Transform your pharmaceutical formulation processes with our cutting-edge Apparent Bulk Density Apparatus. This sophisticated tool leverages precise measurement techniques, enabling accurate determination of apparent bulk density. In our plant, this apparatus serves as a technological cornerstone, facilitating the creation of pharmaceutical products with unparalleled precision and quality. Elevate your efficiency, ensure formulation consistency, and exceed regulatory standards seamlessly with our state-of-the-art apparatus for superior results in pharmaceutical development.
Working Principle of the Bulk Density Apparatus
The working principle of a bulk density apparatus involves measuring the mass of a known volume of particulate material to determine its bulk density. There are various methods for conducting bulk density measurements, and the working principle can vary based on the specific method used. Here, we’ll provide a general overview of the working principle, considering the ASTM D1895 Method A as an example:
Working Principle as per (ASTM D1895 Method A)
- Preparation:
- The apparatus includes a V-shaped funnel, a measuring cup with a known volume (e.g., 100 cm³), and a stand with a funnel shut-off mechanism.
- The material under test, typically fine granules, is poured through the V-shaped funnel.
- Filling the Measuring Cup:
- The material flows freely through the funnel and fills the measuring cup up to its known volume.
- Weighing the Material:
- The filled measuring cup, now containing the material, is weighed to determine its mass accurately.
- Calculating Bulk Density:
- The bulk density is calculated using the formula: Bulk Density = Mass / Volume.
- The volume is the known volume of the measuring cup.
- Reporting Results:
- The results are reported as the bulk density of the material in grams per cubic centimeter (g/cm³) or other appropriate units.
Additional Notes:
- The test may be conducted under controlled conditions, and the apparatus may include features to minimize external factors affecting the measurements.
- For other methods (e.g., ASTM D1895 Method B, Method C, ISO R60), the apparatus and procedures may differ, but the fundamental principle involves measuring the mass and volume of the material to determine its bulk density.
- Tapped density measurements, which involve compacting the material through tapping, are also used to assess the powder’s behavior under compression.
It’s crucial to follow the specific method’s guidelines and standards to ensure accurate and reproducible bulk density measurements. The working principle remains consistent across methods, emphasizing the relationship between mass and volume for determining bulk density.
Powder analysis is a critical aspect of pharmaceutical and industrial processes, where the physical properties of powders play a crucial role in formulation and manufacturing. The Bulk Density Apparatus is a sophisticated tool designed to measure the bulk and tapped densities of powders, providing valuable insights into their behavior and characteristics.
Bulk Density and Its Significance: The bulk density of a powder is defined as the ratio of the mass of an untapped powder sample to its volume, including the interparticulate void volume. It is expressed in grams per milliliter (g/mL) and is a key parameter influenced by both the density of powder particles and their spatial arrangement within the powder bed. The bulk density is highly sensitive to how the sample is handled, prepared, treated, and stored.
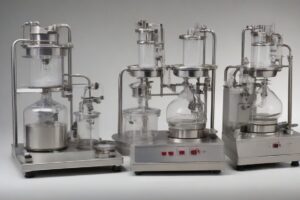
Methods for Bulk Density Measurement: The Bulk Density Apparatus employs various methods for accurate measurements, with Method I utilizing a graduated cylinder, Method II employing a volumeter, and Method III utilizing a vessel. Each method has its advantages and may be favored depending on the nature of the powder being analyzed.
- Method I – Measurement in a Graduated Cylinder:
- A known weight of the powder is introduced into a graduated cylinder.
- The bulk density is calculated by dividing the mass by the unsettled apparent volume of the powder.
- Method II – Measurement in a Volumeter:
- The apparatus consists of a funnel fitted with a 1.0-mm sieve mounted over a baffle box.
- Powder flows through the sieve, bounces off glass baffle plates, and is collected in a cup.
- The bulk density is determined based on the volume of the collected powder.
- Method III – Measurement in a Vessel:
- A cylindrical vessel is mechanically tapped to settle the powder.
- Tapped density is calculated by dividing the mass of the powder in the vessel by the final tapped volume.
Tapped Density and Measures of Powder Compressibility: Tapped density is an increased bulk density achieved by mechanically tapping the powder. The Compressibility Index and Hausner Ratio are measures derived from bulk and tapped densities, providing insights into the powder’s ability to settle and the significance of inter particulate interactions.
- Compressibility Index:
- Calculated as (100 * (V0 – VF) / V0), where V0 is the unsettled apparent volume, and VF is the final tapped volume.
- Indicates the propensity of the powder to be compressed.
- Hausner Ratio:
- Calculated as V0 / VF.
- Provides an assessment of the relative importance of interparticulate interactions.
Conclusion: The Bulk Density Apparatus, with its versatile methods and associated measures, serves as a cornerstone in understanding and characterizing powder properties. Its application in pharmaceutical and industrial settings ensures precision in formulation processes, quality control, and compliance with global pharmacopeias. The nuances of bulk and tapped densities, along with compressibility indices, offer valuable information for optimizing powder handling and manufacturing efficiency.
Applications of Bulk Density Apparatus
Applications of Bulk Density Apparatus |
---|
Density Testing |
– Measuring apparent density of materials. |
Hardness Testing |
– Assessing the hardness of materials, |
especially relevant for pharmaceuticals. |
Melt Flow Testing |
– Analyzing the melt flow characteristics of materials, crucial for certain processes. |
Quality Control in Pharmaceuticals |
– Ensuring consistency and quality in the manufacturing of pharmaceutical products. |
Material Characterization |
– Understanding material behavior and properties, aiding in process optimization. |
– Measuring the apparent density of materials. |
– Conforming to ASTM D1895 and ISO R60 standards for regulatory compliance. |
Versatility in Material Testing |
– Catering to various materials, from fine powders to large flakes and fibers. |
Process Optimization |
– Providing insights into material behavior, assisting in optimizing manufacturing. |
Pourability Assessment |
– Evaluating how well materials pour through specific funnels, relevant in various industries including pharmaceuticals. |
These applications highlight the diverse uses of Bulk Density Apparatus in different industries, with a focus on pharmaceuticals, material testing, and quality control processes.
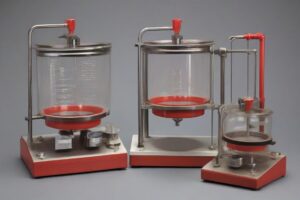
Advantages and Disadvantages of the Bulk Density Apparatus
Precise Measurement: Offers accurate and precise measurements of bulk density, crucial for pharmaceutical formulations. | Sensitivity to Handling: Bulk density can be sensitive to how the material is handled, affecting results. |
Quality Control: Plays a vital role in quality control processes to ensure consistency in pharmaceutical products. | Material Handling: The apparatus may require careful handling to avoid introducing errors in measurements. |
Versatility: Different methods cater to various materials, from fine powders to large granules, offering versatility. | Calibration Challenges: Regular calibration is essential to maintain accuracy, adding to maintenance efforts. |
Process Optimization: Helps in optimizing manufacturing processes by providing insights into material behavior. | Time-Consuming: Some methods, especially tapping procedures, can be time-consuming. |
Regulatory Compliance: Complies with ASTM and ISO standards, ensuring adherence to regulatory requirements. | Equipment Cost: Initial investment and Maintenance costs may be relatively high. |
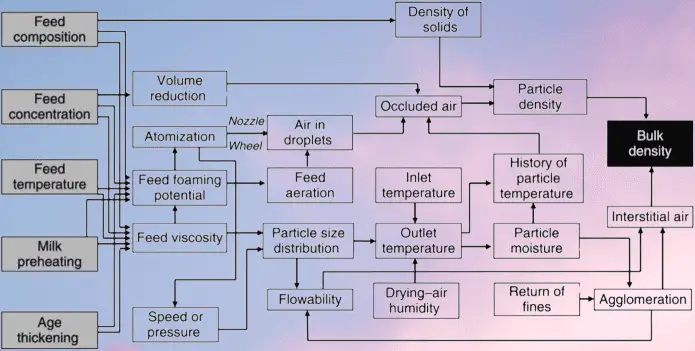