A sterile Manufacturing Vessel, a marvel of modern pharmaceutical science, emerges as a quintessential instrument, shrouded in the cloak of intricacy, striving relentlessly to achieve pharmaceutical perfection. In essence, this enigmatic vessel represents the apogee of pharmaceutical precision. Its multifaceted design confounds simplicity, ushering in an era of complexity that reverberates through the annals of pharmaceutical production.
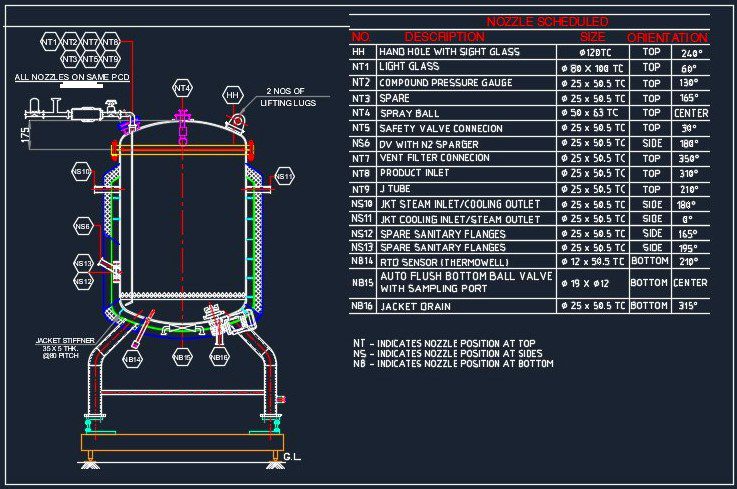
Components of the Manufacturing Vessel
The Compounding Vessel consists of a vertical cylindrical shell having a Dished End bottom & Openable type Top dish end with Nuts and bolts.
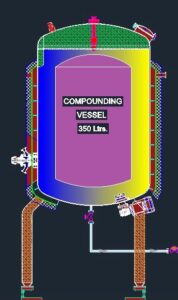
- The Top dish is provided with a hand hole for charging the material with Sight glass,
- Light glass,
- 5” Long 0.2 µ PTFE Vent Filter with Jacketed housing,
- Compound Gauge,
- Spray Ball for CIP,
- Safety Valve & Spare Nozzle.
- The tank bottom has with Pneumatic Actuated Diaphragm Type Flush Bottom Valve.
- Other nozzles are also provided on the top dish having TC end.
- The tank will also be provided with necessary accessories as mentioned below along with Baffle for breaking the vortex and interconnecting piping.
- The stirrer will be Bottom Entry Magnetic type SS 316L Quality suitable for a maximum viscosity of 1 cps. & with Variable Frequency Drive.
- The each leg of the vessel the Load Cell is mounted.
- The tank is reinforced with the Jacket having Cooling Water as a cooling media.
- The Jacket is provided with a Nozzle for Cooling the water Inlet and outlet along with a common nozzle for Air vent, Pressure Gauge, Safety Valve, and Jacket Drain.
- The Jacket is insulated with insulation and cladding is welded type of SS 304 Quality.
- The tank is having 3 Nos. of SS 304 round legs and mounted on Skid.
- All the contact parts are made out of SS 316L and non–contact parts are made out of SS 304 material.
- The design of each and every part are carried out considering the safety, required output, optimum utility, energy saving and to produce the Pharma Quality Vessel.
- The different Utilities are controlled through the control panel as per the requirement.
- The Vessel is internally ELECTROPOLISHED (Ra < 0.4) & externally MATT (Ra < 0.9) finished.
Particulars | Details |
Make | |
Model No. | ———— |
Working Capacity | Ltrs |
Gross Capacity | Ltrs |
Tank Dimension | MM X MM X MM |
Operation Type | Control Panel: Semi-Automatic PLC Based with manual Backup |
Mounting | Skid mounted |
MOC | Contact parts made out of SS 316L Quality and Non-Contact parts made out of SS 304 Quality. |
Finish | Internally Electro polished (Ra ≤ 0.4m) & Externally Matt (Ra ≤ 0.9m) finished. |
Piping | Orbital Welded for All Interconnecting Piping & Argon Welding for Non-Contact Parts. |
Design Aspect From Cleaning Point of View | Minimum sharp corners, minimum crevices & ground finished welds joints. |
Technical specification of the sterile manufacturing or compounding vessel:
Specification | Description |
---|---|
Vessel Material | Typically stainless steel or pharmaceutical-grade materials |
Capacity | Variable, ranging from small-scale to industrial volumes |
Mixing Mechanism | Proprietary agitators, blades, or impellers for precise mixing |
Heating/Cooling | Integrated heating and cooling systems for temperature control |
Pressure Rating | Designed for specific pressure requirements, often adjustable |
Sterilization Method | Steam-in-place (SIP) or autoclave for vessel sterilization |
Control System | Advanced PLC-based control system for precise process control |
Cleanroom Compatibility | Designed for integration into ISO-classified cleanrooms |
Material Inlets/Outlets | Multiple ports for adding ingredients and extracting product |
Safety Features | Pressure relief valves, emergency stop systems, and safety interlocks |
Documentation | Comprehensive documentation for regulatory compliance |
Validation | Validation protocols to ensure process consistency |
Compliance | Designed to meet cGMP (current Good Manufacturing Practices) standards |
Cleaning and Maintenance | Easy-to-clean design with access for thorough maintenance |
Design Parameters of Manufacturing Vessel:
DESCRIPTION | SHELL and JACKET |
Design Code | ASME SEC VIII DIV 1 |
Design pressure Kg/Cm² (g) | -1 to 4 |
Design Temperature Deg C | 130 |
Joint Efficiency % Shell/ Dish end | 0.85/1.0 |
Corrosion Allowance | Nil |
Operating Parameters of Manufacturing Vessel:
DESCRIPTION | SHELL | JACKET |
Operating Pressure Kg/Cm² | -1 to 3 | -1 to 3 |
Operating Temperature Deg C | 0 to 125 | 135 |
Vacuum | Full | Nil |
HYDRO TEST PARAMETERS
DESCRIPTION | SHELL | JACKET |
Hydro test pressure Kg/Cm² | 4 | 5 |
Material of Construction of Manufacturing Vessel:
PARTICULARS | DETAILS |
Main Shell | 4 mm Thk. SS 316L |
Top Dish | 4 mm Thk. SS 316L |
Bottom Dish | 4 mm Thk. SS 316L |
Stationary Baffle | 6 mm Thk. SS 316L |
Top Closing Flanges | 14 mm Thk. SS 316L |
Jacket stiffness | 35 x 5 mm Flat Spiral, SS 304 |
Jacket | 3 mm Thk. SS 304 |
Jacket Bottom | 3 mm Thk. SS 304 |
Insulation | 50 mm Thk. Resin Bonded Glass wool. Density -50 KG/M3 |
Cladding Shell/ Bottom | 1.6 mm, SS 304 |
Impeller of Magnetic Stirrer | SS 316L |
Supporting Legs | 3 Nos. SS 304 |
Skid | SS 304 |
Skid Wheel | P.U Dia. 4” x 2” W (3 Nos. Swiveling) |
Piping and Nozzles | SS 316L Electro polished & Orbital Welded |
Gaskets | Viton, Silicon & Teflon |
Control Panel | 1.6 mm, SS 304 |
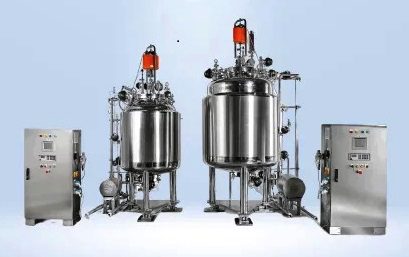
Utilities required to run the Manufacturing Vessels:
Utilities | Parameter’s |
Purified Water | Quality: Conductivity NMT 1.3 µs/cm |
Line Size: 25 mm OD | |
Pressure: @ 2-3 Kg/cm2 | |
WFI | Quality: Conductivity NMT 1.3 µs/cm min at 80 to 90 0C |
Line Size: 25 mm OD | |
Pressure: @ 2-3 Kg/cm2 | |
Soft Water | Quality: |
Line Size: 25 mm OD | |
Pressure: @ 1.5-2 Kg/cm2 | |
Pure Steam | Quality: Dry, Saturated, confirming EN285 pure steam tests (Free from oil, vapor and any other Impurities) |
Pressure: 2.5 -3 Kg/Cm2 | |
Line Size: 25 mm OD | |
Compressed Air | Quality: Moisture free, Filtered and Lubricated. |
Pressure: @ minimum 4-5 Kg/cm2.at FRL Inlet | |
Line Size: ½ ” BSP | |
Drain | 4” System Drain |
Electrical supply | 3 PH, 380 V (+ – 10 %), AC, 50 (+ – 3 %), Cy/Sec, max . kW |
The Manufacturing Vessel or tank will be provided with the following Process Operations:
- CIP Process
- SIP Process
- Heating, Cooling, Stirring and Transfer as per requirement through HMI touch switches individually
- Pressure Test by observing the Compound Gauge.
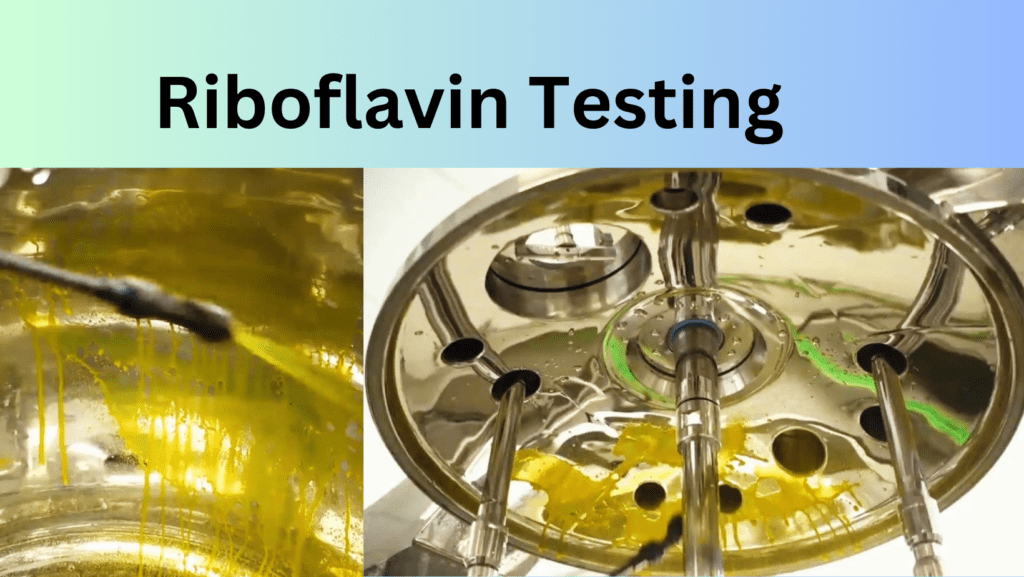
List of SAFETY & Interlocks of Manufacturing Vessel:
Condition | Remark |
Set temperature reached during SIP | Auto Diaphragm Valve will close |
Set temperature reached during Jacket Heating | Steam Inlet Valve will close. |
Set temperature reached during Cooling | Cooling Inlet and Outlet valve will close |
Set SIP Time elapsed | Auto Diaphragm Valve will stop and after a delay time Nitrogen flushing will open |
Set conductivity is reached during CIP. | WFI inlet valve will close with an alarm |
When the liquid level goes higher than the level sensor | Magnetic Stirrer will function otherwise will not operate |
Load in Tank Below Set Parameters (For Magnetic Mixer) | Magnetic Mixer will be Switched Off |
Power Failure in Filtration Tank | Process Will Stop |
Emergency OFF | Process Will Stop |
List of Documents of Manufacturing Vessel:
- URS
- DQ
- Factory Acceptance Test Protocol
- SAT
- As built G.A., P& I Diagram
- Hydro test certificate
- Trial Reports
- Certificates for Bought out components
- Calibration certificates for critical instruments
- Other drawings
- IQ, OQ Protocols and operation instruction manual
Frequently Asked Questions:
What is the primary function of a sterile manufacturing vessel?
Answer: The primary function of a sterile manufacturing vessel is to facilitate the precise formulation, mixing, blending, and drying of pharmaceutical and biotechnological products under aseptic conditions.
What materials are commonly used for constructing sterile manufacturing vessels?
Answer: Sterile manufacturing vessels are typically constructed using materials like stainless steel or other pharmaceutical-grade alloys that are resistant to corrosion and maintain sterility.
How is sterility maintained within a sterile manufacturing vessel during operations?
Answer: Sterility is maintained through a combination of design features, aseptic protocols, and sterilization methods, such as steam-in-place (SIP) or autoclaving, to ensure a sterile environment.
What types of mixing mechanisms are employed in sterile manufacturing vessels?
Answer: Sterile manufacturing vessels often employ specialized mixing mechanisms like agitators, blades, or impellers to ensure precise and homogenous mixing of pharmaceutical formulations.
How are temperature variations controlled within a sterile manufacturing vessel?
Answer: Temperature control is achieved through integrated heating and cooling systems, allowing for precise regulation of temperature during the manufacturing process.
What safety features are typically included in sterile manufacturing vessels?
Answer: Sterile manufacturing vessels are equipped with safety features such as pressure relief valves, emergency stop systems, and safety interlocks to ensure the safety of personnel and prevent equipment damage.
What is the purpose of the control system in a sterile manufacturing vessel?
Answer: The control system, often based on PLC (Programmable Logic Controller) technology, is used for precise process control, monitoring, and automation of various vessel operations.
How does a sterile manufacturing vessel integrate with cleanroom environments?
Answer: Sterile manufacturing vessels are designed for compatibility with controlled cleanroom settings and can be seamlessly integrated into ISO-classified cleanrooms to maintain a sterile production environment.
What regulatory standards must sterile manufacturing vessels adhere to in the pharmaceutical industry?
Answer: Sterile manufacturing vessels must adhere to pharmaceutical quality standards, including cGMP (current Good Manufacturing Practices) and industry-specific regulatory guidelines.
What is the typical documentation required for sterile manufacturing vessels?
Answer: Comprehensive documentation, including validation protocols, operation manuals, and maintenance records, is essential to demonstrate compliance with regulatory requirements and ensure process consistency.