Risk Assessment in the pharmaceutical industry begins with the identification and evaluation of potential risks at various stages, including research and development, manufacturing, distribution, and post-marketing surveillance. These risks can encompass a wide range of factors, such as product quality issues, adverse events, regulatory non-compliance, supply chain vulnerabilities, and emerging safety concerns. Through meticulous analysis and evaluation, stakeholders can gain a comprehensive understanding of the potential risks and their potential impact on patient safety and overall business operations.
The pharmaceutical industry plays a crucial role in improving human health and well-being by developing and manufacturing life-saving drugs. However, this industry operates within a complex landscape, where numerous factors can pose risks to the safety, efficacy, and regulatory compliance of pharmaceutical products. To mitigate these risks, a comprehensive approach to risk assessment is imperative. In this article, we delve into the realm of risk assessment in the pharmaceutical sector, exploring its importance, key components, and its role in ensuring the quality and safety of pharmaceutical products.
Important key steps of Risk Assessment in pharmaceuticals.
Risk assessment in the pharmaceutical industry involves several key steps to identify, evaluate, and manage risks effectively. Here are some important steps in the risk assessment process:
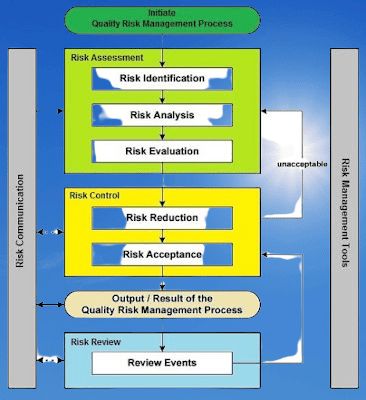
- Hazard Identification: The first step is to identify potential hazards or risks associated with pharmaceutical products, processes, or activities. This involves considering various factors such as product formulation, manufacturing methods, raw materials, equipment, and handling procedures. Thorough analysis and understanding of the entire product lifecycle are essential for comprehensive hazard identification.
- Risk Identification: Once hazards are identified, the next step is to assess and identify the specific risks associated with each hazard. This involves evaluating the likelihood and severity of potential harm or adverse effects. Risks can include product quality issues, safety concerns, regulatory non-compliance, supply chain vulnerabilities, and other factors that could impact patient safety or business operations.
- Risk Analysis and Evaluation: In this step, a systematic analysis and evaluation of identified risks are conducted. This involves gathering and reviewing relevant data, scientific literature, historical information, and expert knowledge. Quantitative or qualitative methods can be used to assess the probability and potential impact of each risk. The goal is to prioritize risks based on their significance and determine the appropriate level of attention and resources needed for risk mitigation.
- Risk Mitigation: Once risks are prioritized, risk mitigation strategies are developed to minimize or eliminate the identified risks. This involves implementing preventive measures, process improvements, and control mechanisms. Risk mitigation strategies may include quality control procedures, enhanced manufacturing practices, rigorous testing and validation, robust supply chain management, and training programs for personnel involved in pharmaceutical processes.
- Risk Monitoring and Review: Risk assessment is an ongoing process, and continuous monitoring of risks is essential. Regular monitoring allows for the detection of emerging risks, changes in the risk landscape, or the effectiveness of implemented mitigation measures. Reviewing risk assessment outcomes and incorporating feedback from stakeholders ensure that risk management strategies remain relevant and effective over time.
- Documentation and Reporting: Thorough documentation of the risk assessment process is crucial for transparency, accountability, and regulatory compliance. All steps, findings, risk assessments, and mitigation strategies should be recorded in a systematic manner. Clear and concise reporting of risk assessment outcomes and mitigation efforts enables effective communication with regulatory authorities, stakeholders, and internal teams.
- Regulatory Compliance: Compliance with regulatory guidelines and requirements is a critical aspect of risk assessment in the pharmaceutical industry. Ensuring that risk assessment processes align with regulatory expectations and standards is essential for obtaining market approvals, maintaining compliance throughout the product lifecycle, and meeting post-marketing surveillance requirements.
By following these key steps, pharmaceutical companies can systematically assess and manage risks, enhance patient safety, and ensure the production of high-quality pharmaceutical products. Effective risk assessment processes contribute to regulatory compliance, business continuity, and the overall success of the pharmaceutical industry.
Applications of the Risk Assessment
Application | Description |
---|---|
Product Development | Identify potential risks during the research and development phase of pharmaceutical products. |
Manufacturing Processes | Evaluate risks associated with manufacturing processes to ensure product quality and safety. |
Supply Chain Management | Assess risks in the supply chain, including raw material sourcing, transportation, and storage. |
Regulatory Compliance | Demonstrate compliance with regulatory requirements through comprehensive risk assessment. |
Quality Control | Identify risks that may impact product quality and implement measures to maintain quality standards. |
Clinical Trials | Evaluate risks and potential adverse events during clinical trials to ensure patient safety. |
Pharmacovigilance | Monitor and assess risks associated with the use of pharmaceutical products in real-world settings. |
Post-Marketing Surveillance | Continuously monitor risks and adverse events after product approval and take appropriate actions. |
Product Recall | Assess risks associated with product defects or safety concerns and initiate recalls, if necessary. |
Business Continuity | Identify risks that may disrupt business operations and implement contingency plans for continuity. |
Advantages and Disadvantages of Risk Assessment
Advantages | Disadvantages |
---|---|
Enhances Patient Safety | Subjectivity in risk assessment |
Identifies and mitigates potential risks | Limited availability of comprehensive data |
Supports regulatory compliance | Inherent uncertainties in risk estimation |
Improves product quality and efficacy | Resource-intensive process |
Minimizes financial and reputational risks | Challenges in predicting rare or long-term risks |
Enables proactive risk management | Difficulty in quantifying subjective risks |
Facilitates informed decision-making | Potential for overestimating or underestimating risks |
Promotes business continuity | Interpretation and communication challenges |
Strengthens stakeholder trust and confidence | Lack of harmonization in risk assessment methodologies |
Importance of Risk Assessment in pharmaceuticals
Risk assessment plays a crucial role in the pharmaceutical industry due to its significance in ensuring the safety, efficacy, and quality of pharmaceutical products. Here are some key reasons highlighting the importance of risk assessment in pharmaceuticals:
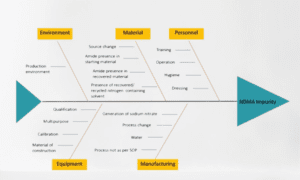
- Patient Safety: The primary objective of risk assessment in the pharmaceutical industry is to safeguard patient safety. By systematically identifying, evaluating, and managing risks, pharmaceutical companies can minimize the potential harm or adverse effects associated with their products. This proactive approach helps prevent safety-related incidents and ensures that patients receive medications that meet stringent quality and safety standards.
- Regulatory Compliance: Regulatory authorities, such as the Food and Drug Administration (FDA) and the European Medicines Agency (EMA), require pharmaceutical companies to conduct thorough risk assessments as part of their regulatory submissions. Compliance with regulatory guidelines is essential for obtaining market approvals and maintaining compliance throughout the product lifecycle. Effective risk assessment helps companies meet regulatory requirements and demonstrate their commitment to product safety and quality.
- Quality Assurance: Risk assessment is closely linked to quality assurance in the pharmaceutical industry. By identifying and assessing potential risks, companies can implement robust quality control measures and processes to minimize product defects, deviations, and non-compliance. This helps maintain product quality and consistency, which is crucial for ensuring the desired therapeutic outcomes and building trust among healthcare professionals and patients.
- Business Continuity: Understanding and managing risks are vital for ensuring the smooth operation of pharmaceutical businesses. By assessing potential risks, companies can develop contingency plans and implement risk management strategies to minimize disruptions to manufacturing, supply chain, and distribution processes. This helps maintain business continuity, safeguarding revenue streams and preventing potential financial losses.
- Reputation and Trust: Effective risk assessment practices contribute to building a positive reputation and instilling trust in pharmaceutical companies. By proactively addressing potential risks, companies demonstrate their commitment to product safety and patient well-being. This fosters confidence among healthcare professionals, regulatory authorities, and patients, leading to stronger relationships, enhanced brand reputation, and increased market competitiveness.
- Cost Reduction: Risk assessment can contribute to cost reduction in the long run. By identifying and mitigating risks early in product development and manufacturing processes, companies can avoid costly recalls, litigation, and product failures. Proactive risk management helps optimize resources, reduce waste, and streamline operations, resulting in improved efficiency and cost savings.
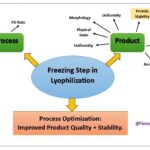
Calculations and formulas of RPN number calculations in risk assessment
In risk assessment, the Risk Priority Number (RPN) is a numerical value used to prioritize risks based on their severity, occurrence probability, and detection capability. The RPN is calculated by multiplying these three factors together. Here is an example of how the RPN is calculated:
RPN = Severity x Occurrence x Detection
Each factor is typically assigned a value on a numerical scale, such as 1 to 10, with 10 indicating the highest severity, occurrence, or detection capability. The higher the RPN value, the higher the priority of the risk.
To provide a clearer understanding, here are two tables that illustrate the calculation of the RPN in risk assessment:
1: Severity:
Severity | Description |
---|---|
1 | Negligible impact on patient safety or product quality |
2 | Minor impact on patient safety or product quality |
3 | Moderate impact on patient safety or product quality |
4 | Major impact on patient safety or product quality |
5 | Critical impact on patient safety or product quality |
2. Occurrence Scale:
Occurrence | Description |
---|---|
1 | Very rare occurrence |
2 | Rare occurrence |
3 | Occasional occurrence |
4 | Frequent occurrence |
5 | Very frequent occurrence |
3. Detection Scale:
Detection | Description |
---|---|
1 | Highly detectable |
2 | Detectable |
3 | Moderately detectable |
4 | Slightly detectable |
5 | Not detectable |
To calculate the RPN for a specific risk, assign a numerical value to each factor based on its severity, occurrence, and detection capability. Multiply these values together to obtain the RPN.
For example, let’s assume a risk has a severity of 3, an occurrence of 4, and detection of 2. The RPN would be calculated as follows:
RPN = 3 (Severity) x 4 (Occurrence) x 2 (Detection) = 24
In this case, the RPN value for the risk would be 24, indicating its priority level based on the severity, occurrence, and detection factors.
It’s important to note that the specific scales, values, and criteria used for severity, occurrence, and detection may vary depending on the organization or risk assessment methodology being employed. The tables provided above are just examples and can be customized to suit specific requirements and contexts.
Example of Risk Assessment
Risk Assessment of Coating Machine of a Pharma Plant
Objective: The aim of this risk assessment is to identify and evaluate potential risks associated with the operation of a coating machine in a pharmaceutical plant.
Step 1: Hazard Identification
- Identify potential hazards related to the coating machine, such as:
- Electrical hazards (e.g., faulty wiring, electrical shocks)
- Fire hazards (e.g., overheating, flammable materials)
- Chemical hazards (e.g., exposure to harmful substances)
- Mechanical hazards (e.g., moving parts, entanglement risks)
- Process-related hazards (e.g., improper coating, equipment failure)
Step 2: Risk Identification
- Assess the risks associated with each identified hazard. For example:
- Electrical hazard risk: Likelihood – 3, Severity – 4, Detection – 4, RPN = 3 x 4 x 4 = 48
- Fire hazard risk: Likelihood – 2, Severity – 3, Detection – 3, RPN = 2 x 3 x 3 = 18
- Chemical hazard risk: Likelihood – 3, Severity – 5, Detection – 2, RPN = 3 x 5 x 2 = 30
- Mechanical hazard risk: Likelihood – 4, Severity – 4, Detection – 3, RPN = 4 x 4 x 3 = 48
- Process-related hazard risk: Likelihood – 3, Severity – 3, Detection – 4, RPN = 3 x 3 x 4 = 36
Step 3: Risk Analysis and Evaluation
- Prioritize risks based on their Risk Priority Numbers (RPNs).
- Identify high-priority risks that require immediate attention and mitigation efforts.
- For example, the electrical hazard risk and mechanical hazard risk both have RPNs of 48, indicating they should be addressed promptly.
Step 4: Risk Mitigation
- Develop risk mitigation strategies for high-priority risks. Some examples include:
- Implementing regular maintenance and inspection schedules for electrical components.
- Installing fire suppression systems and ensuring proper storage and handling of flammable materials.
- Providing appropriate personal protective equipment and training for handling hazardous chemicals.
- Ensuring proper machine guarding and implementing lockout/tagout procedures for maintenance activities.
- Establishing standard operating procedures and quality control measures to minimize process-related risks.
Step 5: Risk Monitoring and Review
- Regularly monitor and review the effectiveness of implemented risk mitigation measures.
- Conduct periodic inspections, audits, and safety assessments to identify any emerging risks or areas for improvement.
- Update the risk assessment as new hazards or control measures are identified.
Step 6: Documentation and Reporting
- Document all risk assessment findings, mitigation strategies, and ongoing risk management efforts.
- Ensure clear and concise reporting of risk assessment outcomes to relevant stakeholders, including management, safety personnel, and regulatory authorities.
By following these steps, the pharmaceutical plant can systematically assess and manage the risks associated with the coating machine, promoting a safe and efficient working environment while ensuring the production of high-quality pharmaceutical products.
Conclusion:
Risk assessment plays a pivotal role in the pharmaceutical industry, safeguarding patient safety, ensuring regulatory compliance, and maintaining the reputation of pharmaceutical companies. By proactively identifying, evaluating, and managing risks throughout the product lifecycle, stakeholders can mitigate potential threats, optimize manufacturing processes, and deliver high-quality pharmaceutical products. As the industry continues to evolve, embracing emerging technologies and collaborative approaches will enable the development of robust risk assessment strategies, further enhancing patient care and advancing the field of pharmaceutical sciences.
Frequently Asked Questions:
What is risk assessment in the context of pharmaceuticals?
Answer: Risk assessment in pharmaceuticals is a systematic process of identifying, evaluating, and managing potential risks associated with pharmaceutical products, processes, or activities.
Why is risk assessment important in the pharmaceutical industry?
Answer: Risk assessment is important in the pharmaceutical industry as it helps ensure patient safety, regulatory compliance, product quality, and business continuity.
What are the key steps involved in risk assessment in pharmaceuticals?
Answer: The key steps in risk assessment include hazard identification, risk identification, risk analysis and evaluation, risk mitigation, risk monitoring and review, and documentation and reporting.
How are risks prioritized in pharmaceutical risk assessment?
Answer: Risks are prioritized by assigning Risk Priority Numbers (RPNs) based on factors such as severity, occurrence, and detection capability. Higher RPN values indicate higher priority risks.
What are some common hazards in pharmaceutical risk assessment?
Answer: Common hazards in pharmaceutical risk assessment include chemical hazards, biological hazards, mechanical hazards, fire hazards, electrical hazards, and process-related hazards.
How is the severity of risks determined in pharmaceutical risk assessment?
Answer: Severity of risks is determined by assessing the potential impact or consequences on patient safety, product quality, or business operations. Severity scales, such as 1 to 5, are commonly used.
How is the occurrence of risks evaluated in pharmaceutical risk assessment?
Answer: Occurrence of risks is evaluated by assessing the likelihood or frequency of the risk event happening. Likelihood scales, such as 1 to 5, are commonly used.
What is detection capability in pharmaceutical risk assessment?
Answer: Detection capability refers to the ability to detect or identify a risk before it causes harm or adverse effects. It is assessed based on factors like detectability, observability, or monitoring effectiveness.
What are some risk mitigation strategies used in pharmaceuticals?
Answer: Risk mitigation strategies in pharmaceuticals include implementing preventive measures, process improvements, quality control measures, training and education, safety protocols, and use of protective equipment.
How often should risk assessments be conducted in the pharmaceutical industry?
Answer: Risk assessments should be conducted regularly, considering factors like changes in processes, technologies, regulations, or new risks identified. It is recommended to review and update risk assessments periodically or when significant changes occur.
How does risk assessment contribute to regulatory compliance in the pharmaceutical industry?
Answer: Risk assessment helps pharmaceutical companies meet regulatory requirements by identifying and mitigating potential risks, ensuring product safety, and demonstrating a commitment to quality and patient well-being.
Can risk assessment help minimize financial and reputational risks in the pharmaceutical industry?
Answer: Yes, risk assessment helps identify and manage risks that could lead to financial losses or damage to the company’s reputation. By proactively addressing risks, companies can minimize the likelihood and impact of such risks.
How does risk assessment support decision-making in the pharmaceutical industry?
Answer: Risk assessment provides valuable information about potential risks and their consequences, aiding in informed decision-making regarding product development, manufacturing processes, risk control measures, and resource allocation.
What role does risk assessment play in continuous improvement in the pharmaceutical industry?
Answer: Risk assessment promotes continuous improvement by identifying areas for enhancement, enabling the implementation of risk mitigation measures, and monitoring their effectiveness over time.
9 thoughts on “Risk Assessment in Pharma 2023”