Discover unparalleled water purity with our state-of-the-art Purified Water Generation Plant. Harnessing cutting-edge technology and innovative purification methods, we redefine excellence in water quality. Elevate your industry standards and ensure the highest levels of purity with the best-in-class water generation system.
Quality parameter of Purified water as per pharmacopeias:
As per USP following specifications limits for Purified water specifications | ||
Sr. No | Description | A Clear, Colorless liquid. |
1 | pH | Between 5.0 and 7.0 |
2 | Nitrates | NMT 0.2 ppm |
3 | Heavy metals | NMT 0.1 ppm |
4 | Total Organic Carbon | NMT 500 ppb |
5 | Conductivity | NMT 1.3 µS/cm |
6 | Total aerobic microbial Counts | NMT 100 CFU/mL |
7 | Escherichia coli | Must be absent |
8 | Salmonella | Must be absent |
9 | Pseudomonas aeruginosa | Must be absent |
10 | Staphylococcus aureus | Must be absent |
Working principle of the purified water generation Plant
The working principle of a purified water generation plant involves a systematic and multi-stage process designed to eliminate impurities, contaminants, and undesirable substances, ensuring the production of high-quality purified water. The plant typically employs a combination of advanced technologies to achieve the desired level of purity. Here is a general overview of the working principle:
- Raw Water Intake:
- The process begins with the intake of raw water from a reliable source, such as municipal water, well water, or surface water.
- Pre-Treatment:
- The raw water undergoes pre-treatment to remove larger impurities, suspended solids, and any substances that could potentially interfere with the subsequent purification stages.
- Pre-treatment methods may include sand filtration, sedimentation, and chemical coagulation.
- Primary Filtration:
- The pre-treated water then enters primary filtration processes, such as multimedia filtration or activated carbon filtration, which further removes finer particles, chlorine, and organic matter.
- Reverse Osmosis (RO):
- One of the key stages in the process is reverse osmosis, where water is forced through a semi-permeable membrane to separate ions, minerals, and other impurities.
- RO is highly effective in removing dissolved salts, heavy metals, and contaminants, resulting in water with high purity.
- Deionization (DI):
- Post-RO, the water may undergo deionization, a process where ion exchange resins remove remaining ions, ensuring ultra-pure water with minimal conductivity.
- UV Treatment:
- Ultraviolet (UV) light is employed for disinfection, targeting and neutralizing microorganisms, including bacteria and viruses.
- UV treatment ensures the elimination of any remaining biological contaminants.
- Storage and Distribution:
- Purified water is stored in tanks designed to maintain its quality, and a distribution system ensures its availability for various applications within the pharmaceutical facility.
- Continuous Monitoring:
- Throughout the entire process, the water quality is continuously monitored. Parameters such as conductivity, total organic carbon (TOC), and microbial content are regularly assessed to ensure compliance with established standards.
- Validation and Documentation: The entire purified water generation system undergoes validation processes to confirm its consistent performance. Comprehensive documentation of the system’s design, installation, operation, and performance is maintained to meet regulatory requirements.
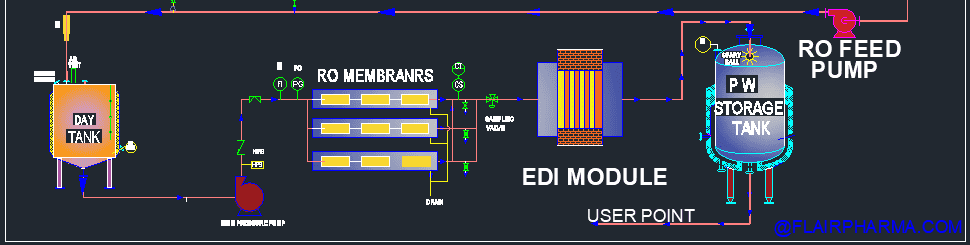
Technical details of the purified water generation system
The Purified Water Generation System (PWGS) stands as a pinnacle of technological sophistication, incorporating an array of standard features within its Distribution System to ensure the highest quality of purified water. Let’s delve into the deep technical details of these components:
Distribution Tank:
- Material: SS 316 L for contact parts, SS 304 for non-contact parts.
- Mounting: Leg mounting arrangement for stability.
- Heating Mechanism: Jacketed design or equipped with a heating coil / electrical heater for precise temperature control.
Vent Filter Assembly:
- Type: 0.2 Micron Hydrophobic vent filter assembly.
- Additional Feature: Special rupture disk (Optional) for enhanced safety measures.
Distribution Transfer Pump:
- Construction: Sanitary construction to maintain the purity of water during transfer.
- Material: SS 316 L for critical components ensuring corrosion resistance.
Ultra Violet Sterilizer:
- Purpose: Disinfection of water to eliminate microorganisms.
- Construction: SS 316 L to withstand the harsh UV treatment environment.
Piping and Fittings:
- Material: SS 316 L for piping and fittings.
- Finish: Electro-polished for improved corrosion resistance and reduced microbial adhesion.
Zero Dead Leg Valve:
- Feature: Incorporated at the end of user points (L < 3 d) to eliminate stagnant zones and ensure thorough cleaning.
Insulation:
- Purpose: Provided for the Hot / Cold water distribution to maintain temperature integrity.
Fabricated Skid:
- Material: SS 304 for the skid construction, ensuring durability and corrosion resistance.
Monitoring Systems:
- Online Conductivity Monitoring: Real-time monitoring of water conductivity to assess purity.
- Return Line Velocity/Flow Monitoring: Continuous monitoring of flow rates for optimal system performance.
- Return Line Temperature Monitoring: Real-time temperature monitoring to maintain desired conditions.
- Online TOC Monitoring: Ongoing Total Organic Carbon monitoring for comprehensive water quality control.
These technical features collectively contribute to the robustness of the Distribution System within the Purified Water Generation System, ensuring not only the delivery of ultra-pure water but also the highest standards of safety, efficiency, and quality control in pharmaceutical water production.
Latest technology in the Purified Water Generation System worldwide:
Latest technologies in the field of purified water generation. Please note that technological advancements are continuous, and there may have been further developments since then. Here are some cutting-edge technologies that were making strides in the purified water generation system:
- Continuous Electrodeionization (CEDI):
- CEDI is an advanced water purification technology that uses an electric field to remove ions from water. It is often used as a polishing step after traditional ion exchange processes, ensuring high-purity water for critical applications.
- Smart Monitoring and Control Systems:
- Integration of advanced sensors, IoT (Internet of Things), and AI (Artificial Intelligence) for real-time monitoring and control of purified water systems. These systems provide predictive maintenance, optimize performance, and enhance overall system efficiency.
- Advanced Membrane Technologies:
- Ongoing developments in membrane technologies, including improvements in reverse osmosis (RO) and nanofiltration membranes. These advancements aim to enhance water recovery rates, reduce energy consumption, and improve the overall efficiency of the purification process.
- Innovative Pre-Treatment Techniques:
- Introduction of innovative pre-treatment methods such as advanced oxidation processes (AOPs) and enhanced coagulation-flocculation strategies. These techniques help in the removal of challenging contaminants and improve the overall effectiveness of the purification process.
- High-Capacity Resin Technologies:
- Development of high-capacity ion exchange resins for deionization processes. These resins exhibit improved regeneration efficiency, increased lifespan, and enhanced ion removal capabilities.
- Energy-Efficient Systems:
- Integration of energy-efficient components and technologies to reduce the overall energy consumption of purified water generation systems. This includes the use of energy recovery devices in processes like reverse osmosis.
- Modular and Compact Designs:
- Adoption of modular and compact designs for water purification systems, allowing for easier installation, scalability, and flexibility in adapting to varying water quality and quantity requirements.
- Zero-Liquid Discharge (ZLD) Systems:
- ZLD systems are gaining prominence, especially in industries with stringent environmental regulations. These systems aim to minimize or eliminate liquid waste discharge by recovering and reusing a significant portion of the water.
- Advanced Oxidation-Reduction Potential (ORP) Control:
- Utilization of advanced ORP control systems to optimize disinfection processes. This ensures effective microbial control while minimizing the use of chemical disinfectants.
- Green Technologies:
- Increasing focus on sustainable and environmentally friendly practices, including the use of green technologies in water treatment. This involves minimizing the environmental impact of water purification processes.
It’s essential to stay updated with industry publications, conferences, and reputable sources for the latest advancements in purified water generation technology, as the field is dynamic and continually evolving.
is purified water the same as distilled water?
Feature | Purified Water | Distilled Water |
---|---|---|
Definition | Water that has undergone purification to remove impurities, contaminants, and undesirable substances. | A specific type of purified water produced through the process of distillation, which involves heating, condensation, and the removal of impurities. |
Source | Can be sourced from various starting water qualities, including tap water, well water, or spring water. | Typically sourced from tap water, but the distillation process ensures the removal of most impurities, minerals, and contaminants. |
Mineral Content | May still contain some minerals, depending on the purification method used. Mineral content can vary. | Known for extremely low mineral content. The distillation process removes minerals, resulting in water that is essentially pure H2O. |
Production Method | Various purification methods like filtration, deionization, reverse osmosis, and UV treatment may be employed. | Produced through the specific process of distillation, involving heating water to create steam, followed by condensation to remove impurities. |
Common Use Cases | Commonly used for general consumption, industrial processes, and pharmaceutical applications. | Commonly used in laboratories, medical applications, and specific industrial processes where ultra-pure water is required. |
Taste and Odor | Taste and odor may vary based on the purification method used. Some purified waters are enriched with minerals for taste. | Typically tasteless and odorless due to the absence of minerals and impurities. |
Final Purity Level | Purity level may vary based on the specific purification methods employed. | Achieves very high purity due to the distillation process, resulting in water that is close to 100% pure H2O. |
Qualification of purified water in pharmaceutical plants:
Regulatory Compliance:
- Ensure compliance with relevant regulatory requirements such as those outlined in pharmacopeias (e.g., USP, EP, JP), FDA regulations, and other applicable standards.
User Requirement Specification (URS):
- Develop a User Requirement Specification document that outlines the intended use, quality attributes, and specific requirements for the purified water system.
Design Qualification (DQ):
- Perform Design Qualification to verify that the design of the purified water system meets the specified requirements and is in accordance with regulatory guidelines.
Installation Qualification (IQ):
- Conduct Installation Qualification to ensure that the purified water system is installed correctly according to the design specifications and manufacturer’s recommendations.
Operational Qualification (OQ):
- Perform Operational Qualification to verify that the purified water system operates as intended under normal operating conditions. This involves testing and documenting system functionalities.
Performance Qualification (PQ):
- Conduct Performance Qualification to demonstrate that the purified water system consistently produces water that meets the defined quality standards. This involves testing the system under actual operating conditions.
Frequently Asked Questions:
What is purified water generation system?
Answer: A purified water generation system is a sophisticated water treatment infrastructure designed to produce water of the highest purity standards. It typically involves a series of purification methods and technologies to remove impurities, contaminants, and undesirable substances, ensuring the water is suitable for various applications, particularly in industries like pharmaceuticals where ultra-pure water is crucial.
What is the primary purpose of a Distribution Tank in a Purified Water Generation System, and what materials are commonly used in its construction?
Answer: The Distribution Tank in a Purified Water Generation System serves as a storage vessel for the purified water before it is distributed to various points of use. It helps maintain a consistent and controlled supply. Common materials used are SS 316 L for contact parts to ensure corrosion resistance and SS 304 for non-contact parts.
Explain the significance of the 0.2 Micron Hydrophobic Vent Filter assembly in the Distribution System of a Purified Water Generation System.
Answer: The 0.2 Micron Hydrophobic Vent Filter assembly is crucial for maintaining the sterility of the distribution system. It prevents the entry of airborne contaminants while allowing air to escape, ensuring that the purified water remains free from microbial contamination during storage and distribution.
What is the role of Ultra Violet (UV) Sterilizer in a Purified Water Generation System, and why is SS 316 L chosen as the construction material for this component?
Answer: The Ultra Violet (UV) Sterilizer in a Purified Water Generation System is designed to disinfect water by deactivating microorganisms. SS 316 L is chosen for its corrosion resistance, durability, and ability to withstand the harsh UV treatment environment, ensuring longevity and efficiency in microbial disinfection.
How does the Online TOC (Total Organic Carbon) Monitoring contribute to the quality control of purified water, and what is its significance in pharmaceutical water production?
Answer: Online TOC Monitoring continuously measures the concentration of organic carbon in purified water, providing real-time data on water quality. In pharmaceutical water production, it is crucial as an elevated TOC level could indicate the presence of organic impurities that might compromise the water’s purity, making it an essential tool for quality assurance and compliance.
Explain the purpose and construction material considerations for the Zero Dead Leg Valve at the end of user points in a Purified Water Generation System.
Answer: The Zero Dead Leg Valve is strategically placed to eliminate stagnant zones, ensuring thorough cleaning and preventing microbial growth. SS 316 L is commonly chosen as the construction material due to its corrosion resistance and compatibility with the stringent purity requirements of pharmaceutical water systems.
How does the Distribution Transfer Pump contribute to maintaining the sanitary conditions of purified water during transfer, and why is SS 316 L preferred in its construction?
Answer: The Distribution Transfer Pump is designed with sanitary construction to prevent contamination during water transfer. SS 316 L is preferred for its corrosion resistance, non-reactivity, and suitability for maintaining the high purity standards required in pharmaceutical water systems.
How is purified water generated?
Answer: Purified water is generated through a multi-stage purification process. This process often includes pre-treatment steps like filtration to remove larger impurities, followed by advanced methods such as reverse osmosis, deionization, and ultraviolet (UV) sterilization to eliminate dissolved salts, ions, and microorganisms, achieving a high level of purity.
What is the working principle of purified water system?
Answer: The working principle involves systematically removing impurities through a combination of physical, chemical, and biological processes. Raw water undergoes pre-treatment, primary filtration, advanced purification, and disinfection to ensure its purity. Continuous monitoring is integral to maintaining water quality within specified standards.
What is purified water example?
Answer: Purified water examples include water produced through processes like distillation, reverse osmosis, and deionization. It is often used in pharmaceuticals, laboratories, and industries where high water purity is essential.
Why is it called purified water?
Answer: It is called purified water because it undergoes a purification process that removes impurities and contaminants, resulting in water that meets specific purity standards.
What is the pH of purified water?
Answer: The pH of purified water is typically close to 7, which is considered neutral. However, variations may occur depending on the purification process and storage conditions.
What is the pH of pure water?
Answer: The pH of pure water at 25°C is 7, indicating a neutral state.
Who first purified water?
Answer:The historical record does not pinpoint a specific individual who first purified water, as water purification methods have evolved over centuries. Ancient civilizations used various methods such as boiling and sand filtration for purification.
What are the 7 stages of purification of water?
Answer: The seven stages of water purification commonly include pre-treatment, coagulation, flocculation, sedimentation, filtration, disinfection, and sometimes post-treatment for pH adjustment.
Is purified water bacteria-free?
Answer: Purified water is designed to be free from harmful microorganisms, including bacteria, through processes like filtration and disinfection.
What are the methods of water purification?
Answer: Methods include distillation, reverse osmosis, filtration (sand, carbon, membrane), chlorination, UV irradiation, and chemical treatments like coagulation and flocculation.
How much TDS is in drinking water?
Answer: The Total Dissolved Solids (TDS) in drinking water can vary, but generally, acceptable levels are below 500 mg/L. Lower TDS is often preferred for purer water.
What is pH full form?
Answer: pH stands for “power of hydrogen,” representing the concentration of hydrogen ions in a solution.
What is TDS in distilled water?
Answer: Distilled water has very low (Near 0) Total Dissolved Solids (TDS) since the distillation process removes most minerals and impurities.
Can water be 100% purified?
Answer: Achieving 100% purity in water is challenging. Processes like distillation and reverse osmosis can get close, but absolute purity is rarely achieved due to the constant exchange of ions in water.
Can you drink 100% purified water?
Answer: While drinking water with high purity is generally safe, consuming water with absolutely 100% purity may not be ideal as it lacks essential minerals and may taste flat.
What are the disadvantages of purified water?
Answer: Disadvantages may include the removal of beneficial minerals, potential flat taste, and the environmental impact of the purification process.
Is pure water tasteless?
Answer: Pure water, lacking minerals and impurities, can sometimes be perceived as tasteless or flat.
Which water is best to drink?
Answer: Water from a reliable, clean source meeting safety standards is best to drink. Preferences may vary, but many consider purified water or natural spring water.
What is the highest purified water?
Answer: Water produced through distillation or reverse osmosis is among the highest purified, but absolute purity is challenging to achieve.
How many ppm is purified water?
Answer: Purified water typically has a low Total Dissolved Solids (TDS) content, often below 10 ppm.
Is rain purified water?
Answer: Rainwater is considered relatively pure as it originates from condensation. However, it can pick up contaminants in the atmosphere during its descent.
Which water is most expensive?
Answer: Some high-end bottled waters, such as Acqua di Cristallo Tributo a Modigliani, have been known to be among the most expensive.
What is the flow range of an EDI module?
Answer: The EDI module is designed for a flow range from 10 liters per hour to 8 cubic meters per hour, with each module having specific engineering design flows depending on whether it’s for 1-pass or 2-pass reverse osmosis (RO).
What is the minimum feed flow required for the EDI module?
Answer: The minimum feed flow should be approximately half of the rated EDI product design flow.
What could be causing a decrease in flow through my EDI?
Answer: Possible causes include issues like power applied without flow, chlorine degradation of resin beads, carbon breakthrough, failure of MBS dosage, and various other factors listed in the troubleshooting guide.
Electrode Flow Issues:
What might cause a decrease in electrode flow?
Answer: Reduced electrode flow could be due to factors like blockages in the flow port, scaling of electrodes due to high water hardness, or even melted plastic if power supply is applied without proper flow.
Increasing Recovery:
How can I increase the EDI system recovery?
Answer: By diverting concentrate waste to a break tank and then pumping it back to the RO inlet, it’s possible to raise the EDI system recovery from 90% to 99%.
Pressure and Temperature Concerns:
What might cause an increase in EDI feed pressure?
Answer: Oxidation can lead to resin degradation, resulting in increased pressure.
Is low temperature problematic for EDI?
Answer: Low temperatures can increase water viscosity and slow down ion movement, affecting performance. Adjusting voltage may help mitigate this.
Quality Control:
What feed quality is necessary for EDI?
Answer: High-quality RO permeate is essential, with factors like conductivity, CO2, and silica levels affecting EDI loading and performance.
How does TOC in the feed affect quality?
Answer: TOC can lead to low quality by adsorbing onto resins and membranes, necessitating surfactant cleaning for diagnosis.
Cleaning and Sanitizing:
When should I perform low pH (acid) cleaning?
Answer: Acid cleaning is recommended for CaCO3 scaling, while Minncare cleaning is effective for bacterial biofilm.
CO2 Management:
How can I reduce CO2 in the EDI feed?
Answer: Membrane degasification or pH adjustment with NaOH can help reduce CO2 levels.
Current and Voltage:
What factors affect current and voltage in an EDI system?
Answer: Current is influenced by factors like resin fouling, scaling, or high concentrate flow, while voltage control is crucial for optimal performance.
Leaking and Installation:
How can I address leaks in my EDI system?
Answer: Check for proper torqueing and installation procedures outlined in the OEM manual to prevent leaks.
Are there any special considerations for EDI installation?
Answer: Avoid using pipe sealants on EDI threaded ports to prevent cracking and ensure proper ventilation for electrode streams.
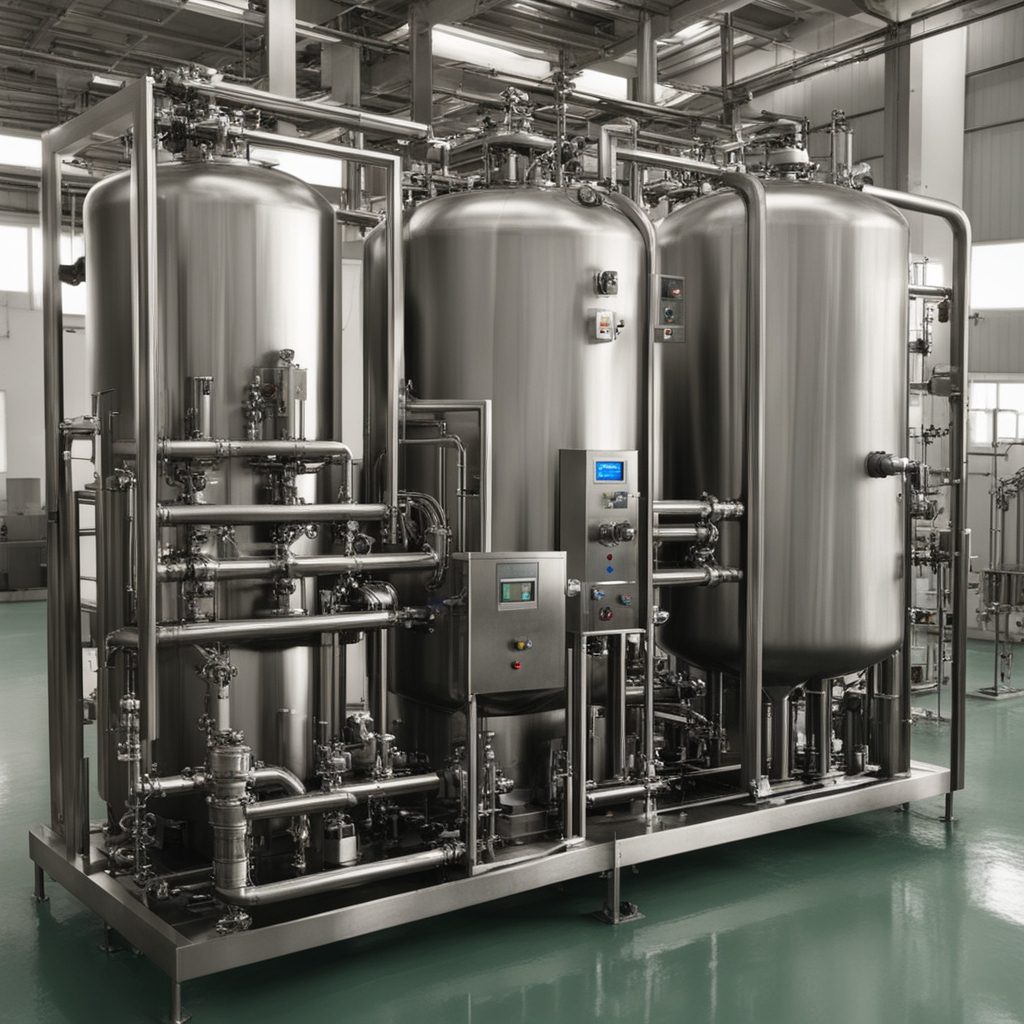
2 thoughts on “Best Purified Water Generation Plant 24”