiccant material, such as silica gel or activated alumina, to absorb moisture from the compressed air. They operate on the principle of adsorption, where the desiccant attracts and retains moisture molecules. Desiccant dryers are capable of achieving extremely low dew points, often below -40°C (-40°F), making them suitable for applications requiring exceptionally dry air, such as in electronics or pharmaceutical industries. These dryers typically consist of two towers filled with desiccant material, allowing for continuous operation with one tower adsorbing moisture while the other regenerates.
- Membrane Air Dryers:
- Membrane air dryers utilize semipermeable membranes to selectively remove moisture from compressed air. These membranes have microscopic pores that allow water vapor to pass through while blocking larger air molecules. By adjusting pressure differentials, membrane dryers facilitate the removal of moisture without the need for refrigeration or desiccant materials. They are commonly used in applications where low dew points are not required, and energy efficiency is a priority.
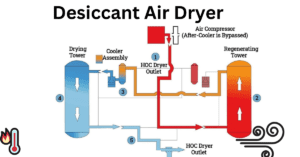
- Deliquescent Air Dryers:
- Deliquescent air dryers employ a hygroscopic substance, typically a salt-like calcium chloride or potassium hydroxide, to absorb moisture from compressed air. The hygroscopic material attracts moisture molecules, causing it to dissolve and form a liquid solution. The liquid byproduct is then drained away, leaving the compressed air dry. Deliquescent dryers are often used in remote or portable applications where electricity or complex systems are not readily available.
- Heatless Air Dryers:
- Heatless air dryers, as the name suggests, do not utilize external heat sources for the drying process. These dryers typically employ desiccant materials to adsorb moisture from the compressed air. Heatless dryers use a portion of the dry compressed air to regenerate the desiccant bed in a cyclic process. While they may have higher energy consumption compared to heated dryers, they are popular for their simplicity, reliability, and cost-effectiveness.
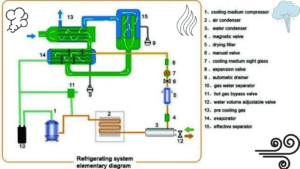
Components of the Air Dryers
Component | Description |
---|---|
Compressed Air Inlet | Point of entry for the moisture-laden compressed air |
Pre-Filters | Removes larger particles and contaminants from the incoming air |
Heat Exchangers | Transfers heat between the incoming and outgoing air streams |
Refrigeration System | Cools the compressed air using a refrigeration cycle |
Condenser | Converts moisture vapor into liquid water for separation |
Separator | Removes liquid water from the compressed air stream |
Expansion Valve | Causes a pressure drop, leading to further cooling and drying |
Desiccant Bed | Contains desiccant material (e.g., silica gel or activated alumina) for moisture adsorption |
Purge Valve | Removes moisture-laden air from the desiccant bed during regeneration |
Control System | Monitors and controls the dryer’s operation and parameters |
Moisture Drain | Facilitates the removal of collected liquid water from the dryer |
Dry Air Outlet | Point of exit for the dry and purified compressed air |
Advantages of the Air Dryer
Advantages | Description |
---|---|
Moisture Control | Effectively removes moisture from compressed air, preventing corrosion, contamination, and freezing. |
Equipment Protection | Safeguards downstream equipment from potential damage caused by moisture, ensuring longer lifespan and improved performance. |
Improved Product Quality | Helps maintain the quality and integrity of products in applications where dry air is crucial, such as in food processing or pharmaceutical industries. |
Energy Efficiency | Reduces energy consumption by optimizing the performance of downstream equipment, such as pneumatic tools and machinery. |
Enhanced Process Efficiency | Eliminates moisture-related issues that can impede process efficiency, ensuring consistent and reliable operation. |
Prevents Pipe Blockages | Minimizes the risk of pipe blockages caused by frozen condensate, leading to uninterrupted airflow and reduced maintenance. |
Extends Maintenance Intervals | Reduces the frequency of maintenance and servicing requirements for downstream equipment by preventing moisture-related issues. |
Protects Sensitive Equipment | Provides dry and clean air to sensitive instruments and devices, preventing damage and maintaining their accuracy and reliability. |
Compliance with Standards | Helps meet industry and regulatory standards that require specific moisture content in compressed air, ensuring compliance and quality assurance. |
Versatility | Air dryers are available in various types and sizes to suit different applications and air compressor systems. |
Desiccant-type Air Dryer Working Principle
The working principle of a desiccant-type air dryer revolves around the use of desiccant materials, such as silica gel or activated alumina, to remove moisture from compressed air. These dryers employ an adsorption process, where the desiccant attracts and holds moisture molecules, effectively drying the air. Here is an overview of the working principle of a desiccant-type air dryer:
- Adsorption Stage: The moist compressed air enters the dryer and passes through a bed of desiccant material. As the air flows through the desiccant bed, the moisture molecules present in the air are attracted to the surface of the desiccant particles. The desiccant acts like a sponge, adsorbing the moisture and removing it from the compressed air stream.
- Drying Cycle: During the drying cycle, the desiccant material continues to adsorb moisture until it reaches its saturation point. The length of the drying cycle depends on factors such as the moisture content of the incoming air and the capacity of the desiccant bed.
- Regeneration Stage: Once the desiccant becomes saturated with moisture, it needs to be regenerated to restore its moisture-absorbing capability. This is achieved by diverting a portion of the dry compressed air from the system to a separate regeneration chamber or tower.
- Purge Air: The diverted dry air, often referred to as purge air or regeneration air, passes through the saturated desiccant bed in the regeneration chamber. As it flows through the desiccant, the purge air releases heat and carries away the moisture that was previously adsorbed. The moisture-laden purge air is then vented outside the system.
- Cooling and Pressure Equalization: After the regeneration stage, the desiccant bed needs to cool down before it can be reintroduced into the drying cycle. To achieve this, the pressure in the regeneration chamber is equalized with the pressure in the drying chamber. This equalization helps cool the desiccant bed, preparing it for the next drying cycle.
- Switching to the Next Bed: Desiccant-type air dryers often consist of two or more beds filled with desiccant material. While one bed is in the drying cycle, the other bed is undergoing regeneration. The dryer’s control system ensures that the beds switch roles periodically, allowing for continuous drying operation without interruption.
By utilizing the adsorption capabilities of desiccant materials, desiccant-type air dryers effectively remove moisture from compressed air, ensuring the delivery of dry and moisture-free air to downstream processes and equipment. This drying process helps prevent issues associated with moisture, such as corrosion, freezing, and contamination, ensuring the reliable and efficient operation of compressed air systems.
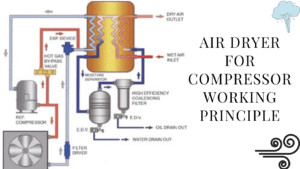
Refrigerated Air Dryer Working Principle
The working principle of a refrigerated air dryer involves the use of a refrigeration system to cool the compressed air and remove moisture from it. This type of air dryer is commonly used in industrial applications to achieve dry and moisture-free compressed air. Here is an overview of the working principle of a refrigerated air dryer:
- Compressed Air Inlet: Moisture-laden compressed air enters the refrigerated air dryer through an inlet port.
- Cooling Stage: The compressed air passes through a refrigeration system that consists of a compressor, condenser, expansion valve, and evaporator. The compressor pressurizes the incoming air, causing its temperature to rise.
- Heat Exchange: In the condenser, the hot and pressurized air encounters a heat exchange process. The heat from the compressed air is transferred to a coolant, typically a refrigerant, flowing through the condenser. This heat exchange causes the compressed air to cool down.
- Condensation: As the compressed air cools in the refrigeration system, the moisture vapor within it begins to condense. The condensation occurs when the temperature of the air reaches its dew point, resulting in the formation of liquid water.
- Separator: The condensed liquid water is separated from the cooled compressed air using a separator or moisture separator. This device efficiently removes the liquid water from the air stream and directs it to a drain for disposal.
- Cooling and Drying: After the moisture separation stage, the cooled and partially dried compressed air continues its flow into the evaporator. In the evaporator, the air undergoes further cooling as it comes into contact with the cold refrigerant. This additional cooling helps to lower the air’s dew point and remove more moisture.
- Moisture Removal: The cooled and dried compressed air exits the refrigerated air dryer through an outlet port. It is now significantly reduced in moisture content, making it suitable for various industrial applications.
By utilizing the cooling effect of a refrigeration system, refrigerated air dryers effectively lower the temperature of compressed air, causing moisture to condense and be separated. This process helps prevent issues related to moisture, such as corrosion, contamination, and damage to downstream equipment. Refrigerated air dryers are widely used due to their reliability, efficiency, and ability to provide consistent dew points, typically ranging from 3°C to 10°C (37°F to 50°F).
Hello!
Good luck 🙂