The concept of Good Engineering Practices (GEP) encompasses a set of principles, methodologies, and guidelines that serve as a foundation for ensuring quality, safety, and efficiency in engineering processes across various industries. GEP provides a framework for professionals to follow standardized practices and procedures, promoting consistency, reliability, and compliance in their work.
At its core, Good Engineering Practice emphasizes the application of established engineering principles, best practices, and industry standards to achieve optimal results. It encompasses a wide range of disciplines, including but not limited to chemical engineering, mechanical engineering, electrical engineering, and civil engineering.
The key objectives of GEP can be summarized as follows:
- Quality: GEP aims to ensure that engineering projects, products, and processes meet defined quality standards and specifications. It involves implementing rigorous quality control measures, conducting thorough inspections and testing, and adhering to relevant regulatory requirements.
- Safety: GEP places a strong emphasis on the safety of personnel, the public, and the environment. It involves identifying and mitigating potential hazards, designing systems and structures with safety in mind, and following industry-specific safety codes and regulations.
- Efficiency: GEP seeks to optimize engineering processes, resource utilization, and project execution. It focuses on enhancing productivity, reducing waste, streamlining workflows, and maximizing the utilization of available resources.
- Compliance: GEP ensures adherence to applicable laws, regulations, and industry standards. It requires staying updated with regulatory requirements, implementing appropriate documentation and record-keeping practices, and conducting regular audits and inspections to ensure compliance.
- Continuous Improvement: GEP promotes a culture of continuous improvement by encouraging professionals to learn from past experiences, implement lessons learned, and embrace emerging technologies and best practices. It involves analyzing performance metrics, identifying areas for improvement, and implementing corrective and preventive actions.
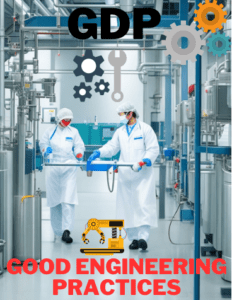
Important Aspects of the Good Engineering Practices:
- Facility Design and Layout:
- Plan the facility layout to ensure efficient workflow and minimize the risk of cross-contamination.
- Segregate different manufacturing areas to prevent cross-contamination and maintain product integrity.
- Design HVAC systems that provide appropriate air filtration, temperature, humidity, and pressure differentials to meet regulatory requirements.
- Incorporate adequate storage areas for raw materials, intermediates, and finished products, considering proper labeling and segregation.
- Equipment Selection and Validation:
- Choose equipment that meets industry standards and regulatory requirements.
- Ensure equipment is properly calibrated, qualified, and validated before use.
- Develop and execute a comprehensive equipment maintenance and calibration program.
- Establish procedures for cleaning and sanitizing equipment to prevent product contamination.
- Documentation and Record Keeping:
- Maintain accurate and up-to-date documentation for all processes, procedures, and equipment.
- Implement a document control system to manage revisions, approvals, and archiving.
- Establish protocols for batch record documentation, including batch manufacturing records, equipment usage logs, and analytical data.
- Conduct regular reviews of documentation to identify areas for improvement and compliance.
- Training and Competency:
- Provide comprehensive training programs for employees involved in manufacturing, quality control, and other critical functions.
- Ensure that employees understand GEP principles, standard operating procedures (SOPs), and regulatory requirements.
- Regularly assess and evaluate employee competency through training assessments and performance reviews.
- Foster a culture of continuous learning and improvement within the organization.
- Quality Control and Testing:
- Establish a robust quality control program to monitor and verify the quality of raw materials, intermediates, and finished products.
- Implement validated analytical testing methods to ensure accurate and reliable results.
- Conduct regular equipment calibration and maintenance to maintain measurement accuracy.
- Perform thorough investigations of any deviations, out-of-specification results, or quality incidents.
- Change Control and Risk Management:
- Develop a change control process to assess and manage the impact of proposed changes to facilities, equipment, processes, or materials.
- Conduct risk assessments to identify potential hazards, vulnerabilities, and mitigation strategies.
- Implement effective risk management strategies, such as failure mode and effects analysis (FMEA) and hazard analysis and critical control points (HACCP).
- Regulatory Compliance:
- Stay updated with current regulations, guidelines, and industry best practices.
- Conduct regular internal audits and inspections to ensure compliance with GEP and regulatory requirements.
- Maintain open communication with regulatory authorities and promptly address any compliance issues or inspections.
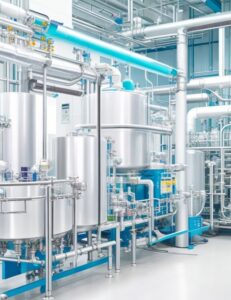
Guidelines for Good Engineering Practices in the pharmaceutical industry
Worldwide guidelines that provide guidance regarding Good Engineering Practices in the pharmaceutical industry:
Worldwide Guidelines for Good Engineering Practices in Pharmaceutical Industry |
---|
1. International Society for Pharmaceutical Engineering (ISPE) |
2. Good Manufacturing Practices (GMP) – Various regulatory authorities (e.g., FDA, EMA, WHO) provide GMP guidelines that encompass GEP. |
3. International Conference on Harmonisation (ICH) Guidelines |
4. European Medicines Agency (EMA) Guidelines |
5. Pharmaceutical Inspection Co-operation Scheme (PIC/S) Guidelines |
6. United States Pharmacopeia (USP) General Chapters |
7. World Health Organization (WHO) Guidelines for Pharmaceutical Manufacturing |
8. Parenteral Drug Association (PDA) Technical Reports |
9. International Organization for Standardization (ISO) Standards (e.g., ISO 14644 for cleanrooms and controlled environments) |
10. ASTM International Standards |
Advantages of Good Engineering Practices (GEP)
Advantages of Good Engineering Practices |
---|
1. Enhanced Quality |
2. Improved Safety and Risk Mitigation |
3. Increased Efficiency and Productivity |
4. Compliance with Regulations and Standards |
5. Effective Resource Utilization |
6. Consistency and Reliability |
7. Facilitates Interoperability and Collaboration |
8. Cost Reduction and Avoidance |
9. Continuous Improvement and Innovation |
10. Customer Satisfaction and Trust |
Frequently Asked Questions:
What is the Full form of GEP?
Answer: The full form of GEP in the context of Good Engineering Practice is “Good Engineering Practice” itself. GEP refers to a set of principles, methodologies, and guidelines that ensure quality, safety, and efficiency in engineering processes across various industries, including the pharmaceutical industry. It is a recognized standard for maintaining consistent and reliable engineering practices to achieve optimal outcomes.
Why is GEP necessary?
Answer: GEP is necessary to ensure quality, safety, and efficiency in engineering processes. It provides a framework for standardized practices, guidelines, and principles to be followed, resulting in consistent and reliable outcomes. GEP helps organizations meet regulatory requirements, mitigate risks, optimize resource utilization, and deliver high-quality products or services.
What is the concept of good engineering practice?
Answer: The concept of Good Engineering Practice (GEP) encompasses a set of principles, methodologies, and guidelines that serve as a foundation for ensuring quality, safety, and efficiency in engineering processes across industries. GEP emphasizes the application of established engineering principles, best practices, and industry standards to achieve optimal results. It promotes consistency, reliability, compliance, and a culture of continuous improvement in engineering work.
What are standards in engineering practice?
Answer: Standards in engineering practice are recognized guidelines, specifications, or practices that define the expected level of quality, safety, and performance in engineering projects or processes. These standards are developed and maintained by reputable organizations, professional bodies, or regulatory authorities. They provide a reference framework for engineering professionals to ensure consistency, compliance, and adherence to best practices in their work.
What is the role of engineering in the pharmaceutical industry?
Answer: Engineering plays a crucial role in the pharmaceutical industry. It involves designing, implementing, and maintaining facilities, equipment, and processes required for the manufacturing, packaging, and quality control of pharmaceutical products. Engineering ensures compliance with regulatory requirements, facilitates efficient and safe operations, enables process optimization, and contributes to the overall quality, safety, and effectiveness of pharmaceutical products.
What is the purpose of conducting equipment validation in adherence to Good Engineering Practice?
Answer: Equipment validation ensures that pharmaceutical manufacturing equipment performs consistently and meets predefined quality standards. It involves testing and documenting equipment performance to ensure reliability, accuracy, and compliance with regulatory requirements.
How does Good Engineering Practice influence the design and construction of cleanrooms in the pharmaceutical industry?
Answer: Good Engineering Practice provides guidelines for designing cleanrooms to achieve controlled environments with specified air cleanliness, temperature, humidity, and pressure differentials. It ensures that cleanrooms meet regulatory requirements, prevent contamination, and maintain product integrity.
What role does risk assessment play in implementing Good Engineering Practice in pharmaceutical manufacturing?
Answer: Risk assessment is crucial in GEP as it helps identify potential hazards, vulnerabilities, and critical control points. It enables the implementation of risk mitigation strategies to minimize risks associated with equipment, processes, and product quality, ensuring safe and effective operations.
How does Good Engineering Practice influence the selection and installation of process equipment in pharmaceutical manufacturing?
Answer: GEP provides criteria for selecting process equipment based on factors such as suitability for intended use, compliance with regulatory requirements, reliability, and ease of maintenance. It also guides proper installation, ensuring equipment is integrated into the manufacturing process correctly.
What are the key considerations for implementing effective process control systems in adherence to Good Engineering Practice?
Answer: GEP emphasizes the need for robust process control systems, including advanced automation, monitoring, and data acquisition. Key considerations include accurate measurement and control of process parameters, real-time monitoring, alarms for deviations, and data integrity for process optimization and compliance.
How does Good Engineering Practice influence the qualification and maintenance of utility systems in the pharmaceutical industry?
Answer: GEP requires the qualification and maintenance of utility systems such as HVAC, water systems, and compressed air systems. It ensures these systems are designed, installed, and operated to provide the required quality and comply with regulatory standards, contributing to the overall quality of pharmaceutical manufacturing.
Can you explain the role of Standard Operating Procedures (SOPs) in maintaining Good Engineering Practice in pharmaceutical manufacturing?
Answer: SOPs are integral to GEP implementation as they provide step-by-step instructions for routine operations, equipment handling, maintenance, and quality control. SOPs ensure consistency, reduce errors, and facilitate compliance with GEP standards across various processes and functions.
How does Good Engineering Practice influence the design and implementation of effective environmental monitoring programs in pharmaceutical facilities?
Answer: GEP mandates the design and implementation of environmental monitoring programs to assess and control air quality, microbial contamination, and particulate matter in critical areas. It includes the use of viable and non-viable monitoring techniques, establishing alert and action limits, and conducting regular monitoring to maintain controlled environments.
What are the key principles of Good Engineering Practice that ensure the safe handling and storage of hazardous materials in pharmaceutical manufacturing?
Answer: GEP emphasizes proper design and engineering controls for the safe handling, storage, and containment of hazardous materials. This includes utilizing appropriate ventilation systems, implementing effective labeling and signage, providing appropriate personal protective equipment (PPE), and ensuring compliance with regulatory requirements for hazardous material management.
How does Good Engineering Practice impact the qualification and validation of analytical instruments and laboratory equipment in the pharmaceutical industry?
Answer: GEP sets guidelines for the qualification and validation of analytical instruments and laboratory equipment to ensure accurate and reliable results. This involves performance testing, calibration, maintenance, and adherence to regulatory requirements for equipment used in quality control, research, and development.
You may also read about Good Laboratory Practices (GLP)
Quite valuable & simple to understand the concepts of GEP.