The objective of this Standard Operating Procedure Cleaning and Preventive Maintenance of Filter Cleaning Station is to outline the steps and guidelines for conducting the cleaning and preventive maintenance of a Filter Cleaning Station to ensure effective filtration, optimal performance, and safety.
SOP for Cleaning and Preventive Maintenance of Filter Cleaning Station
- OBJECTIVE:
- To lay down the Procedure for Cleaning and Preventive Maintenance of Filter Cleaning Station installed in technical area.
- SCOPE:
- This SOP is applicable to cleaning & Cleaning and Preventive Maintenance of Filter Cleaning Station installed in technical area .
- RESPONSIBILITY:
- Technician/ Operator shall be responsible for proper execution of Cleaning and Preventive Maintenance of Filter Cleaning Station as per SOP.
- Engineering – Head shall be responsible for reviewing the SOP and for ensuring proper execution of preventive maintenance.
- ACCOUNTABILITY:
- Engineering – Head shall be accountable for proper implementation of the SOP.
- DEFINITIONS:
- Preventive Maintenance: The Cleaning and Preventive Maintenance of Filter Cleaning Station describes all scheduled work done on a routine, predefined basis to maintain facilities, equipment, utilities and devices in good status in order to ensure reliable performance.
- PROCEDURE:
- SOP for the Cleaning and Preventive Maintenance of Filter Cleaning Station shall be executed as per the SOP No.: SOP/EN/XXXYYY – Execution of Preventive Maintenance.
- Ensure that the Spare parts are available at the time of preventive maintenance.
- Cleaning and Preventive Maintenance of Filter Cleaning Station – Mechanical
- Check the piping and pipe fittings
- Physically checked the piping and pipe fittings for any leakages, if required attend the same.
- The frequency is as needed; however it shall be check for every month ±5 days.
- Check the valves
- Switch off the pump.
- Physically checked for smooth movement of valves. If not Smoothly operate then rectify the same.
- Dismantle the both side flanges of the valve for which maintenance is to be carryout.
- Clean the internals, and re-fix the valve in line, if it is not functioning well then replace the same with new one.
- The valve checking frequency is monthly ±5 days.
- Checking and cleaning of water sump
- Switch Off the scrubber.
- Open the main hole; Check the gasket of the main hole.
- Check and clean the water sump to remove the solids deposited.
- Dismantle the level indicator pipe, clean the indicator pipe and re-fix it.
- Make up the Sump level by opening water inlet valve.
- Physically checked for any water leakage.
- Checking frequency shall be after every month ± 5days.
- Checking of duct work
- Switch off the exhaust blower.
- Switch off the water circulation pump.
- Check and clean the exhaust duct.
- Check the end connection of exhaust duct, if required tightens the same.
- Check and inspect the duct for any damage and deterioration.
- Check the exhaust duct for erosion and plugging.
- Checking shall be done after every six month.± 15 days.
- Checking of filter (Mesh)
- Switch off the exhaust blower.
- Switch off the water circulation pump.
- Open the flange nut and bolts.
- Remove the filter, check the condition of filter, if required clean with compressed air and water ; dry the filter and refix it in to the system as earlier, if required replace the filter.
- The checking frequency shall be after every six month.± 15 days.
- Checking and cleaning of venture and spray pipes
- Switch Off the Exhaust blower.
- Switch off the water circulation pump.
- Dismantle the flange & Flexible pipes.
- Physically check any leakage in flexible pipes, cleaning of venture and spray nozzles.
- Checking shall be done every six month ±15 days.
- Preventive Maintenance – Electrical
- Checking of Terminals and Wiring
- Ensure that the power supply to the machine is switched off.
- Visually check all the power and control wiring.
- Check and ensure by using screwdriver that all the wires are properly tightened.
- Checking shall be done monthly±5 days.
- Checking of motor
- Physically check the insulation resistance of motor winding with the help of meagger.
- Check the phase continuity and winding continuity of motor with the help of tong tester.
- Physically check the motor terminal box and terminal connections.
- Check the voltage drawn by motor with the help of multimeter
- Check the current drawn by motor with the help of tong tester.
- Check the motor abnormal sound, if it is then Rectify the same.
- During checking bearing found warn out same is replace with new one.
- Physically check the direction of rotation; it should be as per recommended direction.
- Checking shall be done after every month.±5days.
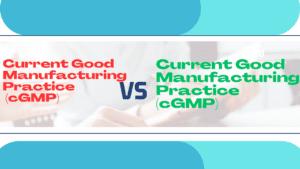
- Post Preventive Maintenance Check List:
- Whenever any modifications and major works are carried out to the equipment, the same shall be mentioned in the equipment history card as per the respective SOP.
- Connect the equipment main power supply and start the equipment.
- Ensure that the equipment is running smoothly, without any abnormality.
- If any abnormality is observed in the above, same will be attended in co-ordination with User Department Head.
- Record the all preventive maintenance activity in Format No. SOP/EN/XXXYYY
- ABBREVIATIONS
- CRF No. : Change Request Form number
- QA : Quality Assurance
- REFERENCES
- Execution of Preventive Maintenance : SOP/EN/XXXYYY
- DISTRIBUTION LIST
- SOP shall be distributed to following departments Quality Assurance, Engineering as per user request.
- ANNEXURES
- Preventive Maintenance checklist & Record for Filter Cleaning Station: SOP/EN/XXXYYY
You may also read about Good Laboratory Practices (GLP)