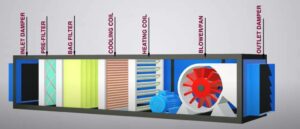
Air Handling Units (AHUs) are a critical component of HVAC systems in pharmaceutical facilities. AHUs play a crucial role in maintaining the required environmental conditions for pharmaceutical manufacturing, storage, and other related processes. They help control temperature, humidity, filtration, and ventilation to ensure the air quality meets specific standards for pharmaceutical production. AHUs are equipped with high-efficiency particulate air (HEPA) filters and often additional filters to remove contaminants. AHUs regulate temperature and humidity levels and provide controlled and sufficient fresh air intake and exhaust to prevent cross-contamination. Energy efficiency is a significant consideration, and AHUs are equipped with energy-efficient components, and typically integrated into a centralized building automation system for effective monitoring and control.
Working Principle of Air Handling Unit.
The working principle of an Air Handling Unit (AHU) involves several components that work together to regulate the temperature, humidity, and air quality of the indoor environment. Here are the primary components and their functions in the working principle of an AHU:
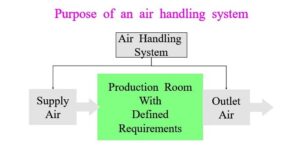
- Fan: The fan draws the air from the return ductwork into the AHU and pushes it through the heating or cooling coils, filters, and humidifiers or dehumidifiers.
- Heating and Cooling Coils: The heating or cooling coils are responsible for regulating the temperature of the air passing through the AHU. They work by transferring heat to or from the air as it passes over the coils, depending on whether heating or cooling is required.
- Filters: The filters remove contaminants from the air, such as dust, pollen, and other airborne particles, to ensure the air quality meets specific standards.
- Humidifiers or Dehumidifiers: Humidifiers add moisture to the air to increase humidity levels, while dehumidifiers remove moisture to reduce humidity levels.
- Mixing Chamber: The mixing chamber blends the return air with fresh outdoor air to create a mixed air supply that meets the required temperature, humidity, and ventilation standards.
- Air Distributor: The air distributor distributes the mixed air supply to the various areas of the building through the supply ductwork.
- Controls: The controls regulate the operation of the AHU components to maintain the desired indoor environment. The controls also monitor and respond to deviations from the required conditions, such as temperature or humidity levels.
Overall, the AHU working principle involves a combination of components working together to regulate the indoor environment’s temperature, humidity, and air quality while ensuring proper ventilation and energy efficiency.
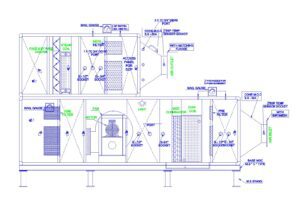
ahu full form
Air Handling Unit.
Air Handling Units (AHUs) are an essential component of HVAC (Heating, Ventilation, and Air Conditioning) systems in pharmaceutical facilities. They play a crucial role in maintaining the required environmental conditions for pharmaceutical manufacturing, storage, and other related processes. Here’s some information about AHUs in pharmaceutical HVAC systems:
- Purpose: AHUs are responsible for circulating and conditioning air within pharmaceutical facilities. They help control temperature, humidity, filtration, and ventilation to ensure the air quality meets specific standards for pharmaceutical production.
- Air Filtration: AHUs in pharmaceutical settings are equipped with high-efficiency particulate air (HEPA) filters and often additional filters to remove contaminants, such as bacteria, viruses, dust, and other airborne particles. These filters are designed to meet stringent pharmaceutical industry standards.
- Temperature and Humidity Control: AHUs regulate temperature and humidity levels within pharmaceutical spaces. Precise control of these parameters is crucial for maintaining the stability and quality of pharmaceutical products. AHUs can heat, cool, humidify, or dehumidify the air as required.
- Ventilation: Proper ventilation is essential in pharmaceutical facilities to ensure adequate air exchange and to remove potential contaminants. AHUs are designed to provide controlled and sufficient fresh air intake and exhaust, maintaining a positive pressure differential between different areas of the facility to prevent cross-contamination.
- Energy Efficiency: Energy efficiency is a significant consideration in pharmaceutical HVAC systems. AHUs are equipped with energy-efficient components, such as variable speed drives (VSDs) for fans and motors, to optimize energy consumption while maintaining the required air quality and environmental conditions.
- Monitoring and Control: AHUs are typically integrated into a centralized building automation system (BAS) for effective monitoring and control. The BAS allows operators to monitor air quality, temperature, humidity, pressure differentials, and other critical parameters. It also enables them to make adjustments and respond to any deviations or alarms promptly.
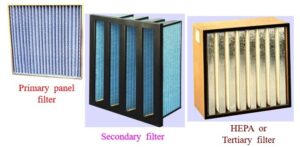
Major components of AHU.
Component | Function | Critical Technical Details |
---|---|---|
Fan | Circulates air within the AHU and throughout the facility. | Type: Centrifugal or Axial Fan, Capacity: Airflow volume in cubic meters per hour (m³/h), Speed Control: Variable Speed Drive (VSD) |
Heating/Cooling Coils | Control air temperature by transferring heat | Type: Finned Tube or Plate Coil Material: Copper, Aluminum, or Stainless Steel Capacity: Heat transfer rating in kilowatts (kW) Cooling capacity in TR |
Filters | Remove airborne contaminants and maintain air quality | Type: Pre-filters, Fine Filters, HEPA Filters, Efficiency: Filtration efficiency rating (e.g., MERV rating), Pressure Drop: Resistance to airflow. |
Humidifiers/Dehumidifiers | Control and adjust air humidity levels | Type: Steam, Spray, or Adiabatic Humidifiers Capacity: Moisture addition or removal rate in kilograms per hour (kg/h) Control: Humidistat or Controller |
Mixing Chamber | Mixes return and fresh air for desired conditions | Design: Plenum Chamber or Mixing Box Airflow Ratio: Proportion of return and fresh air |
Air Distributor | Distributes conditioned air to different areas | Ductwork: Supply ducts, Return ducts Dampers: Balancing dampers, Volume control dampers Registers: Diffusers, Grilles |
Controls | Monitor and regulate AHU operation | Sensors: Temperature, Humidity, Pressure sensors Controller: Programmable Logic Controller (PLC) Setpoints: Desired temperature, humidity, etc. |
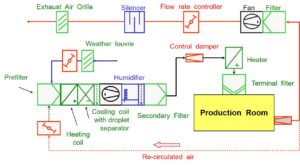
AHU cfm calculation formula
Designing Calculation while designing new AHU
- Airflow Calculation:
- Airflow (Q) = Volume Flow Rate (V) / Time (t)
- Q = 4000 CFM (given)
- Cooling Load Calculation:
- Cooling Load (CL) = Airflow (Q) × Cooling Load Factor (CLF)
- CLF is determined based on factors such as heat gain/loss through walls, windows, occupancy, lighting, and equipment.
- Heating Load Calculation:
- Heating Load (HL) = Airflow (Q) × Heating Load Factor (HLF)
- HLF is determined based on factors such as the desired indoor temperature and heat loss through walls, windows, and infiltration.
- Filter Sizing:
- Determine the required filter size and efficiency based on industry standards and air quality requirements.
- Coil Sizing:
- Cooling Coil: Cooling Capacity (CC) = Q × Sensible Heat Factor (SHF) × Temperature Difference (ΔT)
- Heating Coil: Heating Capacity (HC) = Q × Heating Load Factor (HLF) × Temperature Difference (ΔT)
- ΔT is the desired temperature difference between supply air and room conditions.
- Fan Selection:
- Select a fan based on the required airflow rate and static pressure. Fan curves and fan performance data can be used to determine the appropriate fan size and type.
- Duct Sizing:
- Size the supply and return ducts based on airflow requirements, velocity limits, and pressure drop calculations. Duct sizing equations, such as the Darcy-Weisbach equation, can be used to calculate the duct size.
- Humidification/Dehumidification Sizing:
- Determine the required humidification or dehumidification capacity based on the desired humidity levels, AHU airflow rate, and moisture load calculations.
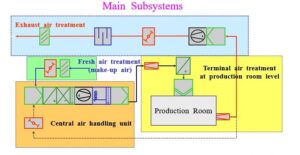
Types of AHUs
There are several types of Air Handling Units (AHUs) used in HVAC systems, each designed to meet specific requirements and applications. Here are some common types of AHUs:
- Single-Zone AHU: This type of AHU is designed to supply conditioned air to a single zone or space. It typically includes a fan, filters, heating, and cooling coils, and controls to regulate airflow and temperature.
- Multi-Zone AHU: Multi-zone AHUs are capable of supplying conditioned air to multiple zones or spaces simultaneously. They have separate ductwork and controls to provide individual temperature control for each zone.
- Constant Volume AHU: Constant Volume AHUs supply a fixed volume of air to the space throughout the operation. The fan speed and airflow remain constant regardless of the demand or load.
- Variable Air Volume (VAV) AHU: VAV AHUs adjust the airflow rate based on the cooling or heating demand of the space. The fan speed and airflow can vary to match the varying load requirements, providing energy savings and improved comfort.
- Makeup Air AHU: Makeup Air AHUs are specifically designed to supply fresh air to compensate for exhaust air or maintain positive pressure in the building. They often incorporate heat recovery systems to optimize energy efficiency.
- Heat Recovery AHU: Heat Recovery AHUs capture and transfer heat energy from the exhaust air to the incoming fresh air, reducing energy consumption by preheating or precooling the supply air.
- Cleanroom AHU: Cleanroom AHUs are designed for environments requiring high levels of air cleanliness, such as pharmaceutical facilities or semiconductor manufacturing. They incorporate high-efficiency filters, precise temperature, and humidity control, and stringent air change rates to maintain clean and controlled environments.
- Packaged AHU: Packaged AHUs are factory-assembled units that contain all necessary components, including fans, filters, coils, controls, and sometimes even pre-wired electrical connections. They are compact and suitable for applications with limited space.
- Rooftop AHU: Rooftop AHUs are specifically designed to be installed on rooftops, saving indoor space. They are weather-resistant and commonly used in commercial buildings.
- Modular AHU: Modular AHUs consist of multiple modules that can be combined or separated to meet specific airflow and capacity requirements. They offer flexibility in system design and future expansion.
Applications of AHU
Application | Description |
---|---|
Commercial Buildings | Air handling Sets are widely used in office buildings, shopping malls, hotels, and other commercial spaces for HVAC systems. |
Industrial Facilities | Air handling Sets play a crucial role in providing conditioned air for manufacturing plants, warehouses, and industrial spaces. |
Healthcare Facilities | Air handling Sets are essential in hospitals, clinics, and healthcare facilities to maintain clean air and control infection risks. |
Pharmaceutical Industry | Air handling Sets are critical in pharmaceutical facilities to control temperature, humidity, and air quality for production and storage. |
Data Centers | Air handling Sets provide cooling and ventilation to maintain optimal operating conditions for servers and IT equipment. |
Laboratories | Air handling Sets ensure proper air circulation and filtration to maintain controlled environments in research and testing labs. |
Food Processing Facilities | Air handling Sets are used in food processing plants to regulate temperature, humidity, and air quality for product safety. |
Educational Institutions | Air handling Sets are employed in schools, universities, and educational buildings to maintain comfortable and healthy indoor environments. |
Hospitality Industry | Air handling Sets are utilized in hotels, resorts, and hospitality establishments to provide conditioned air for guest comfort. |
Cleanrooms | Air handling Sets are crucial in cleanroom environments, such as semiconductor manufacturing, where strict air quality control is required. |
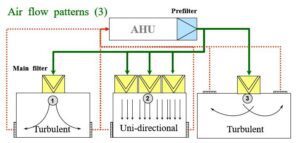
Advantages and disadvantages of AHU
Advantages | Disadvantages |
---|---|
Efficient Air Circulation: Air handling Set ensure proper air distribution | Initial Cost: Air handling Set can be expensive to purchase and install |
Temperature Control: Air handling Set regulate and maintain desired temperatures | Energy Consumption: Air handling Set can consume a significant amount of energy, especially if not properly optimized or maintained |
Humidity Control: Air handling Set help maintain optimal humidity levels | Space Requirements: Air handling Set require dedicated space for installation, which can be limited in some buildings |
Air Quality: Air handling Set filter and remove airborne contaminants | Maintenance: Air handling Set require regular maintenance to ensure optimal performance and prevent breakdowns |
Ventilation: Air handling Set provide fresh air intake and exhaust | Noise: Air handling Set can produce noise during operation, which may require additional soundproofing measures |
Centralized Control: Air handling Set can be integrated into a centralized building automation system for easy monitoring and control | Complexity: Air handling Set involve complex equipment and controls, requiring specialized knowledge for installation and operation |
Flexibility: Air handling Set can be customized to meet specific requirements | Dependency: If an Air handling Set fails, it can impact the entire HVAC system and disrupt the indoor environment |
Troubleshooting in Air Handling Units
Troubleshooting Air Handling Units involves identifying and resolving issues that may arise during operation. Here are some common troubleshooting steps for Air handling Sets:
- Insufficient Airflow:
- Check if the fan is running at the correct speed.
- Verify that dampers are fully open and not obstructed.
- Ensure filters are clean and not clogged.
- Check for any obstructions in the ductwork.
- Inadequate Heating/Cooling:
- Verify that the heating/cooling coils are clean and not blocked by debris.
- Check if the valves controlling the flow of hot/cold water to the coils are functioning properly.
- Ensure that the control system is set to the correct temperature and mode.
- High Energy Consumption:
- Inspect and clean the fan blades and motor to optimize airflow efficiency.
- Check for any air leaks in the ductwork and seal them.
- Verify that the control system is properly calibrated and set for energy-saving operation.
- Unusual Noise or Vibration:
- Inspect the fan assembly for loose or damaged components.
- Check for any loose or worn belts, pulleys, or bearings.
- Ensure that the fan blades are properly balanced.
- Lubricate moving parts as recommended by the manufacturer.
- Poor Air Quality:
- Check and replace filters if they are dirty or clogged.
- Inspect and clean the cooling coils to prevent microbial growth.
- Verify that the Air handling Set is maintaining the recommended humidity levels.
- Ensure that the outdoor air intake is not contaminated or obstructed.
- Control System Malfunction:
- Verify that all sensors and actuators are properly connected and functioning.
- Check the control settings and programming for accuracy.
- Calibrate sensors as necessary.
- Restart or reset the control system if needed.
- Electrical Issues:
- Check for tripped circuit breakers or blown fuses.
- Inspect wiring connections for any loose or damaged connections.
- Verify that all electrical components are receiving the correct voltage.
- Contact a qualified electrician for further assistance if needed.
- Water Leakage:
- Inspect the condensate drain pans and lines for blockages or leaks.
- Clean or replace clogged drain lines.
- Ensure that the drain pans are properly sloped for effective drainage.
It’s important to note that troubleshooting procedures may vary depending on the specific Air handling Set model and the nature of the issue. When encountering complex or persistent problems, it is recommended to consult with qualified HVAC technicians or professionals for accurate diagnosis and resolution.
Frequently Asked Questions:
What is the purpose of AHUs in pharmaceutical facilities?
Answer: Air handling Sets in pharmaceutical facilities are responsible for maintaining specific environmental conditions, including temperature, humidity, filtration, and ventilation, to ensure the air quality meets stringent standards for pharmaceutical production and storage.
What type of filters are typically used in AHUs for pharmaceutical applications?
Answer: HEPA (High-Efficiency Particulate Air) filters are commonly used in Air handling Sets for pharmaceutical applications. These filters are highly efficient at removing airborne particles, including bacteria, viruses, and other contaminants, ensuring clean air within the facility.
How are AHUs designed to prevent cross-contamination in pharmaceutical facilities?
Answer: Air handling Sets in pharmaceutical facilities are designed to maintain a positive pressure differential between different areas of the facility. This prevents the migration of contaminants from one area to another, minimizing the risk of cross-contamination.
How are AHUs controlled in pharmaceutical settings?
Answer: Air handling Sets in pharmaceutical facilities are typically integrated into a centralized Building Automation System (BAS) or a dedicated HVAC control system. These systems monitor and control various parameters such as temperature, humidity, airflow, and filter status, allowing operators to make adjustments and respond to deviations promptly.
What are the energy efficiency considerations for AHUs in pharmaceutical facilities?
Answer: Energy efficiency is a significant consideration for Air handling Sets in pharmaceutical facilities. They are equipped with energy-efficient components such as variable speed drives (VSDs) for fans and motors. Additionally, advanced control strategies and heat recovery systems can be implemented to optimize energy consumption.
How often should filters in AHUs be replaced in pharmaceutical facilities?
Answer: Filter replacement frequency depends on factors such as the type of filter, level of airborne contaminants, and facility-specific requirements. It is typically recommended to follow manufacturer guidelines and conduct regular filter maintenance and replacements to ensure optimal performance and air quality.
What are the considerations for noise control in AHUs for pharmaceutical applications?
Answer: Noise control is an important aspect of Air handling Set design in pharmaceutical facilities. This can be achieved through the use of sound attenuators, acoustic insulation, vibration isolation, and appropriate fan selection to minimize noise levels and ensure a comfortable working environment.
How can AHU performance be validated in pharmaceutical facilities?
Answer: Air handling Set performance can be validated through regular monitoring and testing. This may include measurements of temperature, humidity, airflow, pressure differentials, and air quality parameters. Regular maintenance, calibration, and compliance with industry regulations and standards are crucial for ensuring accurate and reliable Air handling Set performance.
What are the requirements for air change rates in pharmaceutical cleanrooms?
Answer: Air change rates in pharmaceutical cleanrooms are determined based on the classification of the cleanroom and the specific requirements of the process being conducted. They typically range from several air changes per hour (ACH) for higher classified cleanrooms to hundreds of ACH for critical processes.
How are AHUs in pharmaceutical facilities validated for regulatory compliance?
Answer: Air handling Sets in pharmaceutical facilities undergo validation processes to ensure compliance with regulatory standards. This involves performing qualification tests such as Installation Qualification (IQ), Operational Qualification (OQ), and Performance Qualification (PQ) to verify that the Air handling Sets meet the specified design criteria and performance requirements.
What are the considerations for energy recovery in AHUs for pharmaceutical facilities?
Answer: Energy recovery systems, such as heat exchangers, can be incorporated into Air handling Sets to recover heat or coolness from the exhaust air and transfer it to the supply air, improving energy efficiency. Considerations include selecting appropriate heat exchanger types, ensuring compatibility with cleanroom requirements, and proper maintenance to avoid cross-contamination.
How are AHUs designed to handle emergency situations or power failures in pharmaceutical facilities?
Answer: Air handling Sets in pharmaceutical facilities often incorporates emergency systems such as backup power supplies or uninterruptible power systems (UPS) to ensure continued operation during power failures. Additionally, Air handling Sets may have fail-safe mechanisms and alarm systems to detect and respond to critical issues, such as temperature or pressure deviations.
What are the considerations for AHU maintenance in pharmaceutical facilities?
Answer: Regular maintenance of Air handling Sets is crucial to ensure optimal performance and compliance with regulatory requirements. Maintenance tasks include filter replacements, coil cleaning, belt and motor inspections, lubrication, calibration of sensors and controls, and periodic performance testing. Maintenance schedules should be established based on equipment manufacturer recommendations and industry best practices.
How are AHUs designed to meet the requirements of containment facilities in the pharmaceutical industry?
Answer: Containment facilities, such as those handling potent or hazardous substances, require specialized Air handling Sets with robust filtration systems and pressure control measures. Air handling Set in containment facilities are designed to prevent the release of airborne contaminants, maintain negative pressure differentials, and provide adequate ventilation and filtration for worker safety.
Can AHUs be integrated with Building Management Systems (BMS) in pharmaceutical facilities?
Answer: Yes, It can be integrated with Building Management Systems (BMS) or other control systems used in pharmaceutical facilities. This allows centralized monitoring, control, and data logging of Air handling Set performance and coordination with other HVAC systems and equipment within the facility.
You may also read Water Quality Monitoring