In the pharmaceutical industry, ensuring the integrity and efficiency of filtration systems is of utmost importance. The bubble point test has emerged as a critical tool for quality assurance, allowing pharmaceutical manufacturers to evaluate the performance and reliability of filters. This article explores the significance of the bubble point test in the pharmaceutical industry and its role in upholding product quality and patient safety.
Bubble Point Test: The bubble point test is a widely utilized method for assessing the integrity of filters in pharmaceutical applications. It determines the minimum pressure required to initiate liquid flow through the filter media. By subjecting filters to increasing pressures, the test detects any defects, pore blockages, or inconsistencies that may compromise the filter’s efficiency and ability to retain particulate matter.
Filter Validation and Quality Assurance: Pharmaceutical manufacturers rely on the bubble point test as part of their filter validation process to ensure regulatory compliance and maintain stringent quality standards. The test provides quantitative data that validates the filter’s performance, confirming its suitability for critical processes such as sterilization, purification, and particle removal.
Detecting Critical Filter Defects: During the bubble point test, if a filter exhibits excessive bubble formation at a pressure lower than the expected threshold, it indicates potential defects or compromised integrity. These defects can include cracks, pinholes, improper membrane adhesion, or uneven pore size distribution. Identifying such issues early on allows manufacturers to take corrective actions, preventing potential product quality issues and ensuring consistent filtration performance.
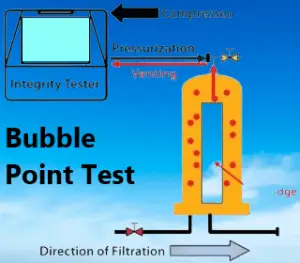
Ensuring Product Quality and Patient Safety: In the pharmaceutical industry, product quality and patient safety are paramount. By incorporating the bubble point test into quality control protocols, manufacturers can confidently validate filters and maintain the efficacy of their filtration systems. Reliable filters ensure the removal of contaminants, microorganisms, and particulate matter, safeguarding the integrity of pharmaceutical products and protecting patients from potential harm.
Process Optimization and Efficiency: The bubble point test not only serves as a tool for quality assurance but also enables manufacturers to optimize their filtration processes. By identifying the optimal pressure range for a filter, manufacturers can maximize its efficiency while ensuring reliable performance and longevity. This knowledge facilitates process optimization, reduces filtration cycle times, and enhances overall manufacturing efficiency.
Bubble point test principle
The bubble point test is based on the principle of capillary action and pressure differentials across a filter membrane. It is used to evaluate the integrity and pore size distribution of filters in various industries, including the pharmaceutical industry. The test determines the minimum pressure required for a liquid to penetrate the filter and initiate flow.
During the bubble point test, the filter membrane is wetted with a suitable liquid to ensure complete saturation and removal of any trapped air. Gradually increasing pressure is then applied to the upstream side of the filter. As the pressure increases, the liquid attempts to penetrate the filter pores.
At a certain pressure, known as the bubble point pressure, the capillary forces within the filter pores are overcome, and the liquid starts to pass through the pores, resulting in the formation of bubbles on the downstream side of the filter. This pressure represents the minimum pressure required for the liquid to break through the filter’s pore structure.
The bubble point pressure is an indicator of the filter’s ability to retain particulate matter, microorganisms, and other contaminants of a certain size. It is influenced by various factors such as filter material, pore size, surface tension of the wetting liquid, and filter cleanliness.
By measuring and recording the bubble point pressure, operators can assess the integrity of the filter and detect any defects, cracks, or pore blockages that may compromise its performance. The test helps ensure that filters meet specified standards and can effectively retain particles, thereby contributing to product quality, process efficiency, and patient safety.
In summary, the principle of the bubble point test lies in applying pressure to determine the minimum pressure required for a liquid to penetrate the filter and initiate flow, providing valuable insights into the filter’s integrity and performance.
Integrity Testing Methods
Filtration systems, and maintaining the integrity of filters are crucial to ensure optimal performance and the production of high-quality products. Integrity testing methods serve as valuable tools for assessing the structural integrity and efficiency of filters.
Bubble Point Test:
One of the fundamental integrity testing methods is the bubble point test. This test determines the minimum pressure required for a liquid to penetrate through the filter membrane, detecting any potential defects or pore blockages. By assessing the bubble point pressure, operators can gauge the filter’s ability to withstand pressure differentials and effectively retain particulate matter.
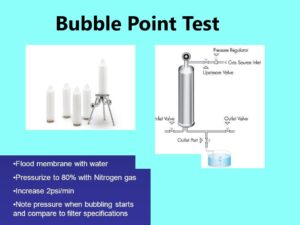
Diffusion Test:
The diffusion test, also known as the water intrusion test, evaluates the filter’s ability to resist the passage of liquid under pressure. It involves applying controlled pressure to the upstream side of the filter and measuring the liquid flow rate. This test helps identify any defects or inconsistencies in the filter membrane, enabling operators to take corrective measures promptly.
Pressure Hold Test:
The pressure hold test examines the filter’s ability to retain a specified pressure over a certain period. It assesses the filter’s integrity and ensures that it can withstand the applied pressure without any leaks or failures. By monitoring pressure fluctuations, this test provides valuable insights into the filter’s performance and reliability under sustained pressure conditions.
Forward Flow Test:
The forward flow test evaluates the filter’s capacity to allow liquid to pass through the filter media under specified flow rates. This test measures the flow rate and compares it to predefined limits, ensuring that the filter operates within the desired parameters. Deviations from the expected flow rate can indicate potential issues requiring further investigation.
Bubble Point Diffusion Test:
The bubble point diffusion test combines the principles of the bubble point test and diffusion test to comprehensively assess filter integrity. By measuring both the bubble point pressure and the diffusion flow rate, this test offers a comprehensive evaluation of the filter’s structural integrity and ability to resist liquid penetration under pressure.
Bubble point test procedure
SOP for Bubble Point Test:
Step 1: Equipment Preparation To commence the bubble point test, gather the necessary equipment, including a pressure gauge, a filtration apparatus, a clean and dry filter membrane, a pressure source, and a suitable test fluid. Thoroughly inspect the equipment for any defects or contamination to ensure accurate and reliable results.
Step 2: Filter Wetting Immerse the filter membrane in the test fluid, ensuring complete saturation. Allow the filter to equilibrate for a specific duration to eliminate any air trapped within the pores. This crucial step facilitates optimal flow and accurate measurement during subsequent stages.
Step 3: Assembling the Filtration Apparatus Carefully assemble the filtration apparatus, ensuring tight connections and a leak-free setup. Attach the wetted filter membrane to the apparatus, securing it in place. Maintain cleanliness and handle the assembly with precision to prevent any potential sources of error.
Step 4: Applying Pressure Gradually apply pressure to the filtration apparatus using the chosen pressure source. Observe the pressure gauge and note the pressure at which the first stream of bubbles emerges from the filter surface. This pressure, known as the bubble point pressure, signifies the minimum pressure required for the fluid to overcome the capillary forces and initiate flow through the filter.
Step 5: Measuring Bubble Point Pressure Accurately record the bubble point pressure as the point of equilibrium where the filtered fluid starts to flow steadily without additional bubble formation. This pressure reading is a critical parameter in assessing the filter’s efficiency and integrity.
Step 6: Validating Results Compare the obtained bubble point pressure with the specified limits defined for the particular filter type. Evaluate the results based on established acceptance criteria to determine the filter’s performance. Any deviations from the defined limits may indicate potential issues requiring corrective action.
Step 7: Documentation and Reporting Document the entire bubble point test procedure, including the equipment used, test fluid details, observed pressure values, and any relevant observations. Maintain a comprehensive record to ensure traceability and facilitate future analysis. Generate a comprehensive report summarizing the test results, highlighting any deviations or noteworthy findings.
Bubble point test formula an example
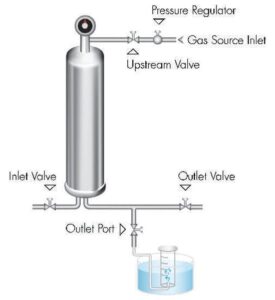
The bubble point test does not involve a specific mathematical formula for calculation. It is a qualitative test that determines the minimum pressure at which bubbles start to form and pass through a filter membrane. However, I can provide you with an example calculation to demonstrate the concept.
Let’s assume we are conducting a bubble point test on a filter membrane, and during the test, the first stream of bubbles is observed at a pressure of 2.5 bar (250 kPa). This pressure is noted as the bubble point pressure.
In this example, the calculation involves recording the observed pressure at which the bubbles appear, rather than applying a formula. The pressure is typically measured using a pressure gauge or a pressure transducer.
Bubble point test equipment
The bubble point test requires specific equipment to accurately measure the pressure at which bubbles start to form and pass through a filter membrane. The following are some of the essential equipment used in conducting a bubble point test:
- Pressure Source: A pressure source is necessary to apply increasing pressure to the upstream side of the filter during the test. This can be a pressure regulator, a compressed gas cylinder, or a pump that can generate controlled pressure.
- Filtration Apparatus: The filtration apparatus holds the filter membrane in place and allows the passage of the test fluid. It typically consists of a filter housing or holder that securely holds the filter, along with appropriate connections and fittings.
- Pressure Gauge or Transducer: A pressure gauge or transducer is used to measure the pressure applied to the filter during the test. It provides a visual or digital display of the pressure values, allowing for accurate readings.
- Test Fluid: A suitable test fluid, compatible with the filter and the intended application, is required to wet the filter membrane and conduct the test. The choice of test fluid depends on the specific requirements and compatibility considerations.
- Stopwatch or Timer: A stopwatch or timer is useful for monitoring the duration of the test and recording the time when the first stream of bubbles appears.
- Clean and Dry Filter Membrane: A filter membrane, appropriate for the specific test requirements and pore size, is selected. The filter membrane should be clean and dry before conducting the test.
Frequently Asked Questions
What is the purpose of the bubble point test in the pharmaceutical industry?
Answer: The bubble point test is performed to assess the integrity and performance of filters used in pharmaceutical applications.
How does the bubble point test help in ensuring product quality?
Answer: By detecting filter defects and pore blockages, the bubble point test ensures that the filters can effectively retain particulate matter and microorganisms, thereby maintaining product quality.
What are the common test fluids used in the bubble point test?
Answer: Test fluids such as water, air, or other compatible liquids are used based on the filter type and intended application.
What equipment is required to conduct a bubble point test?
Answer: The equipment typically includes a pressure source, filtration apparatus, pressure gauge or transducer, test fluid, stopwatch or timer, and a clean and dry filter membrane.
How is the bubble point pressure determined during the test?
Answer: The bubble point pressure is determined by gradually increasing the pressure until the first stream of bubbles is observed on the downstream side of the filter.
What factors can influence the bubble point pressure obtained during the test?
Answer: The bubble point pressure can be influenced by factors such as filter type, pore size, wetting liquid, surface tension, and filter cleanliness.
What does a lower bubble point pressure indicate?
Answer: A lower bubble point pressure may indicate defects, cracks, or pore blockages in the filter, compromising its integrity and performance.
How is the bubble point test related to filter validation?
Answer: The bubble point test is an essential part of filter validation, ensuring that the filters meet regulatory requirements and perform effectively in critical pharmaceutical processes.
What acceptance criteria are used to evaluate the bubble point test results?
Answer: Acceptance criteria are typically defined based on the filter specifications and industry standards, ensuring that the bubble point pressure falls within an acceptable range.
How can the bubble point test help optimize filtration processes?
Answer: By identifying the optimal pressure range for a filter, the bubble point test helps optimize filtration processes, reducing cycle times and enhancing overall manufacturing efficiency.
What are the potential sources of error in the bubble point test?
Answer: Sources of error can include improper filter wetting, air bubbles trapped in the system, equipment calibration issues, or human error in pressure readings.
Can the bubble point test be used for both hydrophobic and hydrophilic filters?
Answer: Yes, the bubble point test is applicable to both hydrophobic and hydrophilic filters, although the choice of test fluids may differ based on the filter type.
How does the bubble point test contribute to patient safety?
Answer: By ensuring the integrity of filters, the bubble point test helps prevent the passage of contaminants and microorganisms, safeguarding patient safety in pharmaceutical products.
Can the bubble point test be performed in-line during manufacturing processes?
Answer: In certain cases, the bubble point test can be adapted for in-line testing, providing real-time assessment of filter performance and allowing for immediate corrective actions if needed.
How should the results of the bubble point test be documented and reported?
Answer: The results should be documented, including details such as equipment used, test fluid, observed pressure values, any deviations or observations, and a comprehensive report summarizing the test results. This documentation ensures traceability and facilitates future analysis and audits.