Failure Mode, Effects, and Criticality Analysis (FMECA) is used to identify potential failure modes in a system, process, or product, determine their potential impact, and prioritize corrective actions based on their criticality. FMECA is widely used in various industries, including pharmaceuticals, to improve product quality, reliability, and safety. It involves a systematic approach to analyzing potential failure modes and their effects on a system or process and can be used to improve the design, manufacturing, and maintenance processes.
Failure Mode, Effects, and Criticality Analysis (FMECA) is a systematic approach used to identify potential failure modes (ways in which a system or component could fail), their effects on the system or component, and the criticality of those effects. It is often used in engineering, manufacturing, and other industries to evaluate the potential risks associated with a system or process.
FMECA involves breaking down a system or process into its individual components and analyzing each component for potential failure modes. The failure modes are then assessed for their potential effects on the system or process, as well as their likelihood of occurring and their detectability. The criticality of each failure mode is then determined based on the severity of its effects and the likelihood of its occurrence.
FMECA can be used to identify potential design or process flaws and to prioritize corrective actions. It can also be used to identify critical components that require additional monitoring or maintenance to prevent failures. FMECA is a valuable tool for ensuring the reliability and safety of complex systems and processes.
Steps of Failure Mode, Effects, and Criticality Analysis in pharma
Performing a Failure Mode, Effects and Criticality Analysis (FMECA) typically involves the following steps:
- Define the scope of the analysis: Identify the system, process, or component that will be analyzed, and define the boundaries of the analysis.
- Assemble a team: Bring together a team of subject matter experts who have knowledge and experience with the system or process being analyzed.
- Break down the system into components: Break down the system or process into its individual components and identify the functions of each component.
- Identify failure modes: For each component, identify potential failure modes that could occur and how each failure mode might affect the overall system or process.
- Assign severity ratings: Assign a severity rating to each failure mode based on the potential impact on the system or process.
- Assign occurrence ratings: Assign an occurrence rating to each failure mode based on the likelihood of the failure mode occurring.
- Assign detection ratings: Assign a detection rating to each failure mode based on the likelihood of detecting the failure mode before it leads to a system or process failure.
- Calculate the criticality ranking: Calculate the criticality ranking for each failure mode by multiplying the severity, occurrence, and detection ratings.
- Develop corrective actions: Based on the criticality rankings, identify corrective actions that can be taken to mitigate the risks associated with the most critical failure modes.
- Implement and monitor corrective actions: Implement the corrective actions and monitor their effectiveness to ensure that they are reducing the risks associated with the identified failure modes.
FMECA can be a complex and time-consuming process, but it can help to identify potential risks and ensure the reliability and safety of complex systems and processes.

Difference between FMECA and FMEA
FMECA and FMEA are both methods used to analyze potential failures and their effects on a system or process. The main difference between them is that FMECA takes into account the criticality of each failure mode, while FMEA does not.
FMEA (Failure Mode and Effects Analysis) is a systematic approach for identifying potential failure modes, their causes and their effects on a system or process. It involves three steps:
1) identifying potential failure modes,
2) assessing the severity of the effects of the failure modes, and
3) evaluating the likelihood of the failure modes occurring and the ability to detect them before they cause harm. FMEA is often used in the early stages of product development to identify potential problems before they occur and to implement preventive actions.
FMECA (Failure Mode, Effects, and Criticality Analysis) is a more advanced version of FMEA that takes into account the criticality of each failure mode. It adds an additional step to the FMEA process, where the criticality of each failure mode is calculated by multiplying the severity of the effects, the likelihood of occurrence, and the ability to detect it. FMECA is typically used to evaluate and prioritize the most critical failure modes for corrective action.
In the pharmaceutical industry, FMEA and FMECA are commonly used in the development and manufacturing of drugs and medical devices to identify potential risks and ensure the safety and efficacy of the products. These methods are used to analyze various processes, such as drug synthesis, packaging, and transportation, as well as clinical trials and post-marketing surveillance. FMECA is particularly useful in the pharmaceutical industry to identify the most critical failure modes and prioritize corrective actions to ensure the safety and efficacy of the products.
Calculation and formula in Failure Mode, Effects and Criticality Analysis FMECA
The Failure Mode, Effects, and Criticality Analysis (FMECA) tool uses a formula to calculate the criticality ranking for each failure mode. The formula is:
Criticality Ranking = Severity Rating x Occurrence Rating x Detection Rating
where:
- Severity Rating: A value from 1 to 10 that represents the potential impact of the failure mode on the system or process, with 10 being the highest severity.
- Occurrence Rating: A value from 1 to 10 that represents the likelihood of the failure mode occurring, with 10 being the highest likelihood.
- Detection Rating: A value from 1 to 10 that represents the likelihood of the failure mode being detected before it leads to a system or process failure, with 10 being the highest likelihood.
The resulting criticality ranking value is a measure of the risk associated with each failure mode. The higher the criticality ranking, the greater the risk and the more urgent the need for corrective action.
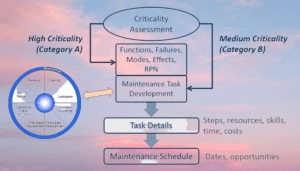
Once the criticality rankings are calculated, the failure modes can be prioritized based on their ranking to determine which ones require immediate attention and which ones can be addressed later.
It’s important to note that different organizations may use slightly different formulas or scales for severity, occurrence, and detection ratings. Therefore, it’s crucial to clarify the exact formulas and scales being used when conducting an FMECA analysis.
Key Points of FMECA analysis:
Key Point | Description |
---|---|
Objective | To identify potential failure modes in a system, process, or product, determine their potential impact, and prioritize corrective actions based on their criticality. |
Steps | FMECA typically involves the following steps: (1) Define the system, process, or product to be analyzed. (2) Identify potential failure modes and their causes. (3) Determine the severity, frequency, and detectability of each failure mode. (4) Calculate the risk priority number (RPN) for each failure mode. (5) Prioritize corrective actions based on the RPN. (6) Implement corrective actions and monitor their effectiveness. |
Severity | The severity of a failure mode is a measure of the impact of the failure on the system or process. It is typically rated on a scale of 1 to 10, with 10 being the most severe. |
Frequency | The frequency of a failure mode is a measure of how often the failure is likely to occur. It is typically rated on a scale of 1 to 10, with 10 being the most frequent. |
Detectability | The detectability of a failure mode is a measure of how likely it is to be detected before it causes harm. It is typically rated on a scale of 1 to 10, with 10 being the most detectable. |
Risk Priority Number (RPN) | The RPN is calculated by multiplying the severity, frequency, and detectability ratings for each failure mode. The higher the RPN, the higher the priority for corrective action. |
Corrective Actions | Corrective actions are prioritized based on the RPN and may include design changes, process improvements, or operator training. |
Effectiveness | Corrective actions should be monitored for effectiveness, and the FMECA process should be reviewed and updated periodically. |
Benefits | FMECA can help improve product quality, reliability, and safety, reduce downtime and maintenance costs, and enhance regulatory compliance. |
Failure Mode, Effects, and Criticality Analysis FMECA example using aseptic sterile process.
Failure Mode, Effects, and Criticality Analysis (FMECA) in the Context of an Aseptic sterile process in a pharmaceutical manufacturing facility:
- Define the scope and objectives: The objective of the FMECA is to identify potential failure modes in the aseptic sterile process used to manufacture a new drug product.
- Assemble a team: The FMECA team consists of a process engineer, a quality assurance specialist, a manufacturing operator, and a microbiologist.
- Identify the system or process functions: The aseptic sterile process includes multiple steps, including cleaning, sterilization, filling, capping, and labeling.
- Break down the system into components: Each step is divided into individual components, such as the filling machine, capping machine, and labeling machine.
- Identify potential failure modes: The team identifies potential failure modes for each component, such as microbial contamination during filling, incomplete capping, and incorrect labeling.
- Assign severity ratings: The team assigns severity ratings for each failure mode based on the potential impact on the final product, such as microbial contamination leading to a batch rejection (severity rating of 10) or incorrect labeling leading to a recall (severity rating of 9).
- Assign occurrence ratings: The team assigns occurrence ratings for each failure mode based on the likelihood of the failure mode occurring, such as microbial contamination due to inadequate cleaning procedures (occurrence rating of 8) or incomplete capping due to equipment malfunction (occurrence rating of 6).
- Assign detection ratings: The team assigns detection ratings for each failure mode based on the likelihood of detecting the failure mode before it leads to a product quality issue, such as microbial contamination detected during in-process sampling (detection rating of 9) or incomplete capping detected during visual inspection (detection rating of 8).
- Calculate the criticality ranking: The team calculates the criticality ranking for each failure mode by multiplying the severity, occurrence, and detection ratings.
- Prioritize the failure modes: The team ranks the failure modes based on their criticality rankings and prioritizes which ones require immediate attention, such as microbial contamination due to inadequate cleaning procedures or incomplete capping due to equipment malfunction.
- Develop corrective actions: The team develops corrective actions to mitigate the risks associated with the most critical failure modes, such as improving cleaning procedures or conducting preventative maintenance on the capping equipment.
- Implement and monitor corrective actions: The team implements the corrective actions and monitors their effectiveness to ensure that they are reducing the risks associated with the identified failure modes.
- Review and update the FMECA: The team periodically reviews and updates the FMECA as changes occur in the aseptic sterile process to ensure continued effectiveness.
This example shows how FMECA can be used to identify potential failure modes and prioritize corrective actions to reduce risks in an aseptic sterile process used to manufacture a pharmaceutical product.

Use of FMECA in Pharma
FMECA is commonly used in the pharmaceutical industry to improve the quality, reliability, and safety of pharmaceutical products and manufacturing processes. Here are some specific areas in pharmaceuticals where FMECA is utilized:
- Product development: FMECA is used during the product development process to identify and mitigate potential risks associated with the drug product and its manufacturing process.
- Manufacturing process: FMECA is used to identify potential failure modes in the manufacturing process, including equipment failure, contamination, and human error, and to prioritize corrective actions to reduce risks.
- Quality control: FMECA is used to identify potential failure modes in quality control procedures and to prioritize corrective actions to improve the accuracy and reliability of quality control tests.
- Regulatory compliance: FMECA is used to identify potential compliance risks associated with the manufacturing process and to prioritize corrective actions to ensure compliance with regulatory requirements.
- Facility design and maintenance: FMECA is used to identify potential risks associated with facility design and maintenance, including equipment maintenance, environmental controls, and personnel hygiene, and to prioritize corrective actions to ensure a safe and effective manufacturing environment.
In summary, FMECA is used in various areas of pharmaceuticals to identify potential risks, prioritize corrective actions, and improve product quality, reliability, and safety.
Difference Between FMECA and FMEA
Aspect | FMECA | FMEA | Utilization in Pharmaceuticals |
---|---|---|---|
Definition | A systematic method for identifying potential failure modes, determining their effects, and prioritizing corrective actions based on their criticality. | A systematic method for identifying potential failure modes and determining their effects. | Both FMECA and FMEA are utilized in pharmaceuticals to identify and mitigate potential risks associated with the drug product and its manufacturing process. |
Objective | To identify potential failure modes, determine their potential impact, and prioritize corrective actions based on their criticality. | To identify potential failure modes and their effects. | FMECA is generally used to prioritize corrective actions and focus resources on the most critical failure modes, while FMEA is typically used to identify potential failure modes and their effects on a system or process. |
Steps | FMECA typically involves additional steps beyond FMEA, such as determining the detectability of each failure mode and calculating the risk priority number (RPN) for each failure mode. | FMEA typically involves fewer steps than FMECA, focusing on identifying potential failure modes and their effects. | FMECA is more commonly used in the pharmaceutical industry due to the additional steps it involves, which can help prioritize corrective actions more effectively. |
Ratings | FMECA typically uses severity, frequency, and detectability ratings to determine the RPN for each failure mode. | FMEA typically uses severity and occurrence ratings to determine the risk priority number (RPN) for each failure mode. | Both FMECA and FMEA use ratings to determine the criticality of each failure mode, but FMECA typically includes an additional detectability rating. |
Criticality | FMECA prioritizes corrective actions based on the RPN, which takes into account the severity, frequency, and detectability of each failure mode. | FMEA prioritizes corrective actions based on the RPN, which takes into account the severity and occurrence of each failure mode. | FMECA is generally considered to be more effective in identifying and prioritizing critical failure modes, while FMEA is more commonly used to identify potential failure modes in a system or process. |
Utilization | FMECA is commonly used in industries where safety and reliability are critical, such as aerospace, defense, and automotive. It is also widely used in the pharmaceutical industry to improve product quality, reliability, and safety. | FMEA is commonly used in various industries, including automotive, aerospace, and electronics, to identify potential failure modes and their effects. It is also utilized in the pharmaceutical industry to identify potential risks associated with the manufacturing process. | Both FMECA and FMEA are widely utilized in the pharmaceutical industry to improve the quality, reliability, and safety of drug products and their manufacturing processes. |
Frequently Asked Questions:
What is FMECA?
Answer: FMECA is an acronym for Failure Mode, Effects and Criticality Analysis, which is a systematic method used to identify potential failure modes, determine their effects, and prioritize corrective actions based on their criticality.
What is the purpose of FMECA?
Answer: The purpose of FMECA is to identify and prioritize potential failure modes in a system, process, or product, and determine the potential impact of each failure mode on the overall system or process. This information is then used to prioritize corrective actions and focus resources on the most critical failure modes.
What industries commonly use FMECA?
Answer: FMECA is commonly used in industries where safety and reliability are critical, such as aerospace, defense, automotive, and pharmaceuticals.
What is the difference between FMECA and FMEA?
Answer: FMECA is similar to FMEA (Failure Mode and Effects Analysis), but with additional steps that involve determining the detectability of each failure mode and calculating the risk priority number (RPN) for each failure mode. FMEA, on the other hand, focuses on identifying potential failure modes and their effects on a system or process but typically does not include the additional steps used in FMECA.
How is FMECA used in pharmaceuticals?
Answer: FMECA is used in the pharmaceutical industry to identify and mitigate potential risks associated with drug products and their manufacturing processes. This includes identifying potential failure modes in equipment, processes, and materials used in drug manufacturing, and prioritizing corrective actions based on their criticality.
You may also read Disinfectant Efficacy Test in Microbiology