Pharma-grade Water is the most important utility used by the pharma industry. It may be present as an excipient or used for the reconstitution of products, during synthesis, during the production of the drug product, or as a cleaning agent for rinsing vessels, equipment, primary packaging m
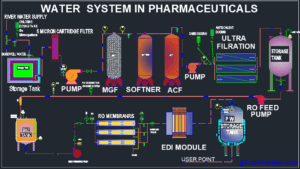
aterials, etc. There are different grades of water quality are required as per the utilization of water in the pharma generally used as excipients and cleaning.The pharmaceutical sector invests significant resources in the creation and upkeep of water purification systems since controlling water quality, especially microbiological purity, is a crucial priority.
Purified water quality describes in the following Guidelines:
- USP: US Pharmacopeia.
- IP: Indian Pharmacopeia.
- BP: British pharmacopeia.
- European Pharmacopoeia.
- WHO TRS (Technical report Sheet).
- USFDA: High Purity Water System (7/93).
- ICH: International Council for Harmonization.
Important Parameters of Pharma grade water:
Parameters | Purified Water (PW) | Water for injection (WFI) |
Conductivity | < 1.3 µS/cm @25 °C | < 1.3 µS/cm @25 °C |
pH | 5.0 -7.0 | 5.0 -7.0 |
Total Organic Carbon (TOC) | < 500 ppb | < 500 ppb |
Total bioburden | < 10,000 CFU/100 mL | < 10 CFU /100 mL |
Endotoxin | N/A | < 0.25 Endotoxin Units/mL |
Coliform Level | 0/100 mL | 0/100 mL |
Chemistry of water:
Water consists of 2 hydrogen atoms and 1 oxygen atom. They are both hydrogen and oxygen atoms attracted to each other due to their electrostatic attraction.
All that means is the hydrogen atom is positively charged, while the oxygen atom is negatively charged. Opposites attract, and water is no different.
Due to the charge Water attracts other water. In the same manner that the atoms are combined. The hydrogen of one water molecule will bond to the oxygen atom of another molecule.
Physical: pH, conductivity, turbidity, color, etc.
Chemical: (a) Organic e.g., Trihalomethane, pesticides, etc.
(b) Inorganic: Nutrient, ion & Heavy metals, etc.
Biological: Algae, zooplankton, macroinvertebrates, etc.
Bacteriological: Total coliform, E. coliform, plate count.
Water System techniques and major processes while producing Purified water:
Generally, water systems in pharma industries have two parts:
- Pre-treatment section.
- PW (pharmacopeial grade) generation system.
1. Pre-Treatment section of the water system which generates Portable water:
- Source of water: Generally, in India, the main source of water is River water or Ground/Borewell water.
- Chlorination: This is a chemical treatment of water in which Pre-chlorination for algae control, microorganism growth, and arresting biological growth.
- Storage tanks and Sedimentation.: Then this chlorinated water is stored in a storage tank either underground or overhead Tanks. So, industries design these tanks as per design in which the lower area of the tank settles the large particle, this process is called sedimentation or physical treatment.
- Bag filters 10 Micron.:Bag filters are used to remove the bigger particles of more than 10 microns.
- MGF, Multigrade Filters: Multi Grade Filter consists of vertical or horizontal vessels having pressure sand filters, that contain multiple layers of course and fine sand (pebbles and gravels) in a fixed proportion. This is a filter bed that has adequate pores that retain the large and small suspended solid, un-dissolved impurities and dust particles. This MGF system works on higher specific flow rates at lower costs. MGF system has high throughputs, high dirt-holding capacity, and capacity to reduce turbidity and TSS (< 5ppm) from water. MGF contains the media like finest sand, Gravel & Pebbles.
- ACF, Activated carbon Filter.: Activated Carbon filter has the media in which the adsorptive removal of color, aroma, taste, and other harmful organics and inorganics from drinking water.
- De-chlorination (Sodium metabisulphite SMBS): Sodium metabisulphite is used as an antioxidant agent. SMBS is widely used for the removal of excess chlorine from the water system. SMBS act in order to remove dissolved oxygen from water, as an oxygen diver.
- Softener: – Softener is a cylindrical vessel that is used to remove the impurities from water and make it soft water. This vessel has a resin bed in its body. This process is called ion exchange and removes harsh manganese, iron, calcium, and magnesium ions from water. The resin of the softener acts as industrial hard water treatment and replaces the hardness in the water with salt (brine) that is regenerated periodically. Softener Application and parts:
- Reduce the water hardness.
- Size of system and flow rates.
- Control heads types.
- FRP vs. steel tank.
- Top-mounted valves vs. face-piping.
- Resins
- Softener can easily remove water hardness without high-pressure or harmful chemicals and also helps to control alkalinity.
- Anti Scalent dosing to protect membranes from the scale.: Antiscalant chemicals are used to preserve the RO membranes from scaling and fouling. Mineral fouling such as calcium sulphate, calcium carbonate, barium sulphate, silica, calcium fluoride, and strontium sulphate can be found in the scale. To break up sulphate precipitates, calcium carbonate, and other mineral fouling, antiscalants should be dosed prior to reaching the RO membranes.
- Ultrafiltration: Ultrafiltration is also the filtration process to filter water and remove impurities from the water. Ultra-filters have a size of 0.01 μm to 0.1 μm. Ultrafiltration is used to remove particles, some protozoa, viruses, and bacteria from the flow of water. The water which passed through the ultrafiltration membrane is called permeate water. Ultra-filtration is an excellent way to remove pyrogen contaminations from water.
- Storage Tank and pumps: Storage tanks of ss 304 or HDPE tanks are used to store the pre-treated water and pumped through a mechanical Pump to purify the water generation system.
2. Purified water (PW) generation system.
- Reverse Osmosis
- Deionization and Ionization by EDI.
- In the old method, Mix Bed was used for Deionization and Ionization.
- UV Treatment.
1.0 Reverse Osmosis System: –
Osmosis is a natural phenomenon by which water flows across a semi-permeable membrane and it allows water to pass through, while does not allow salts.
But in Reverse Osmosis Additional pressure applied will cause water to flow in a reverse direction from the high salt side to the low salt side. This is known as reverse osmosis.
Now for the generation of purified water in the pharma industries used HSRO heat-suitable reverse osmosis membrane elements which deliver outstanding quality water with the added capability to withstand sanitization with hot water.
2.0 Deionization and Ionization by ED
High-purity water production is done by the combination of membrane separation and ion exchange processes.
EDI is a high-efficiency demineralization process that combines semi-permeable membrane technology with ion-exchange media.
Electrical current and specially prepared membranes that are semi-permeable to ions based on their charge, electrical current, and ability to reduce the ions based on their charge are used in electrodialysis. Electrical potential transports and separates charged aqueous species via electrodialysis.
The electrical current is used to regenerate the resin continuously, eliminating the need for periodic regeneration.
The main form of an EDI stack is the same as that of a de-ionization chamber. In the chamber, an anionic exchange membrane and a cationic exchange membrane are sandwiched by an ion exchange resin.
Only ions can pass through the membrane; water cannot. Several processes are initiated when flow enters the resin-filled diluting compartment. The mixed bed resins scavenge strong ions from the feed stream.
Charged ions are pulled off the resin and drawn towards the respective, oppositely-charged electrodes by the strong direct current field applied across the stack of components.
These charged strong-ion species are continuously removed and transferred into the adjacent concentrating compartments in this manner.
The following are the ionization reactions that occur in the resin in hydrogen or hydroxide forms for the removal of weakly ionized compounds:
CO2 + OH- ==> HCO3-
HCO3- + OH- ==> CO32-
SiO2 + OH- ==> HSiO3-
H3BO3 + OH- ==> B(OH)4-
NH3 + H+ ==> NH4+
Advantages: Some of the benefits of EDI over traditional ionic interchange systems include:
- Operation is simple and continuous.
- Chemicals used in regeneration have been completely eliminated.
- Low-cost operation and maintenance.
- Power consumption is minimal.
- Non-pollution, security, and dependability
- It necessitates very few automatic valves or complex control sequences that require operator supervision.
- It takes up little room.
- It continuously produces high-purity water.
- It completely removes dissolved inorganic particles.
- It removes more than 99.9% of ions from water when combined with reverse osmosis pre-treatment.
Disadvantages:
- EDI cannot be used for water with a hardness greater than one because the calcium carbonate would form a scab in the concentrated one’s screen, limiting the operation.
3.0 Mix Bed:
Mix Bed works the same as EDI work. Mix bed is the conventional method having anionic and cationic media/ resin in its vessels to remove the free ions from the RO water.
Mixed bed resins, also known as mixed bed ion exchange resins, are commonly used in the water purification sector to polish process water to produce high-quality demineralized water (such as after a reverse osmosis system). As the name implies, a mixed bed is made up of strong acid cation exchange and strong base anion exchange resin.
4.0 UV Treatment:
UV water purification systems purify water by killing microorganisms in the water with ultraviolet rays. UV rays kill water-borne microorganisms and prevent their reproduction by interfering with their DNA. Furthermore, UV rays do not cause chemical changes in water. As a result, UV-purified water contains no harmful microorganisms and retains its original taste.
Water Quality Monitoring
Qualification of Purified Water in Pharma Industries:
The qualification of the purified water is held in three phases as per the following details:
- Phase 1 (investigational phase): A test period of 2-4 weeks – monitor the system. The whole PW generation, storage, and distribution loop line have in operation continuously without deviation. Chemical and microbiological testing should include in accordance with a Defined plan.
- Phase 2 (The verification step): After completion of phase 1. For the next 2-4 weeks all parameters will be tested and intensively monitored. Also, we check for the system utilization are as per the sops after the satisfactory completion of phase 1, sampling scheme generally the same as in phase 1 water can be used for manufacturing purposes during this phase.
- Phase 3 (Final Approval): Over 1 year after the satisfactory completion of phase 2, Water can be used for manufacturing purposes during this phase, Demonstrate: Extended reliable performance That seasonal variations are evaluated. PW sample locations, periodic sampling frequencies, and Based on established protocols validated during stages 1 and 2, test types should be restricted to the typical routine pattern.
FAQ:-
What is water system in pharmaceutical industry?
Answer: In the pharmaceutical and biotechnology sectors, purified water is frequently utilized during production as well as for washing tools, containers, etc. Due to its capacity to absorb, suspend, or dissolve different substances, water does not exist in pure form in nature. To create water for pharmaceutical use (WPU), bugs and minerals must be eliminated from even clean drinking water from the mains. As described in many pharmacopeias, WPU is categorized based on how the patient is delivered the pharmaceutical substance (European Pharmacopoeia, United States Pharmacopoeia, Japanese Pharmacopoeia, etc.).
What are the types of pharmaceutical water system?
Answer:- There are various kinds of pharmaceutical water based on the utilization major are Purified water and Strile water i.e. Water for Injection (WFI).
What are the components of water system in pharmaceutical industry?
Answer: major components of the water system are the following:
- Pretreatment (MGF, ACF, Softner, Chemical dosing setup, etc.).
- Reverse osmosis system (RO).
- EDI.
- Storage Tank.
- Distribution System.
- Online testing 7 controlling ( TOC analyzer, Conductivity meter etc.)
What is water validation in pharma?
Answer: Validation of the PW & WFI will be done in the 3 phases as described above.
Manufacturers of water Systems in India:
There are many manufacturers of the water system In India, some of the best and legacy OEMs are:
- Praj Hipurity
- CN waters
- TSA
- Hydropure
- Induionpure
- Rapid ion waters
- Biocell system
For more information on water system-related setup, please write us at: admin@flairpharma.com
Nice
Nice ….👍
Good job 👍
Good work sir
Good job sir🙂🙂
Good job 👍
Nice and hood