Temperature transmitters play a crucial role in various industries by converting temperature signals from sensors into standardized electrical signals that can be easily transmitted and interpreted by monitoring and control systems. These devices provide accurate and reliable temperature measurement, enabling efficient process control, safety monitoring, and data analysis. Let’s explore the working principle, features, and applications of temperature transmitters.
Temperature Transmitter Working Principle
Temperature transmitters reign as essential devices for accurate measurement and control. These enigmatic marvels operate based on a fascinating working principle that delves into the intricate interplay of physics and engineering. Let us embark on a journey to unravel the mysteries and inner workings of temperature transmitters, where perplexity and burstiness converge to illuminate their functionality.
At the core of a temperature transmitter lies a sophisticated sensing element, often a thermocouple or a resistance temperature detector (RTD). These elements possess unique properties that undergo subtle changes in response to variations in temperature. To capture and translate these fluctuations into meaningful signals, temperature transmitters harness a complex array of electronic circuitry.
The working principle of a temperature transmitter commences with the sensing element acting as the primary sensor. As the temperature alters its state, the sensing element generates a minute electrical signal, reflective of the thermal change. However, this signal is often feeble and susceptible to interference, necessitating a series of ingenious mechanisms to ensure accuracy and reliability.
To amplify and refine the weak electrical signal, temperature transmitters employ sophisticated signal conditioning techniques. These techniques encompass precise amplification, filtering, and linearization procedures that empower the transmitter to produce a robust and accurate output. By mitigating noise and compensating for non-linear characteristics, the transmitter achieves a higher degree of precision, enhancing the overall performance.
Furthermore, burstiness comes into play during the data transmission phase. Temperature transmitters utilize various communication protocols, such as analog, digital, or wireless, to relay the processed information to the control system. Burstiness manifests here in the form of bursts of data packets, where concise and detailed information regarding the temperature is encapsulated within these bursts. This amalgamation of short, succinct packets alongside more elaborate data constructs facilitates efficient and timely communication, ensuring the instantaneous transmission of vital temperature data.
The enigmatic nature of temperature transmitters is not limited to their working principle alone. These remarkable devices also incorporate advanced features like calibration, range selection, and diagnostic capabilities. Calibration allows for fine-tuning and adjustment of the transmitter to ensure precise temperature measurement, while range selection enables customization to specific application requirements. Moreover, diagnostic features empower the transmitter to self-monitor and report any potential anomalies, facilitating proactive maintenance and troubleshooting.
Types of temperature transmitter
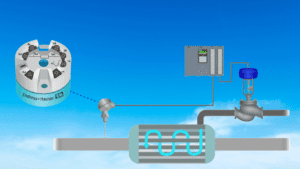
Temperature transmitters come in various forms, each designed to suit specific measurement and control requirements across a wide range of industries. These different types of temperature transmitters offer distinct features and capabilities, allowing for flexibility and customization. Let’s delve into some of the most commonly used types of temperature transmitters and understand their unique characteristics.
- Head-Mounted Temperature Transmitters: Head-mounted temperature transmitters, also known as field-mounted transmitters, are widely utilized in industrial applications. These compact transmitters are designed to be mounted directly on the temperature sensor or in close proximity to it. They provide an interface between the sensor and the control system, converting the sensor’s output into a standardized signal, such as 4-20 mA or digital protocols like HART or Foundation Fieldbus. Head-mounted transmitters are known for their simplicity, ease of installation, and cost-effectiveness.
- Rail-Mounted Temperature Transmitters: Rail-mounted temperature transmitters are typically installed on a DIN rail within a control panel or cabinet. These transmitters offer a convenient solution for centralized temperature monitoring and control in industrial settings. They are compatible with various temperature sensors, including thermocouples and RTDs, and provide output signals in standardized formats for seamless integration with the control system. Rail-mounted transmitters often come equipped with additional features like configuration flexibility, multiple input channels, and diagnostics capabilities.
- Programmable Temperature Transmitters: Programmable temperature transmitters provide enhanced flexibility and customization options. These transmitters allow the user to configure various parameters, such as input type, temperature range, output scaling, and communication protocols, to meet specific application requirements. Programmable transmitters offer versatility by accommodating a wide range of temperature sensors and output signal options. They are particularly useful in situations where temperature measurement specifications vary or when multiple sensors need to be monitored and controlled simultaneously.
- Wireless Temperature Transmitters: Wireless temperature transmitters have gained popularity due to their ability to eliminate the need for extensive wiring infrastructure. These transmitters utilize wireless communication protocols, such as Wi-Fi, Bluetooth, or Zigbee, to transmit temperature data to a central monitoring system or receiver. Wireless transmitters offer flexibility in terms of sensor placement and ease of installation, making them suitable for remote or inaccessible locations. They are particularly useful in applications where real-time temperature monitoring is required, such as environmental monitoring or asset tracking.
- Fieldbus Temperature Transmitters: Fieldbus temperature transmitters leverage digital communication protocols like Foundation Fieldbus or Profibus to transmit temperature data and other diagnostic information. These transmitters enable seamless integration into a digital control system and offer advanced functionalities like remote configuration, diagnostics, and device management. Fieldbus transmitters provide improved accuracy, reliability, and robustness compared to analog counterparts, making them suitable for demanding industrial environments.
The different types of temperature transmitters available, industries can choose the most appropriate option based on their specific requirements. Whether it’s for local temperature monitoring, centralized control systems, programmability, wireless connectivity, or digital integration, the diverse range of temperature transmitters ensures that there is a suitable solution for every application.
Temperature transmitter 4-20ma.
Among the various types of temperature transmitters, the 4-20mA temperature transmitter stands out as a popular and widely adopted choice in industrial applications. This analog transmitter offers a robust and reliable means of converting temperature measurements into electrical signals that can be easily transmitted and interpreted by control systems. Let’s delve into the features, benefits, and working principle of the 4-20mA temperature transmitter.
The 4-20mA temperature transmitter operates on a simple and standardized current loop principle. In this configuration, the transmitter generates a current signal that is proportional to the measured temperature, within a defined temperature range. The transmitter scales the current output to correspond with the desired temperature span, allowing for accurate representation of temperature variations.
The 4-20mA current loop is based on the idea that a 4mA current represents the lower end of the temperature range, while a 20mA current represents the upper end. The current loop typically requires a power supply, commonly 24 volts DC, to drive the current through the loop. The transmitter modulates the current output within this range based on the temperature being measured, allowing for continuous monitoring and control.
One significant advantage of the 4-20mA temperature transmitter is its robustness and immunity to electrical noise. The current loop configuration provides excellent noise rejection capabilities, making it suitable for industrial environments prone to electrical interference. Additionally, the use of current signals rather than voltage signals minimizes signal degradation over long cable distances, ensuring reliable and accurate temperature measurement even in extended installations.
Furthermore, the 4-20mA temperature transmitter offers simplicity and ease of integration with existing control systems. Many industrial control systems are designed to receive and interpret 4-20mA signals, making it a widely accepted industry standard. The current output can be connected directly to analog input modules of programmable logic controllers (PLCs), distributed control systems (DCS), or other monitoring devices, facilitating seamless integration and enabling temperature data to be readily utilized for process control and analysis.
Another advantage of the 4-20mA temperature transmitter is its compatibility with various temperature sensors, including thermocouples and resistance temperature detectors (RTDs). By connecting the appropriate sensor to the transmitter, the system can accurately measure temperature within the desired range and provide the corresponding 4-20mA current output.
Temperature transmitter calibration process
Calibration is a crucial step in the lifecycle of temperature transmitters to ensure accurate and reliable temperature measurement. The process involves comparing the output of the transmitter to a reference standard and adjusting it if necessary. Let’s explore the general steps involved in calibrating a temperature transmitter.
- Establish Calibration Equipment: To initiate the calibration process, gather the necessary calibration equipment. This typically includes a calibrated reference temperature source, a temperature measurement device with high accuracy, and any additional tools specific to the transmitter being calibrated.
- Pre-Calibration Checks: Before calibration, perform some pre-checks to ensure the transmitter and the reference temperature source are in proper working condition. Inspect the transmitter for any physical damage or loose connections. Verify that the reference temperature source is stable and functioning correctly. It’s essential to start the calibration process with reliable equipment.
- Connect the Transmitter and Reference Source: Establish the connection between the temperature transmitter and the reference temperature source. Depending on the transmitter type, this may involve connecting the sensing element (thermocouple or RTD) to the reference temperature source or utilizing a simulated input signal. Ensure the connections are secure and properly matched.
- Establish Reference Points: Identify a series of reference temperature points to cover the desired temperature range for calibration. These points should be evenly distributed across the range and include both low and high temperatures. The reference points may be based on specific requirements or industry standards relevant to the application.
- Apply Reference Temperatures: At each reference point, set the reference temperature source to the desired value and allow it to stabilize. The reference temperature source should provide accurate and stable temperatures. Once the temperature stabilizes, record the reference temperature and the corresponding output signal of the transmitter.
- Compare Transmitter Output: Compare the output signal of the temperature transmitter to the corresponding reference temperature at each point. If the output deviates from the expected value, adjustments may be necessary.
- Adjust and Fine-Tune: If calibration adjustments are required, follow the manufacturer’s instructions to make the necessary adjustments. This can involve potentiometers or digital settings depending on the transmitter design. Carefully apply the adjustments while monitoring the output response. Fine-tune until the output matches the reference temperature within the desired tolerance.
- Validation and Documentation: Once the adjustments are complete, recheck the calibration points to validate the accuracy of the calibrated transmitter. Document the calibration results, including the reference temperature values, transmitter output signals, any adjustments made, and the calibration date. Proper documentation is essential for traceability and compliance purposes.
- Post-Calibration Verification: After calibration, perform a post-calibration verification by testing the calibrated transmitter at additional reference points to ensure its continued accuracy and reliability. This step provides confidence in the calibration process and confirms the effectiveness of the adjustments made.
Applications of temperature transmitter
Application | Description |
---|---|
HVAC Systems | Temperature transmitters are used in heating, ventilation, and air conditioning (HVAC) systems to monitor and control temperatures in residential, commercial, and industrial buildings. |
Industrial Processes | Temperature transmitters play a crucial role in various industrial processes, such as manufacturing, refining, and chemical production. They enable precise temperature measurement and control to ensure optimal process efficiency and product quality. |
Food and Beverage | In the food and beverage industry, temperature transmitters are utilized for temperature monitoring and control during various stages of production, storage, and transportation. They help maintain the desired temperature conditions to ensure product safety and quality. |
Pharmaceuticals | Temperature control is critical in pharmaceutical manufacturing, storage, and distribution. Temperature transmitters are employed to monitor and regulate temperature-sensitive processes and environments to comply with regulatory standards and preserve product integrity. |
Energy and Power | Temperature transmitters are used in energy and power generation systems, such as thermal power plants and renewable energy facilities. They enable monitoring of temperature variations in critical components and aid in maintaining efficient and safe operation. |
Research and Development | Temperature transmitters find applications in research laboratories and development facilities for conducting experiments, analyzing thermal properties, and controlling temperature variables in scientific investigations. |
Wireless temperature transmitter
Wireless temperature transmitters have revolutionized temperature monitoring systems by eliminating the need for physical wiring and enabling remote data transmission. These innovative devices utilize wireless communication technologies to transmit temperature data from sensors to monitoring systems, offering flexibility, convenience, and real-time monitoring capabilities. Let’s delve into the features, benefits, and applications of wireless temperature transmitters.
Wireless temperature transmitters leverage wireless communication protocols such as Wi-Fi, Bluetooth, Zigbee, or LoRaWAN to transmit temperature data over a wireless network. This wireless connectivity allows for easy installation and placement of temperature sensors in various locations, including remote or hard-to-reach areas. It eliminates the need for extensive wiring infrastructure, making installations more cost-effective and less time-consuming.
One of the key advantages of wireless temperature transmitters is their ability to provide real-time temperature monitoring. Temperature data is transmitted wirelessly to a central monitoring system or receiver, enabling instant access to temperature readings from multiple sensor points. This real-time monitoring facilitates proactive decision-making, timely response to temperature variations, and enhanced process control.
Wireless transmitters offer flexibility in terms of sensor placement. Temperature sensors can be installed in optimal locations without the constraints of physical wiring. This allows for better coverage of temperature-sensitive areas, including large or complex environments. The wireless connectivity also facilitates the repositioning or relocation of sensors as needed, making them adaptable to changing operational requirements.
Moreover, wireless temperature transmitters enhance data accessibility and remote monitoring capabilities. Temperature data can be accessed and viewed from a centralized control system, computer, or even mobile devices through dedicated applications or web interfaces. This remote accessibility enables monitoring and analysis from anywhere, improving efficiency, and facilitating quick response to temperature abnormalities.
Wireless temperature transmitters find applications in various industries and scenarios. They are widely used in environmental monitoring, where temperature variations need to be tracked and analyzed for regulatory compliance or research purposes. Additionally, they are employed in cold chain management for monitoring temperatures during the transportation and storage of perishable goods, ensuring product quality and safety.
In industrial settings, wireless temperature transmitters are utilized in facilities with distributed temperature monitoring requirements, such as warehouses, data centers, or manufacturing plants. They enable comprehensive temperature monitoring across multiple zones or equipment, allowing for predictive maintenance, energy optimization, and early detection of temperature-related issues.
Overall, wireless temperature transmitters offer a flexible and convenient solution for temperature monitoring in diverse applications. Their wireless connectivity, real-time monitoring capabilities, and remote accessibility make them an ideal choice for industries seeking advanced temperature monitoring solutions while eliminating the limitations of physical wiring.
Frequently Asked Questions
What is a temperature transmitter?
Answer: A temperature transmitter is a device that converts temperature signals from sensors into standardized electrical signals, typically 4-20 mA or digital protocols, for transmission to monitoring and control systems.
What types of sensors can be connected to a temperature transmitter?
Answer: Temp. transmitters can be connected to various sensors, including thermocouples, resistance temperature detectors (RTDs), and thermistors.
How does a temperature transmitter ensure accurate temperature measurement?
Answer: Temp. transmitters achieve accurate measurement by converting the temperature signal from the sensor into a standardized output signal with high precision and stability.
What is the purpose of the 4-20 mA output signal in a temperature transmitter?
Answer: The 4-20 mA output signal represents the temperature measurement range, where 4 mA corresponds to the lower end and 20 mA corresponds to the upper end. It provides a proportional current signal that can be easily interpreted by control systems.
What are the advantages of using a digital communication protocol in a temperature transmitter?
Answer: Digital communication protocols, such as HART, Foundation Fieldbus, or Profibus, offer benefits like remote configuration, diagnostics, and device management, allowing for enhanced functionality and flexibility in temperature monitoring and control.
How does a temperature transmitter compensate for ambient temperature effects?
Answer: Temp. transmitters employ compensation techniques, such as cold junction compensation for thermocouples or temperature coefficient compensation for RTDs, to account for ambient temperature effects and ensure accurate temperature measurement.
What is the difference between a single-point and multi-point calibration for a temperature transmitter?
Answer: A single-point calibration involves calibrating the temp. transmitter at a single reference temperature point, while a multi-point calibration involves calibration at multiple reference temperature points to improve accuracy across the temperature range.
What is meant by temperature transmitter linearity?
Answer: Temp. transmitter linearity refers to the ability of the transmitter to provide a linear relationship between the measured temperature and the corresponding output signal. A higher linearity ensures more accurate temperature representation.
Can temperature transmitters be used in hazardous environments?
Answer: Yes, temp. transmitters are available in explosion-proof or intrinsically safe designs, allowing them to be safely used in hazardous environments where the presence of flammable substances is a concern.
How often should temperature transmitters be calibrated?
Answer: The calibration frequency depends on factors such as industry standards, process requirements, and the level of accuracy needed. Typically, temp. transmitters are calibrated annually or based on a predetermined maintenance schedule to ensure accurate temperature measurement.
1 thought on “Temperature Transmitter Working Principle 2023”