Flanges, the unsung heroes of industrial infrastructure, play a pivotal role in connecting piping systems with utmost precision and reliability. These unassuming yet crucial devices come in a multitude of forms, each possessing unique characteristics and serving specific purposes. To navigate the intricate landscape of fluid transportation and containment, it is imperative to delve into the diverse world of flanges, understand their complexities, and explore their multifaceted applications.
Importance of flanges
The importance of flanges in various industries and applications cannot be overstated. Here are some key reasons why flanges are crucial:
- Secure Connections:
- Flanges provide a secure and reliable means of connecting pipes, valves, and equipment in a piping system. They create a strong joint that can withstand the pressure, temperature, and fluid flow within the system.
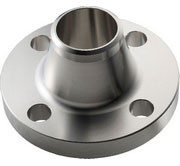
- Leak Prevention:
- Flanges, when properly installed with gaskets, ensure a tight seal, preventing leakage of fluids or gases. This is vital in maintaining the integrity of the system, minimizing the risk of environmental contamination, and ensuring the safety of personnel.
- Easy Installation and Maintenance:
- Flanges facilitate ease of installation and disassembly, making it simpler to connect or disconnect components in a piping system. This is particularly important for maintenance, repairs, or modifications, saving time and effort.
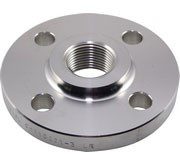
- Flexibility and Adaptability:
- Flanges allow for flexibility and adaptability in piping systems. They enable the connection of pipes with different sizes, materials, or types, accommodating changes in the system layout or the addition of new components.
- Alignment and Support:
- Flanges help align and support pipes, valves, and equipment, ensuring proper positioning and structural stability. They help distribute loads and stresses evenly, reducing the risk of damage or failure.
- Compatibility and Standardization:
- Flanges follow industry standards and specifications, ensuring the compatibility and interchangeability of components across different manufacturers and systems. This standardization simplifies procurement, maintenance, and replacement processes.
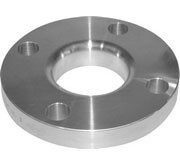
- Pressure and Temperature Management:
- Flanges are designed to withstand high pressures, extreme temperatures, and aggressive environments. They contribute to the overall integrity and safety of the system by containing and controlling the flow of fluids within specified parameters.
- Versatility and Diverse Applications:
- Flanges find application in a wide range of industries, including oil and gas, petrochemical, power generation, water treatment, pharmaceuticals, and more. They serve various purposes, from connecting pipelines and equipment to facilitating measurement and control.
Types of Flanges and Their Uses
Flange Type | Uses |
---|---|
Weld Neck Flange | High-pressure applications, stress, and corrosion resistance. |
Slip-On Flange | Cost-effective, frequent disassembly and reassembly. |
Blind Flange | Closure of pipe ends, preventing fluid escape and contamination. |
Threaded Flange | Easy assembly and disassembly, suitable for threaded connections. |
Socket Weld Flange | Measurement of fluid flow, and installation of orifice plates. |
Lap Joint Flange | Easy alignment, ideal for non-standard or rotating connections. |
Orifice Flange | Temporary or permanent closure of pipe ends, for maintenance purposes. |
Spectacle Blind Flange | Temporary or permanent closure of pipe ends, maintenance purposes. |
Expander Flange | Expansion and contraction of pipelines, thermal movements. |
Reducing Flange | Robust weld penetration, and leakage resistance. |
Tongue and Groove Flange | Alignment and connection of pipes with grooved ends. |
Types of flanges in piping
In piping systems, various types of flanges are employed to ensure reliable connections and facilitate the seamless flow of fluids. Here are some commonly used types of flanges in piping:
- Weld Neck Flange (WNF): This type of flange has a long, tapered hub that provides reinforcement and enhances the strength of the joint. It is well-suited for high-pressure applications and situations that involve extreme temperatures or substantial loads.
- Slip-On Flange (SOF): The Slip-On Flange slides over the pipe and is then welded in place. It offers ease of installation and is ideal for applications that require frequent disassembly and reassembly.
- Socket Weld Flange (SWF): A Socket Weld Flange features a socket-like structure where the pipe is inserted, allowing for easy and efficient welding. It provides a strong and leak-resistant connection.
- Threaded Flange (THF): This flange type has internal threading, allowing it to be screwed onto the pipe. It is commonly used in low-pressure applications and offers convenience in assembly and disassembly.
- Blind Flange (BLF): The Blind Flange is used to close off the end of a pipe. It lacks a center opening, making it ideal for applications where isolation or closure of a pipeline is required.
- Lap Joint Flange (LJF): A Lap Joint Flange consists of two components: the backing flange and a separate stub-end. It allows for easy alignment and rotation of the stub-end, making it suitable for systems that require frequent disassembly.
- Threaded/Screwed Flange: This type of flange has external threading, which allows it to be screwed into a matching threaded pipe or fitting. It provides a secure and reliable connection.
- Orifice Flange: An Orifice Flange is specifically designed for the installation of orifice plates, which are used to measure fluid flow rates. It has holes or pressure taps for accurate measurement and control.
- Spectacle Blind Flange: A Spectacle Blind Flange consists of two metal discs connected by a central section. It is used for temporary or permanent isolation of a pipe, allowing maintenance or inspection work to be carried out.
- Reducing Flange: A Reducing Flange is used to connect pipes of different diameters. It has a larger flange face on one side and a smaller one on the other, enabling a smooth transition between pipes with varying sizes.
Application of flanges
Industry/Sector | Flange Application |
---|---|
Oil and Gas | Pipeline connections, refinery equipment, wellheads, valves |
Petrochemical | Chemical processing units, storage tanks, reactors |
Power Generation | Turbines, boilers, heat exchangers, condensers |
Water and Wastewater | Water treatment plants, pump stations, sewage systems |
Pharmaceutical | Process equipment, sterile connections |
Food and Beverage | Processing equipment, sanitary connections |
HVAC | Air conditioning systems, ventilation ducts, heating units |
Shipbuilding | Marine piping, ship propulsion systems, ballast systems |
Construction | Plumbing, heating systems, fire protection |
Automotive | Exhaust systems, engine components |
Aerospace | Fuel systems, hydraulic and pneumatic systems |
Mining | Slurry pipelines, mineral processing equipment |
Chemical | Storage tanks, reactors, chemical transfer lines |
Pulp and Paper | Paper machines, pulp digesters, wastewater treatment systems |
Pharmaceutical | Process equipment, sterile connections |
Food and Beverage | Processing equipment, sanitary connections |
Frequently Asked Questions
What is the purpose of a flange?
Answer: Flanges are used to connect pipes, valves, and other equipment in a piping system, providing a secure and leak-tight joint.
What are the common materials used to manufacture flanges?
Answer: Flanges are typically made from materials such as carbon steel, stainless steel, alloy steel, or non-ferrous metals like bronze or brass, depending on the application and required properties.
How are flange dimensions specified?
Answer: Flange dimensions are specified using standards such as ASME B16.5 or DIN, which provide guidelines for flange sizes, bolt hole patterns, and pressure ratings.
What is the difference between a raised face (RF) and a flat face (FF) flange?
Answer: A raised face flange has a raised surface around the sealing area, while a flat face flange has a smooth, flat sealing surface. The choice between RF and FF flanges depends on the application and the type of gasket used.
What is a flange gasket, and why is it important?
Answer: A flange gasket is placed between two flange faces to create a reliable seal and prevent leakage. It helps to compensate for surface irregularities and provides a barrier against fluid or gas escape.
What is flange rating, and how is it determined?
Answer: Flange rating indicates the pressure-temperature capacity of a flange. It is determined based on factors such as material strength, flange design, and industry standards. Common ratings include Class, PN, or pressure/temperature tables.
What are the main types of flange connections?
Answer: The main types of flange connections include weld neck flanges, slip-on flanges, socket weld flanges, threaded flanges, blind flanges, and lap joint flanges, each suited for different applications and installation requirements.
What is flange face finish, and why is it important?
Answer: Flange face finish refers to the smoothness and flatness of the flange sealing surface. A proper face finish is crucial to ensure effective sealing, gasket compatibility, and minimize the risk of leaks.
How are flanges joined together in a piping system?
Answer: Flanges are joined together using bolts and nuts, creating a strong and reliable connection. The number and size of bolts depend on the flange size, pressure rating, and application requirements.
What considerations should be made when selecting a flange for a specific application?
Answer: When selecting a flange, factors such as the system pressure and temperature, fluid type, corrosion resistance, flange material, gasket material, and industry standards should be taken into account to ensure a safe and efficient installation.