“To Enhance the Clean in Place (CIP) protocols with Riboflavin Testing. Explore how this advanced technique uses fluorescent dye to meticulously evaluate spray coverage within industrial vessels. Elevate your quality standards and regulatory compliance with effective cleaning validation.”Efficient Clean in Place (CIP) processes are vital for maintaining the cleanliness and functionality of stainless steel process vessels. These vessels often harbor complex structures such as agitators, nozzles, vortex breakers, and man-ways, creating areas that are challenging to clean thoroughly. To ensure comprehensive spray coverage during CIP, a meticulous assessment of spray patterns becomes essential. This article delves into the significance of Riboflavin testing in evaluating CIP spray patterns and optimizing cleaning procedures.
The Significance of Comprehensive Cleaning
In the realm of industrial processes, particularly in sectors like pharmaceuticals, food and beverage, and chemical manufacturing, maintaining pristine process vessels is paramount. The presence of ‘shadowed’ areas within these vessels, where the CIP spray might not effectively reach, poses a significant challenge. Residues left in these uncleaned areas can lead to product contamination, compromised quality, and even operational issues. Riboflavin testing offers a precise solution to this challenge.
Riboflavin Testing Explained
Riboflavin testing involves the application of a fluorescent dye solution within process tanks, followed by the activation of the CIP system. This procedure allows for a meticulous study of the spray patterns and their cleaning efficiency. The dye solution, when illuminated by a long-wavelength UV lamp, fluoresces, indicating the areas that have been thoroughly cleaned and those that may still retain residues.
Materials and Procedures
The Riboflavin testing process requires specific materials and adherence to certain steps to ensure accuracy:
Materials:
- Riboflavin Powder: Riboflavin Orange Powder (reagent grade) or an equivalent.
- Long Wavelength UV Lamp: Used to visualize the fluorescence of the dye solution.
- Water: Used as a carrier for the dye solution and for rinsing.
- CIP Supply Pump: Provides water at a controlled pressure.
- Riboflavin Solution Spray Device: Produces a fine mist spray for even application.
- Calibrated Pressure Gauges and Flow Meters: Ensure precise measurement of parameters.
Testing Procedure:
- Preparation: The tank is positioned in its operational orientation and thoroughly cleaned.
- Dye Preparation: Riboflavin powder is mixed with water to create a 100ppm solution.
- Application: The dye solution is sprayed throughout the tank’s interior, including hard-to-reach areas.
- Inspection: After applying the dye, the tank’s interior is inspected under UV light to observe fluorescence.
- Re-spraying: Any areas with incomplete coverage are re-sprayed for comprehensive cleaning.
Key Critical Parameter in Riboflavin Testing for Cleaning Validation
The primary critical parameter in Riboflavin Testing during cleaning validation is Spray Coverage Uniformity. This parameter directly reflects the effectiveness of the Clean in Place (CIP) process in ensuring thorough cleanliness across all surfaces within industrial vessels.
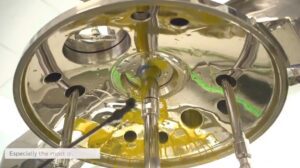
Spray Coverage Uniformity:
- Description: Spray coverage uniformity refers to the consistency and completeness of the fluorescent dye’s distribution on all internal surfaces of the vessel. It ensures that every nook, corner, and intricate structure is reached by the CIP spray.
- Significance: An even distribution of the fluorescent dye indicates that the CIP system is effectively reaching all areas, leaving no residue or contaminants behind. Inadequate coverage may imply that certain shadowed or complex regions haven’t received sufficient cleaning action.
- Evaluation: The fluorescent dye’s fluorescence under UV light serves as a visual indicator of coverage. Areas that fluoresce brightly have been thoroughly cleaned, while dimly fluorescing or non-fluorescing areas may require further attention.
- Measurement: Visual observation and documentation of the fluorescent patterns provide a qualitative assessment of spray coverage uniformity.
- Acceptance Criteria: To meet cleaning validation standards, the spray coverage should be consistent and comprehensive across the entire internal surface, leaving no areas devoid of fluorescence.
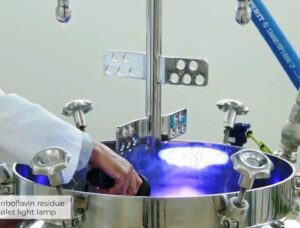
While other parameters, such as dye concentration, spray pressure, and contact time, contribute to the overall success of Riboflavin Testing, the uniformity of spray coverage stands out as the key critical parameter. It ensures that the CIP process achieves its ultimate goal of complete cleanliness in industrial vessels, maintaining product quality, safety, and regulatory compliance.
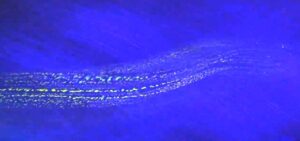
Benefits and Applications of Riboflavin Testing
Riboflavin testing provides several benefits:
- Precision: It pinpoints areas that may not have received adequate spray coverage.
- Validation: It offers documented proof of cleanability, which is crucial for compliance and quality assurance.
- Optimization: It enables optimization of CIP processes, saving time and resources.
Advantages of the Riboflavin Testing in CIP
Advantages of Riboflavin Testing in CIP | |
Advantage | Description |
Precise Cleaning Assessment | Pinpoints areas with incomplete spray coverage, ensuring thorough cleaning. |
Validation of Cleanability | Offers documented proof of effective vessel cleaning for compliance and quality assurance. |
Optimal Process Optimization | Enables fine-tuning of CIP processes, saving time and resources. |
Enhanced Quality Assurance | Elevates quality control measures by ensuring impeccable cleanliness standards. |
Regulatory Compliance | Provides assurance of meeting regulatory cleanliness standards. |
Efficient Resource Utilization | Prevents unnecessary re-cleaning and enhances overall process efficiency. |
Visual Representation of Cleaning Efficacy | Offers clear visual verification through fluorescence under UV illumination. |
Cross-industry Applicability | Beneficial across industries with complex vessel configurations. |
Conclusion
Riboflavin testing emerges as a powerful tool in ensuring the thoroughness of Clean in Place processes. By shedding light on areas that traditional cleaning methods might miss, it enhances the quality, safety, and efficiency of industrial processes. The integration of this technique into quality control procedures serves as a testament to the relentless pursuit of cleanliness and excellence across industries.
Frequently Asked Questions:
What is Riboflavin Testing in the context of Clean in Place (CIP) and cleaning validation?
Answer: Riboflavin Testing is a technique used to assess the thoroughness and effectiveness of cleaning processes, particularly in industrial vessels during CIP procedures. It involves applying a fluorescent dye solution, often containing riboflavin, to the interior surfaces of the vessel. The vessel is then subjected to a CIP cycle. The presence of the dye allows for visual confirmation of spray coverage and cleaning effectiveness under UV illumination.
How does Riboflavin Testing contribute to cleaning validation?
Answer: Riboflavin Testing is a crucial step in cleaning validation as it provides a tangible and visual means to confirm that the CIP process is achieving the desired level of cleanliness. It helps identify any areas with incomplete spray coverage or “shadowed” regions that might not receive adequate cleaning. This information is critical for meeting regulatory requirements and ensuring product quality by minimizing the risk of cross-contamination or product carryover.
What are the benefits of using Riboflavin Testing in cleaning validation?
Answer: Riboflavin Testing offers several benefits, including:
- Visual Confirmation: It provides a clear visual representation of areas that have been effectively cleaned (fluorescent) and those that need improvement (non-fluorescent).
- Precision: It allows pinpointing of specific areas with inadequate spray coverage, helping to optimize cleaning procedures.
- Compliance: Riboflavin Testing provides documented evidence of the cleaning process, satisfying regulatory requirements for cleanliness validation.
- Process Optimization: The insights gained from Riboflavin Testing enable refining CIP parameters for better efficiency and effectiveness.
What parameters are critical for successful Riboflavin Testing during cleaning validation?
Answer: The following parameters are critical for successful Riboflavin Testing:
- Spray Coverage Uniformity: Ensuring that the fluorescent dye is uniformly distributed across all surfaces, including complex structures.
- Dye Concentration: Using the right concentration of riboflavin dye to achieve clear fluorescence under UV light.
- CIP Parameters: Controlling factors like spray pressure, flow rate, and contact time to mimic real-world cleaning conditions.
- UV Illumination: Using a suitable UV lamp to clearly differentiate between fluorescing and non-fluorescing areas.
Is Riboflavin Testing applicable across different industries?
Answer: Yes, Riboflavin Testing is versatile and applicable across various industries that rely on CIP processes, including pharmaceuticals, food and beverage, cosmetics, and more. Its effectiveness in revealing spray coverage makes it valuable for any industry where vessel cleanliness is crucial for product quality and safety.
How does Riboflavin Testing align with industry regulations and standards?
Answer: Many industry regulations and standards emphasize the importance of effective cleaning validation. Riboflavin Testing directly addresses these requirements by offering visual evidence of thorough cleaning, ensuring compliance with guidelines such as cGMP (Current Good Manufacturing Practice) and FDA regulations.
Can Riboflavin Testing be automated?
Answer: Yes, Riboflavin Testing can be automated to a certain extent. Automated systems can be designed to apply the dye solution, run the CIP cycle, and even capture images of the fluorescent patterns. Automation streamlines the process, reduces human errors, and allows for consistent and reliable results.
How frequently should Riboflavin Testing be conducted during cleaning validation?
Answer: The frequency of Riboflavin Testing depends on factors like the criticality of the vessel’s use, the complexity of its design, and regulatory requirements. Generally, it’s conducted during initial validation and subsequently during routine monitoring to ensure the ongoing effectiveness of the cleaning process.
Can Riboflavin Testing replace other cleaning validation methods?
Answer: Riboflavin Testing is a powerful visual technique that complements other cleaning validation methods but might not replace them entirely. It provides a direct way to visualize spray coverage but may not reveal chemical residue or other contaminants. A combination of methods, including swab testing and visual inspection, offers a comprehensive validation approach.
How is the riboflavin dye solution prepared for testing?
Answer: Riboflavin dye solution is typically prepared by mixing riboflavin powder with water to create a specific concentration, often around 100ppm. This solution is atomized or sprayed onto the interior surfaces of the vessel to simulate the application of the CIP solution.
What equipment is needed for Riboflavin Testing?
Answer: Equipment required for Riboflavin Testing includes riboflavin powder, a UV lamp for fluorescence observation, a spray device for even application of the dye solution, and a CIP system capable of mimicking actual cleaning conditions. Additionally, calibrated pressure gauges and flow meters ensure precise measurements.
Are there any safety considerations when conducting Riboflavin Testing?
Answer: Yes, safety precautions are essential during Riboflavin Testing. Personnel entering the vessel for dye application should follow confined space safety regulations. Also, since UV lamps emit UV light, proper eye protection is necessary to prevent UV exposure.
Can Riboflavin Testing help identify areas prone to contamination in vessels?
Answer: Yes, Riboflavin Testing can identify areas that are challenging to clean effectively due to intricate designs, such as agitators, nozzles, and corners. By highlighting these shadowed areas, Riboflavin Testing aids in optimizing cleaning procedures to minimize contamination risks.
How does Riboflavin Testing impact production downtime?
Answer: Riboflavin Test, when integrated into the cleaning validation process, might add a minor time component to the overall cleaning procedure due to the dye application and UV inspection steps. However, the insights gained can lead to more efficient cleaning processes, potentially offsetting any additional time.
Can Riboflavin Testing be performed in real-time during a production cycle?
Answer: While Riboflavin Test is not typically performed in real-time during production cycles due to the need for UV observation and dye application, the insights gained from testing can help optimize cleaning procedures for better real-time efficiency.
Are there limitations to Riboflavin Testing?
Answer: Riboflavin Test, while valuable, has limitations. It focuses on visualizing spray coverage but might not detect chemical or microbial residues. It also relies on human observation and interpretation. Complex vessel geometries can present challenges in achieving uniform dye distribution.
Can Riboflavin Testing be incorporated into automated CIP systems?
Answer: Yes, Riboflavin Test can be integrated into automated CIP systems. Automated devices can apply the dye solution and run the CIP cycle, while cameras capture UV images for subsequent analysis, providing a streamlined and consistent testing process.
What role does Riboflavin Testing play in continuous process improvement?
Answer: Riboflavin Test serves as a valuable tool in continuous process improvement. It highlights areas needing attention, aiding in refining CIP parameters, optimizing cleaning cycles, and ultimately enhancing overall production efficiency and product quality.