(BFS) Blow fill seal technology is a highly efficient manufacturing process used for the aseptic packaging of pharmaceuticals and healthcare products. It involves blowing a plastic tube, filling it with the product, and sealing it to create hermetically sealed containers. BFS provides sterility, product protection, and extended shelf life, making it popular in the pharmaceutical industry.
Blow-fill-seal (BFS) technology is a manufacturing process used for the aseptic packaging of pharmaceuticals, healthcare products, and food and beverage items. It involves three main steps:
- Blow: A plastic tube is extruded and cut into individual units. One end of each unit is sealed while the other end remains open.
- Fill: The open end of each unit is positioned under a filling station, where the product (liquid or powder) is injected into the container.
- Seal: The open end of the container is sealed, forming a hermetically sealed package.
BFS technology offers advantages such as sterility, product protection, extended shelf life, and high production efficiency. It is widely used in the pharmaceutical industry for single-dose containers, such as vials, ampoules, and eye drops.
bfs full form
The full form of BFS is “Blow-fill-seal.”
Principle of Blow Fill Seal Machine (BFS) / Blow fill Seal technology
The working principle of a Blow-fill-seal (BFS) machine involves a continuous and automated process that integrates several steps. Here is a simplified explanation of the working principle:
- Mold Preparation: The machine starts by preparing the mold, which consists of two halves. The molds are precisely designed according to the desired container shape and size.
- Plastic Extrusion: A plastic material, usually in the form of a tube or a strip, is fed into the machine. The plastic material is typically a thermoplastic polymer that can be melted and molded.
- Heating and Molding: The machine heats the plastic material, making it malleable. The heated plastic is then placed between the two halves of the mold. The mold closes, and compressed air is blown into the mold, causing the plastic to expand and take the shape of the mold. This creates a container with one end open.
- Filling: The open end of the container is positioned under the filling station. The desired product, such as a liquid or powder, is injected into the container through a filling nozzle. The filling process is typically performed in a controlled and sterile environment to ensure product safety.
- Sealing: After the container is filled, the open end is sealed to create a hermetically sealed package. The sealing process may involve various techniques such as heat sealing, ultrasonic sealing, or applying a pre-formed cap or closure. The sealing ensures product integrity and prevents contamination.
- Discharge and Further Processing: The sealed containers are then discharged from the machine, ready for further processing, labeling, and packaging. The machine operates continuously, producing a high volume of aseptic packages efficiently.
Overall, the BFS machine combines plastic extrusion, molding, filling, and sealing processes in a seamless and automated manner. This technology offers advantages such as sterility, product protection, extended shelf life, and high production efficiency, making it widely used in the pharmaceutical and healthcare industries.
Blow fill seal machine
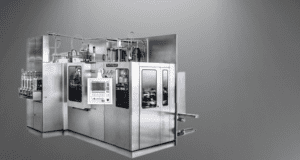
A Blow-fill-seal (BFS) machine is a packaging technology used to produce aseptic and hermetically sealed containers. It combines the processes of molding, filling, and sealing into a continuous and automated system. The machine starts by extruding plastic material into a hollow tube, which is then molded into the desired container shape using a mold system. The mold is then opened, and the container is transferred to the filling station. The product is precisely dosed and injected into the container, followed by sealing the container with a hermetic seal. BFS machines are widely used in the pharmaceutical industry for packaging liquid medications, inhalation products, and ophthalmic solutions, among others. They provide a sterile packaging solution, ensuring product integrity, extended shelf life, and enhanced safety.
Technical details of Blow fill seal (BFS) machine.
Aspect | Range | Critical Points |
---|---|---|
Temperature | 150-250°C (302-482°F) | Controlled heating of plastic material. |
Pressure | 4-10 bar | Compressed air for blowing and sealing. |
Filling Pressure | 0.2-4 bar | Controlled filling of the product into containers. |
Electrical Power | 10-30 kW | Power consumption of the BFS machine. |
Speed | 100-600 units/min | Production rate of containers per minute. |
Container Sizes | Varies | Depends on the mold and machine specifications. |
Sterility | Aseptic | Maintaining sterile conditions during the process. |
The Main components of the Blow fill seal machine (BFS)
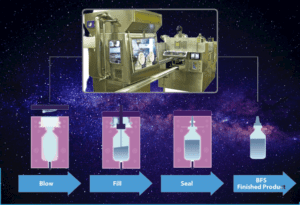
Component | Function |
---|---|
Extruder | Melts and extrudes the plastic material used for container forming |
Mold System | Forms the shape of the container |
Heating System | Heats the plastic material for molding |
Blowing System | Supplies compressed air for blowing the plastic material into the mold |
Filling System | Injects the product into the formed containers |
Sealing System | Seals the containers to create a hermetic seal |
Control System | Manages and controls the machine operations and parameters |
Conveyor System | Transports the containers through different stages |
Cooling System | Cools down the containers after molding |
Sterilization System | Provides a sterile environment during the process |
Discharge System | Releases the finished containers from the machine |
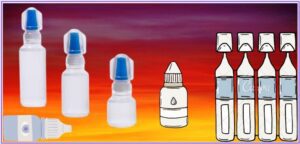
Applications of the Blow-fill-seal (BFS) machine
The Blow-fill-seal (BFS) machine is extensively used in the pharmaceutical industry for the aseptic packaging of various products. Some of the common applications of BFS technology in pharmaceuticals include:
- Liquid Pharmaceuticals: BFS is widely used for packaging liquid pharmaceuticals such as eye drops, nasal sprays, oral solutions, and injectables. The aseptic nature of BFS ensures product sterility and prolonged shelf life.
- Parenteral Medications: BFS technology is commonly employed for the packaging of parenteral medications, including vials, ampoules, and pre-filled syringes. It provides a sterile and hermetically sealed container, ensuring the safety and efficacy of injectable drugs.
- Inhalation Products: BFS is suitable for packaging inhalation products such as metered-dose inhalers (MDIs) and dry powder inhalers (DPIs). It helps in maintaining the integrity and sterility of the inhalation formulations.
- Ophthalmic Products: BFS technology is ideal for packaging ophthalmic products like eye drops, eye ointments, and contact lens solutions. The aseptic packaging process of BFS minimizes the risk of contamination and ensures product safety for delicate eye care formulations.
- Topical Medications: BFS is utilized for packaging topical medications, including creams, ointments, gels, and lotions. It provides a hygienic and hermetically sealed packaging solution, protecting the product from external contaminants.
The BFS machine’s ability to produce aseptic, high-quality, and tamper-evident packaging makes it a preferred choice in the pharmaceutical industry, ensuring the integrity and safety of various medications and healthcare products.
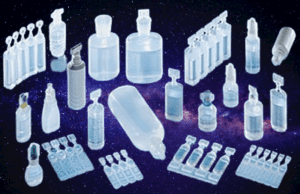
Advantages and disadvantages of Blow-fill-seal (BFS) machine
Advantages | Disadvantages |
---|---|
Aseptic Packaging: Provides sterile product packaging | Limited Container Variety: Restricted to certain shapes |
Product Protection: Hermetic seal prevents contamination | Initial Investment: High cost of acquiring BFS machines |
Extended Shelf Life: Ensures product stability | Equipment Complexity: Requires specialized expertise |
High Production Efficiency: Continuous and automated process | Mold Design and Changeover: Time-consuming and costly |
Reduced Material Usage: Minimizes material waste | Batch Sizes: More suitable for large-scale production |
Cost Savings: Lower labor and packaging costs | Product Compatibility: Limited to certain formulations |
Tamper-Evident Packaging: Enhances product safety | Maintenance and Training: Requires regular upkeep and training |
Difference between bfs and dfs
Aspect | Blow-fill-seal (BFS) | Dry-fill-seal (DFS) |
---|---|---|
Container Formation | Plastic containers are formed by extruding and molding plastic material into the desired shape. | Pre-formed containers (e.g., vials, cups) are used for packaging. |
Filling Process | Product is filled into the containers after they are formed. | Containers are pre-formed and then filled with the product. |
Filling Method | Typically uses precise metering systems or pumps for accurate dosing. | Product is transferred into the containers using specialized equipment. |
Container Sealing | Containers are sealed with a hermetic seal after filling. | Sealing methods can include heat sealing or capping. |
Suitable Products | Primarily used for aseptic packaging of liquid medications, inhalation products, etc. | The product is transferred into the containers using specialized equipment. |
Production Efficiency | High production efficiency with continuous and automated operation. | May require additional steps for cleaning and sterilizing pre-formed containers. |
Container Design Flexibility | Limited to specific container shapes based on the molding process. | Allows flexibility in container design as pre-formed containers can have various shapes. |
Product Compatibility | Suitable for liquid or viscous products. | Suitable for solid or powdered products. |
Equipment Complexity | Requires specialized expertise due to the integration of multiple processes. | Typically simpler in design and operation. |
Packaging Application | Commonly used in pharmaceuticals, particularly for aseptic packaging. | Widely used in pharmaceuticals and other industri |
Validation of the BFS
The qualification process for a Blow-fill-seal (BFS) machine typically involves several steps to ensure that it meets the required standards and specifications. Here are the general steps involved in the qualification of a BFS machine:
- Installation Qualification (IQ):
- Verify that the BFS machine has been installed correctly according to the manufacturer’s guidelines and specifications.
- Ensure that all required utilities, such as power, water, and compressed air, are properly connected and functioning.
- Document the installation details, including equipment location, connections, and any modifications made.
- Operational Qualification (OQ):
- Conduct a series of tests and verifications to ensure that the BFS machine operates within the defined operational parameters.
- Verify and document the machine’s performance in terms of speed, accuracy, and reliability.
- Validate the different functions and controls of the machine, such as material extrusion, molding, filling, and sealing.
- Perform equipment calibration, where applicable, to ensure accurate measurements and dosing.
- Performance Qualification (PQ):
- Validate the BFS machine’s performance by running it under normal operating conditions using representative product formulations and packaging materials.
- Evaluate and document the machine’s performance in terms of product quality, container integrity, and process consistency.
- Conduct tests, such as leak testing, visual inspection, and microbial testing, to ensure the quality and sterility of the packaged products.
- Establish acceptance criteria and compare the actual performance of the machine with the defined specifications.
- Process Validation:
- Perform a thorough validation of the BFS process by conducting a series of tests and evaluations to demonstrate its robustness and consistency.
- Determine critical process parameters and establish appropriate controls to ensure product quality and integrity.
- Document the validation activities, including test protocols, results, and any corrective actions taken.
- Ensure compliance with regulatory requirements, such as Good Manufacturing Practices (GMP) and relevant industry guidelines.
- Ongoing Performance Monitoring:
- Implement a monitoring system to continuously assess and maintain the performance of the BFS machine.
- Conduct routine checks, inspections, and preventive maintenance to ensure the machine’s reliability and functionality.
- Establish a system for documentation, change control, and deviation management to address any modifications or issues related to the BFS machine.
Manufactures (OEM) of the Blow-fill-seal (BFS) machine
blow fill seal machine manufacturers
There are several manufacturers of Blow-fill-seal (BFS) machines worldwide. Here are some prominent manufacturers known for their BFS technology:
- Rommelag (Switzerland): Rommelag is a leading global manufacturer of BFS machines, specializing in aseptic packaging solutions for the pharmaceutical, biotech, and healthcare industries.
- Weiler Engineering (United States): Weiler Engineering is a well-known manufacturer of BFS machines for pharmaceutical and personal care applications. They offer a range of BFS systems, including small-scale laboratory units and high-speed production machines.
- Agronova (Spain): Agronova designs and manufactures BFS machines for the pharmaceutical, cosmetic, and healthcare sectors. They offer a range of compact and efficient machines suitable for various production volumes.
- Nephron Pharmaceuticals Corporation (United States): Nephron Pharmaceuticals is a manufacturer of BFS machines and specializes in aseptic pharmaceutical manufacturing. They provide customized BFS solutions for their own pharmaceutical production needs.
- Shibuya Corporation (Japan): Shibuya Corporation is a Japanese company that offers BFS machines for pharmaceutical and healthcare applications. They have a strong presence in the Asian market and provide advanced BFS technology.
In India, there are a few manufacturers of Blow-fill-seal (BFS) machines as well. Some notable BFS machine manufacturers in India include:
- Aseptic Technologies India Pvt. Ltd. (ATI): ATI is a subsidiary of the Rommelag Group and manufactures BFS machines in India. They provide aseptic packaging solutions for the pharmaceutical, biotech, and healthcare industries.
- Gansons Limited: Gansons Limited is an Indian company that manufactures BFS machines for the pharmaceutical industry. They offer a range of BFS systems suitable for small to large-scale production.
It’s worth noting that the list is not exhaustive, and there may be other manufacturers and suppliers of BFS machines worldwide and in India. It’s always recommended to research and contact the manufacturers directly for the most up-to-date information on BFS machine availability and specifications.
Frequently Asked Questions
What is the working principle of a Blow-fill-seal (BFS) machine?
Answer: The working principle involves heating and molding plastic material, blowing it into a container shape, filling it with the product, and sealing it to create a hermetic package.
What are the common applications of BFS machines?
Answer: BFS machines are commonly used for aseptic packaging of pharmaceuticals, including liquid medications, inhalation products, ophthalmic solutions, and parenteral drugs.
How does a BFS machine ensure product sterility?
Answer: BFS machines provide a sterile environment throughout the packaging process, including sterilization of the plastic material, aseptic filling, and hermetic sealing.
What materials are typically used in BFS packaging?
Answer: BFS packaging is primarily done with thermoplastic polymers, such as polyethylene, polypropylene, or cyclic olefin copolymers (COCs).
How does a BFS machine control the filling volume accurately?
Answer: The filling volume is controlled through precise metering systems, such as pumps or mass flow meters, which accurately deliver the desired quantity of product into each container.
What sealing methods are used in BFS machines?
Answer: BFS machines employ various sealing methods, including heat sealing, ultrasonic sealing, and applying pre-formed caps or closures.
How is the quality of the BFS containers ensured?
Answer: The quality of BFS containers is maintained through rigorous quality control measures, including visual inspections, leak testing, and microbial testing.
What factors affect the production speed of a BFS machine?
Answer: Production speed depends on factors such as container size, complexity, filling volume, sealing method, and the machine’s capabilities.
How is the aseptic environment maintained during BFS operation?
Answer: The BFS machine incorporates sterile zones, including HEPA filters, laminar airflow, and controlled air quality, to maintain an aseptic environment.
What measures are taken to prevent cross-contamination in a BFS machine?
Answer: Cross-contamination is prevented through proper cleaning and sanitization procedures, dedicated production zones, and controlled airflow to avoid product contact between different batches.
What are the critical parameters for plastic material heating in a BFS machine?
Answer: Critical parameters include heating temperature, heating time, and uniform heating to ensure proper plastic material flow and molding.
How is the blowing pressure determined in a BFS machine?
Answer: Blowing pressure is determined based on the mold design, plastic material thickness, desired container shape, and container strength requirements.
What measures are taken to ensure accurate filling in a BFS machine?
Answer: Accurate filling is achieved through precise metering systems, control of filling pressure, and synchronization with the container’s position.
How is the sealing temperature determined in a BFS machine?
Answer: The sealing temperature is determined based on the plastic material properties, such as its melting temperature and desired seal quality.
What are the main maintenance requirements for a BFS machine?
Answer: Regular maintenance includes cleaning, lubrication, calibration of sensors, replacement of worn-out parts, and periodic inspection of critical components to ensure optimal machine performance.
You may also read about Microbiology Guidelines
Request – Quote–A Lab scale-single head BFS machine