“Failure Mode and Effects Analysis (FMEA) is a proactive risk assessment tool that identifies and mitigates potential failures in products and processes. FMEA helps organizations prioritize risks, develop action plans, and continuously improve their processes to enhance product quality and reliability, comply with regulations, and enhance customer satisfaction.”
Typical steps of the Failure Modes and Effects Analysis (FMEA) tool:
- Define the scope: Identify the process, product, or system to be analyzed and define the scope of the analysis.
- Assemble the team: Assemble a cross-functional team with members who have expertise in the process or product being analyzed.
- Identify the functions: Identity the key functions of the process, product, or system being analyzed.
- Identify the failure modes: Identify the potential failure modes for each function. A failure mode is a way in which a function can fail to meet its intended purpose.
- Determine the severity: Determine the severity of the effect of each failure mode on the process, product, or system. The severity is the degree of impact or harms the failure mode could have on the process, product, or system.
- Determine the occurrence: Determine the likelihood of each failure mode occurring. The occurrence is the frequency or probability of the failure mode happening.
- Determine the detection: Determine the likelihood of detecting each failure mode before it occurs or has a significant impact. Detection is identifying the failure mode before it becomes a problem.
- Calculate the risk priority number (RPN): Calculate the RPN for each failure mode by multiplying the severity, occurrence, and detection scores.
- Prioritize the actions: Prioritize the actions to be taken based on the RPN scores. Focus on the failure modes with the highest RPN scores and develop actions to prevent or mitigate them.
- Implement the actions: Implement the actions identified in the previous step and monitor their effectiveness.
- Review and update: Review and update the FMEA regularly to reflect changes in the process, product, or system being analyzed.
Overall, the FMEA tool is a systematic approach to identifying and mitigating potential failures or risks associated with a particular process or product. The FMEA process is a living document and should be updated regularly to ensure that the actions taken are effective and up-to-date.
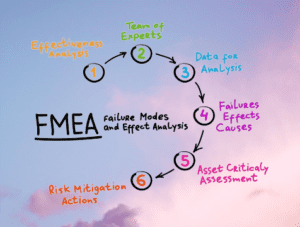
FMEA (Failure Mode and Effect Analysis):
FMEA (Failure Mode and Effect Analysis) can be used in various industries and situations where there is a need to identify and mitigate potential failures or risks associated with a particular process or product. Here are some common situations when FMEA can be used:
- New product development: FMEA can be used during the design phase of a new product to identify and address potential failures before they occur.
- Process improvement: FMEA can be used during the production phase of a process to continuously improve the quality and safety of the process.
- Regulatory compliance: FMEA can help organizations comply with industry regulations and standards related to risk management, such as ISO 9001, ISO 13485, and IEC 62304.
- Quality control: FMEA can be used as part of a quality control program to identify potential failures and take preventive or corrective actions.
- Safety analysis: FMEA can be used to assess the potential risks associated with a particular activity, equipment, or system to ensure safety.
Overall, FMEA is a proactive tool that can be used in various situations to prevent failures and reduce costs associated with failures. FMEA is best used when there is a need to identify and mitigate potential failures before they occur, and when there is a potential impact on product quality, safety, or regulatory compliance.
Risk priority number RPN in FMEA:
Failure Mode and Effects Analysis (FMEA) is a structured, systematic approach to identifying and evaluating potential failure modes and their effects on products or processes. The FMEA process involves breaking down the system or process being analyzed into individual components or steps, identifying potential failure modes and their causes, and assessing their potential impact.
FMEA uses a risk priority number (RPN) to quantify the level of risk associated with each potential failure mode. The RPN is calculated by multiplying the severity, occurrence, and detection scores assigned to each failure mode. The severity score represents the potential impact of the failure, the occurrence score represents the likelihood of the failure occurring, and the detection score represents the likelihood of the failure being detected before it causes harm.
Procedures of Failure Mode and Effects Analysis (FMEA
The FMEA procedure generally follows a structured approach to identify potential failures and their effects, prioritize them by their risk, and develop action plans to mitigate or eliminate the risks. Here are the typical steps of the FMEA procedure:
- Define the scope of the analysis: Define the system or process being analyzed, its boundaries, and its intended use.
- Assemble the team: Assemble a cross-functional team with expertise in the system or process being analyzed, including representatives from engineering, quality assurance, manufacturing, and other relevant departments.
- Break down the system or process: Break down the system or process into individual components or steps.
- Identify potential failure modes: Identify potential failure modes for each component or step.
- Determine the severity of each failure mode: Determine the severity of each failure mode by assessing its potential impact on the system or process and its users.
- Determine the occurrence of each failure mode: Determine the occurrence of each failure mode by assessing the likelihood of the failure occurring.
- Determine the detectability of each failure mode: Determine the detectability of each failure mode by assessing the likelihood of the failure being detected before it causes harm.
- Calculate the risk priority number (RPN): Calculate the RPN for each potential failure mode by multiplying the severity, occurrence, and detection scores assigned to each failure mode.
- Prioritize the failure modes: Prioritize the failure modes by their RPN and focus on those with the highest risk.
- Develop action plans: Develop action plans to mitigate or eliminate the highest-risk failure modes, including design changes, process changes, or other corrective and preventive actions.
- Implement the action plans: Implement the action plans and monitor their effectiveness.
- Reassess the FMEA periodically: Reassess the FMEA periodically, typically when changes are made to the system or process being analyzed, or at regular intervals determined by the organization’s quality management system.
Overall, the FMEA procedure is a structured and systematic approach to risk management that helps organizations identify potential failure modes, evaluate their risks, and develop action plans to reduce or eliminate the risks.
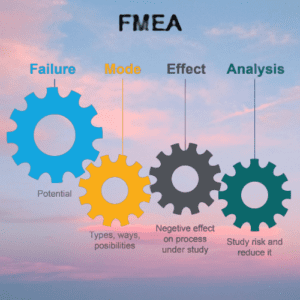
Calculation and formula in fmea :
The Risk Priority Number (RPN) is a score that is calculated for each potential failure mode identified during the FMEA process. The RPN is a product of three scores assigned to each potential failure mode:
RPN = Severity x Occurrence x Detection
where:
- Severity (S): represents the potential impact or severity of the failure mode on the system, process, or customer. Severity is typically scored on a scale of 1 to 10, with higher scores indicating more severe impacts.
- Occurrence (O): represents the likelihood or frequency of the failure mode occurring. Occurrence is typically scored on a scale of 1 to 10, with higher scores indicating more frequent occurrences.
- Detection (D): represents the likelihood or effectiveness of detecting the failure mode before it causes harm. Detection is typically scored on a scale of 1 to 10, with higher scores indicating a higher likelihood or effectiveness of detection.
The RPN score ranges from 1 to 1000, which is the maximum score possible if all three scores are at their highest level (10). The higher the RPN score, the higher the risk associated with the failure mode. The FMEA team can then prioritize the potential failure modes based on their RPN scores and develop action plans to mitigate or eliminate the highest-risk failure modes.
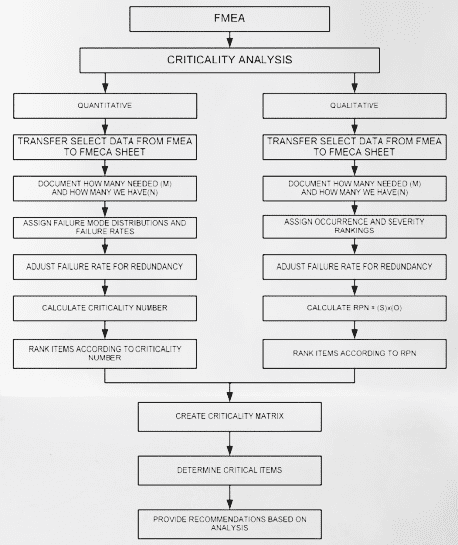
Failure Modes and Effects Analysis FMEA example:
Process: Tablet Coating process by Coating machine.
Step 1: Define the scope: Coating process for tablets at a pharmaceutical plant
Step 2: Assemble the team: A cross-functional team consisting of production, quality control, maintenance, and engineering personnel.
Step 3: Identify the functions
Function | Description |
Coating | Apply a coating to tablets to provide a protective layer and improve appearance. |
Drying | Dry the coated tablets to remove solvent and ensure uniform coating thickness. |
Packaging | Package the finished tablets for shipment. |
Step 4: Identify the failure modes:
Function | Failure Mode | Effect |
Coating | Inadequate coating thickness | Tablets are not protected or do not meet visual specifications. |
Coating | Excessive coating thickness | Tablets are over-protected or do not meet visual specifications. |
Coating | Coating uniformity issues | Tablets are not uniformly protected or do not meet visual specifications. |
Drying | Over-drying | Tablets become brittle and break or do not meet weight specifications. |
Drying | Under-drying | Tablets are not completely dry and may stick together or not meet weight specifications. |
Packaging | Incorrect labeling | Incorrect labeling can lead to incorrect usage, which can result in harm to patients or customers. |
Step 5: Determine the severity:
Failure Mode | Severity |
Inadequate coating thickness | 7 |
Excessive coating thickness | 5 |
Coating uniformity issues | 8 |
Over-drying | 6 |
Under-drying | 4 |
Incorrect labeling | 9 |
Step 6: Determine the occurrence:
Failure Mode | Occurrence |
Inadequate coating thickness | 2 |
Excessive coating thickness | 3 |
Coating uniformity issues | 4 |
Over-drying | 2 |
Under-drying | 3 |
Incorrect labeling | 2 |
Step 7: Determine the detection:
Failure Mode | Detection |
Inadequate coating thickness | 8 |
Excessive coating thickness | 6 |
Coating uniformity issues | 7 |
Over-drying | 7 |
Under-drying | 5 |
Incorrect labeling | 9 |
Step 8: Calculate the risk priority number (RPN):
Failure Mode | Severity | Occurrence | Detection | RPN |
Inadequate coating thickness | 7 | 2 | 8 | 112 |
Excessive coating thickness | 5 | 3 | 6 | 90 |
Coating uniformity issues | 8 | 4 | 7 | 224 |
Over-drying | 6 | 2 | 7 | 84 |
Under-drying | 4 | 3 | 5 | 60 |
Incorrect labeling | 9 | 2 | 9 | 162 |
Step 9: Prioritize the actions:
Based on the RPN scores, the team should focus on addressing the coating uniformity issues, followed by inadequate coating thickness and incorrect labeling.
Step 10: Implement the actions:
The team could consider actions such as improving the coating equipment, optimizing the coating process, implementing quality control checks during coating and drying, training personnel on labeling requirements, and reviewing labeling procedures.
Step 11: Review
After implementing the actions, the team should review and monitor the coating process regularly to ensure the improvements are effective and sustainable. They can also use FMEA to reassess the process periodically and identify any new failure modes or changes in severity, occurrence, or detection that require further action.
Step 12: Follow-up
The team should also conduct follow-up actions such as documenting the FMEA results, communicating the findings and recommendations to relevant stakeholders, and updating the risk management plan accordingly.
Step 13: Continuous Improvement
FMEA is a continuous improvement process, and the team should use the lessons learned from the FMEA to improve other processes and systems within the organization. They can also use the FMEA to identify opportunities for innovation and new product development, as well as to comply with regulatory requirements and industry standards.
Step 14: Cross-functional collaboration
FMEA is most effective when it involves cross-functional collaboration and communication. The team should ensure that all stakeholders are involved in the FMEA process, including suppliers, customers, regulators, and other relevant parties. They should also encourage open communication and a culture of continuous improvement within the organization.
Step 15: Training and Education
Finally, the team should provide adequate training and education to all personnel involved in the FMEA process to ensure that they have the knowledge, skills, and tools necessary to perform the analysis effectively. This can include training on risk assessment, root cause analysis, statistical analysis, and other relevant topics.
Step 16: Integration with other processes
FMEA can be integrated with other processes and tools, such as design control, process validation, and CAPA (Corrective and Preventive Action). By integrating FMEA with these processes, the team can ensure that risk management is incorporated throughout the product lifecycle and that risks are addressed proactively rather than reactively.
Step 17: Use of software tools
While FMEA can be performed manually using paper and pencil, there are also software tools available that can facilitate the process. These tools can help automate data collection, analysis, and reporting, as well as provide features such as real-time collaboration, risk prioritization, and decision support.
Step 18: Reassessment
As the product and process evolve over time, the team should reassess the FMEA periodically to ensure that the risk management plan remains effective and up-to-date. Reassessment may be triggered by changes in product design, manufacturing processes, regulatory requirements, or customer feedback.
Step 19: Integration with Quality Management System
FMEA is an integral part of the Quality Management System (QMS) and can be used to demonstrate compliance with regulatory requirements such as ISO 13485 and FDA QSR. By incorporating FMEA into the QMS, the team can ensure that risk management is ingrained into the organization’s culture and that continuous improvement is a core value.
Step 20: Sharing knowledge and best practices
Finally, FMEA can be used as a tool for sharing knowledge and best practices within the organization and with external stakeholders. By documenting and communicating the FMEA results and recommendations, the team can share their expertise and help others learn from their experiences. This can lead to improved collaboration, increased efficiency, and enhanced quality throughout the product lifecycle.
FMEA is a continuous improvement process, and teams should use it to monitor and reassess their processes periodically, incorporate risk management into their culture and values, and share their knowledge and best practices with others. FMEA can also be integrated with other processes and tools, such as design control, process validation, and CAPA, to ensure that risk management is incorporated throughout the product lifecycle.
Frequently Asked Questions:
What is the purpose of FMEA?
Answer: The purpose of FMEA is to identify and evaluate potential failure modes and their effects on products or processes and to develop action plans to reduce or eliminate their impact.
How is the risk priority number (RPN) calculated in FMEA?
Answer: The RPN is calculated by multiplying the severity, occurrence, and detection scores assigned to each failure mode.
What are the three key factors used to assess the risk of a failure mode in FMEA?
Answer: The three key factors used to assess the risk of a failure mode in FMEA are severity, occurrence, and detection.
What is the difference between FMEA and FMECA?
Answer: FMECA (Failure Mode, Effects, and Criticality Analysis) is a variant of FMEA that adds a criticality assessment to the evaluation of failure modes.
How often should FMEA be reassessed?
Answer: FMEA should be reassessed periodically, typically when changes are made to the product or process being analyzed, or at regular intervals determined by the organization’s quality management system.
What types of industries and processes can FMEA be applied to?
Answer: FMEA can be applied to a wide range of industries and processes, including manufacturing, healthcare, automotive, aerospace, and many others.
What are some common software tools used for FMEA?
Answer: Some common software tools used for FMEA include Excel, FMEA Pro, and Relex.
How can FMEA be integrated with other quality management processes?
Answer: FMEA can be integrated with other quality management processes, such as design control, process validation, and CAPA (Corrective and Preventive Action), to ensure that risk management is incorporated throughout the product lifecycle.
What are the benefits of using FMEA?
Answer: The benefits of using FMEA include reduced risk of product failures, improved product quality and reliability, compliance with regulatory requirements, and enhanced customer satisfaction.
How does FMEA support continuous improvement?
Answer: FMEA supports continuous improvement by identifying potential failure modes and developing action plans to reduce or eliminate their impact, and by reassessing the FMEA periodically to ensure that the risk management plan remains effective and up-to-date.
Also, Read Qualification/Validation Concept
Every time I read a new post, I feel like I’ve learned something valuable or gained a new perspective. Thank you for consistently putting out such great content!