Wet scrubbers in the industry operate on a simple yet effective principle. Airborne contaminants, such as dust, fine particles, and potentially harmful fumes generated during various pharmaceutical processes, are drawn into the wet scrubber. Inside the scrubber, a liquid, typically water, is introduced into the system. As the contaminated air encounters the scrubbing liquid, pollutants undergo various mechanisms of removal. These include absorption, condensation, impaction, and agglomeration. Pollutants dissolve into the liquid through chemical reactions, condense into droplets, or collide with liquid droplets, effectively removing them from the air stream.
In the pharmaceutical industry, where precision and purity are paramount, wet scrubbers play a crucial role in maintaining a clean and controlled environment. These pollution control devices are employed to capture and remove airborne contaminants, ensuring product quality, operator safety, and compliance with stringent regulatory standards.
Key functions of the Wet Scrubber:
- Air Quality Assurance: Wet scrubbers ensure that the air within pharmaceutical facilities remains clean and free from contaminants that could compromise product quality or pose health risks to workers.
- Safety and Compliance: Compliance with strict regulatory standards is a non-negotiable aspect of pharmaceutical manufacturing. Wet scrubbers help pharmaceutical companies meet these standards by capturing and eliminating pollutants that may contain hazardous or controlled substances.
- Operator Well-being: Maintaining a safe and healthy working environment is paramount. Wet scrubbers protect operators by preventing exposure to harmful airborne contaminants, contributing to a safer workplace.
- Environmental Responsibility: Pharmaceutical companies are increasingly committed to environmental sustainability. Wet scrubbers aid in minimizing emissions of pollutants into the atmosphere, aligning with environmental responsibility objectives
Working principle of wet scrubber
The wet scrubber used in tablet coating machines / Fluid bed Dryers in the pharmaceutical industry plays a crucial role in maintaining a clean and controlled environment during the tablet coating process. Its working principle involves the removal of airborne contaminants, such as dust and fumes, to ensure product quality and operator safety. Here’s a brief overview of the working principle of a wet scrubber in this context:
1. Inlet and Capture: The tablet coating machine generates airborne contaminants in the form of dust, fine particles, and fumes during the coating process. These contaminants are drawn into the wet scrubber through an inlet or capture hood located near the source of emissions.
2. Scrubbing Liquid Introduction: Inside the wet scrubber, a liquid, typically water, is introduced into the system. This liquid can also contain additives or chemicals, depending on the specific contaminants to be removed.
3. Contact and Absorption: As the contaminated air stream enters the wet scrubber, it comes into contact with the liquid. The pollutants in the air are absorbed into the liquid through various mechanisms, including:
- Absorption: Pollutants dissolve into the liquid due to chemical reactions between the contaminants and the scrubbing solution.
- Condensation: In some cases, contaminants may condense into droplets within the scrubber, effectively removing them from the air.
- Impaction and Agglomeration: Larger particles may collide with droplets of liquid, causing them to combine and form larger, easier-to-remove particles.
4. Particle Separation: Once the contaminants are absorbed into the liquid, the air stream continues through the wet scrubber. To prevent any liquid droplets from escaping with the treated air, the wet scrubber incorporates a mist eliminator or demister. This component captures and removes liquid droplets, allowing only clean, purified air to exit the scrubber.
5. Scrubbing Liquid Management: The liquid now laden with captured pollutants is collected at the bottom of the wet scrubber. It is then typically directed to a treatment system or a collection vessel where further processing or disposal takes place.
6. Continuous Operation: The wet scrubber operates continuously during tablet coating to ensure that airborne contaminants are effectively captured and removed throughout the process.
7. Monitoring and Control: Many modern wet scrubbers used in pharmaceutical tablet coating machines are equipped with monitoring and control systems. These systems help maintain optimal operating conditions by adjusting parameters such as liquid flow rate, pH, and temperature as needed to maximize efficiency and pollutant removal.
In summary, the wet scrubber in a tablet coating machine in the pharmaceutical industry works by introducing a scrubbing liquid into the path of the contaminated air. Through various mechanisms, including absorption and condensation, it captures and removes airborne contaminants. The clean air is then released into the environment, ensuring product quality and compliance with safety and environmental regulations.
Wet Scrubber diagram
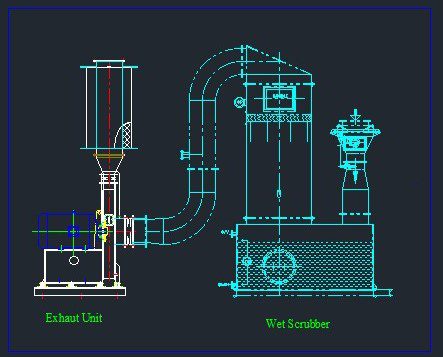
Types of wet scrubbers
Wet scrubbers are a versatile family of air pollution control devices designed to remove various airborne pollutants from industrial gas streams. There are several types of wet scrubbers, each tailored to specific applications and pollutants. Here are some common types of wet scrubbers:
- Venturi Scrubbers:
- Working Principle: Venturi scrubbers use the Venturi effect to create high-velocity gas streams that enhance the capture of particulate matter and pollutants.
- Applications: They are effective for removing fine particles, mists, and certain gases and are often used in power plants and industrial processes.
- Packed Bed Scrubbers:
- Working Principle: Packed bed scrubbers force gas streams through a bed of packing material (usually made of plastic or metal) where the contaminants are absorbed or captured.
- Applications: Commonly used for the removal of acidic gases, such as sulfur dioxide (SO2), and particulate matter, making them suitable for chemical processing and industrial emissions control.
- Spray Tower Scrubbers:
- Working Principle: In spray tower scrubbers, contaminated gas is directed upwards through a tower, and a scrubbing liquid is sprayed from the top. Pollutants are absorbed and removed as they come into contact with the liquid.
- Applications: Effective for removing acidic gases and particulate matter; used in applications like chemical manufacturing and wastewater treatment.
- Impingement Plate Scrubbers:
- Working Principle: Impingement plate scrubbers use a series of plates or trays to impede the flow of gas and promote the collision of contaminants with liquid droplets, facilitating their removal.
- Applications: Used for removing fine particulate matter and some gases in applications such as metal finishing and semiconductor manufacturing.
- Wet Electrostatic Precipitators (WESP):
- Working Principle: WESPs use an electrostatic charge to capture particles in the gas stream and collect them on charged plates or tubes. A liquid spray may be added to enhance removal efficiency.
- Applications: Effective for removing fine particulate matter and mists; often used in chemical, petrochemical, and pharmaceutical industries.
- Scrubbing Towers:
- Working Principle: Scrubbing towers are tall, vertical structures where contaminated gas is exposed to scrubbing liquid in a countercurrent or crosscurrent flow configuration.
- Applications: Suitable for a wide range of applications, including the removal of acidic gases, particulate matter, and volatile organic compounds (VOCs).
- Crossflow Scrubbers:
- Working Principle: Crossflow scrubbers use a horizontal gas flow that intersects with a vertical flow of scrubbing liquid, promoting contact and pollutant removal.
- Applications: Used for various pollutant removal tasks, including acidic gases, odors, and particulate matter.
- Bubble Plate Scrubbers:
- Working Principle: Bubble plate scrubbers introduce scrubbing liquid through a series of bubble plates or trays, creating turbulence that enhances contact between gas and liquid.
- Applications: Effective for removing fine particulate matter, mists, and some gases; often used in chemical and pharmaceutical industries.
Design parameters of the wet scrubber:
Designing a wet scrubber involves several key parameters that must be considered to ensure effective pollutant removal. While the specific design parameters can vary depending on factors like the type of pollutant, gas flow rate, and scrubbing liquid, I can provide a general overview of some essential design parameters and equations used in wet scrubber design:
1. Gas Flow Rate (Qg):
Gas flow rate is a critical parameter, usually measured in cubic meters per second (m³/s) or cubic feet per minute (CFM). To determine the required gas flow rate for a wet scrubber, you need to consider the volume of gas emissions from the source. The formula is:
Qg = (Pollutant Emission Rate) / (Pollutant Concentration in the Gas Stream)
2. Scrubbing Liquid Flow Rate (Ql):
The scrubbing liquid flow rate is the amount of liquid required to effectively capture pollutants. It’s measured in liters per second (L/s) or gallons per minute (GPM). The formula to calculate it depends on the specific design, but it often considers the gas flow rate and the liquid-to-gas ratio (L/G ratio), which is the ratio of liquid flow rate to gas flow rate.
Ql = Qg * L/G Ratio
3. Liquid-to-Gas Ratio (L/G Ratio):
The L/G ratio is a crucial parameter that determines the efficiency of pollutant removal. A higher L/G ratio typically results in better pollutant capture. The specific value depends on the contaminants and the scrubber type but is typically determined through empirical testing and engineering judgment.
4. Scrubbing Liquid pH:
The pH of the scrubbing liquid can affect the efficiency of pollutant removal, especially when dealing with acidic or basic gases. The pH is adjusted using chemical additives. It’s important to maintain the pH within the optimal range for the specific pollutant being targeted.
5. Scrubbing Liquid Temperature:
The temperature of the scrubbing liquid can influence chemical reactions and absorption efficiency. It’s crucial to maintain the liquid at a temperature that ensures effective pollutant capture.
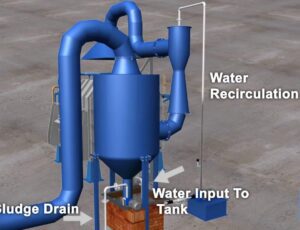
6. Contact Time (t):
The contact time represents the duration that the gas and liquid interact within the scrubber. It’s typically calculated by dividing the volume of the scrubber by the gas flow rate.
t = (Scrubber Volume) / (Gas Flow Rate)
7. Scrubber Efficiency (E):
The efficiency of a wet scrubber in capturing pollutants is a key parameter. It’s calculated as the ratio of the pollutant concentration at the inlet to the scrubber (Cin) and the pollutant concentration at the outlet (Cout).
E = (Cin - Cout) / Cin
8. Pressure Drop (ΔP):
Pressure drop is the change in pressure across the wet scrubber, often measured in Pascals (Pa) or inches of water (inH2O). It’s important to calculate and manage pressure drop to ensure proper operation of the scrubber and the overall process.
Advantages and Disadvantages of the wet scrubber
Advantages of Wet Scrubbers | Disadvantages of Wet Scrubbers |
---|---|
Highly effective in removing a wide range of pollutants, including acidic gases, particulate matter, and volatile organic compounds (VOCs). | High Water Usage: Wet scrubbers require a substantial amount of water, which may be a concern in water-scarce regions. |
Versatile and adaptable for various industrial applications and pollutant types. | Maintenance Complexity: The liquid-based nature of wet scrubbers can make maintenance more complex, including managing the scrubbing liquid and addressing potential corrosion issues. |
High removal efficiencies ensure compliance with stringent environmental regulations. | Higher Initial Costs: Wet scrubbers often have a higher upfront cost compared to some other pollution control technologies. |
No dust emissions, contributing to improved air quality. | Space Requirements: Wet scrubbers may require more space for installation and operation compared to dry scrubbers or other control methods. |
Can handle high-temperature gas streams effectively. | Waste Handling: Disposing of spent scrubbing liquid may require specialized treatment due to the concentrated pollutants it contains. |
Suitable for both new installations and retrofitting into existing industrial facilities. | Energy Consumption: Operating a wet scrubber may require energy for pump systems, which can add to operational costs. |
Effective at capturing and removing hazardous air pollutants (HAPs) and toxic gases. | Limited Applicability in Water-Sensitive Areas: In regions with strict water conservation measures, the high water consumption of wet scrubbers may pose challenges. |
Proven track record of performance in various industries and applications. | Potential for Corrosion: Wet scrubbers can be susceptible to corrosion due to the presence of liquid, necessitating corrosion-resistant materials and maintenance measures. |
Applications of the wet scrubber
Application | Description |
---|---|
Industrial Processes | – Removal of acidic gases, particulate matter, and odors in manufacturing, metal processing, and chemical industries. |
– Capture of dust and fumes in foundries, glass manufacturing, and cement production. | |
Power Generation | – Control of sulfur dioxide (SO2) emissions from coal and oil-fired power plants. |
– Removal of fine particulates, such as fly ash, in flue gas streams. | |
Waste Incineration | – Scrubbing of toxic gases, dioxins, and heavy metals produced during waste disposal. |
– Reduction of emissions from medical waste incinerators and municipal solid waste facilities. | |
Chemical Processing | – Elimination of corrosive gases, like hydrogen chloride (HCl), from chemical production processes. |
– Capture of volatile organic compounds (VOCs) emitted during solvent recovery and chemical synthesis. | |
Oil and Gas Industry | – Removal of hydrogen sulfide (H2S) and other sulfur compounds in natural gas processing. |
– Treatment of emissions from oil refineries and offshore drilling platforms. | |
Pulp and Paper Mills | – Control of sulfur compounds and other pollutants generated during paper production. |
Pharmaceutical Industry | – Scrubbing of hazardous chemical by-products and VOCs in pharmaceutical manufacturing. |
Food Processing | – Odor control and removal of organic emissions in food processing and rendering facilities. |
Dry Vs. Wet Scrubbers
Aspect | Dry Scrubbers | Wet Scrubbers |
---|---|---|
Operation Principle | Use dry sorbents or absorbent powders to capture pollutants in the gas stream. | Employ a liquid (usually water) to capture and remove pollutants by physical and chemical mechanisms. |
Pollutant Types | Effective for capturing particulate matter and some acidic gases (e.g., HCl) using dry sorbents. | Versatile; suitable for a wide range of pollutants, including acidic gases, particulate matter, and volatile organic compounds (VOCs). |
Efficiency | Moderate removal efficiency, particularly for particulates and certain gases. | High removal efficiency for a broad spectrum of contaminants, ensuring compliance with strict environmental regulations. |
Water Usage | Minimal water usage, as dry scrubbers do not require liquid. | Significant water consumption, which may be a concern in areas with water scarcity. |
Maintenance Complexity | Generally less complex maintenance, as there is no liquid to manage. | May require more complex maintenance due to the liquid-based operation, including managing scrubbing liquid and addressing potential corrosion issues. |
Waste Generation | Limited waste generation, as spent sorbents can often be disposed of relatively easily. | Handling and disposing of spent scrubbing liquid may be more challenging due to the concentrated pollutants. |
Dust Emissions | Can generate dust emissions during the injection of dry sorbents, which may pose environmental and health hazards. | Do not generate dust emissions, contributing to improved air quality. |
Space Requirements | Compact and often suitable for retrofitting into existing facilities. | May require more space for installation and operation, making them less suitable for retrofitting. |
Cost | Generally lower initial cost compared to wet scrubbers. | Often higher upfront cost due to the more complex design and liquid handling requirements. |
Corrosion Risk | Lower risk of corrosion due to the absence of liquid. | Susceptible to corrosion in some cases, necessitating corrosion-resistant materials and maintenance measures. |
Heat Resistance | Suitable for high-temperature gas streams. | Can handle high-temperature gas streams effectively. |
Frequently Asked Questions:
Where are wet scrubbers used?
Answer: Wet scrubbers are used in a wide range of industries and applications where the removal of airborne pollutants is essential for environmental compliance, air quality, and safety. Common areas of application include:
- Manufacturing: Wet scrubbers are used in various manufacturing processes to capture and remove particulate matter, acids, and other pollutants. Industries such as metal fabrication, glass manufacturing, and ceramics often employ wet scrubbers.
- Power Generation: In power plants, wet scrubbers are used to control emissions of sulfur dioxide (SO2) and particulate matter from flue gas generated by the combustion of fossil fuels, particularly coal and oil.
- Chemical Processing: Chemical manufacturing facilities utilize wet scrubbers to manage emissions of hazardous or corrosive gases, ensuring worker safety and environmental compliance.
- Waste Incineration: Wet scrubbers play a critical role in waste incineration facilities by capturing and neutralizing harmful gases, dioxins, and heavy metals produced during the incineration process.
- Pharmaceuticals: In pharmaceutical manufacturing, wet scrubbers help control emissions of volatile organic compounds (VOCs) and other pollutants from various processes.
- Food Processing: Wet scrubbers are used to remove odors and contaminants generated in food processing and rendering facilities, contributing to a healthier working environment.
What is the difference between a wet scrubber and a scrubber?
Answer: The term “scrubber” is often used interchangeably with “wet scrubber,” but it’s essential to clarify the distinction:
- Scrubber: The term “scrubber” is a broad term that encompasses various pollution control devices used to remove pollutants from gas streams. Scrubbers can be categorized into two main types: wet scrubbers and dry scrubbers.
- Wet Scrubber: A wet scrubber is a specific type of scrubber that uses a liquid (usually water) to capture and remove airborne pollutants. It operates on the principle of absorption, condensation, and chemical reactions between the pollutants and the scrubbing liquid.
- Dry Scrubber: A dry scrubber, on the other hand, employs dry sorbents or absorbent powders to capture pollutants without using a liquid. It relies on chemical reactions between the dry sorbents and the contaminants to achieve pollutant removal.
Why is it called a wet scrubber?
Answer: A wet scrubber is called so because it utilizes a liquid (i.e., it is “wet”) to scrub or cleanse polluted gas streams. The term “scrub” in this context refers to the physical and chemical processes by which pollutants are captured and removed from the air. The scrubbing liquid comes into contact with the contaminated gas, resulting in the removal or “scrubbing” of the pollutants.
What material is used in wet scrubbers?
Answer: Wet scrubbers are typically constructed using materials that are resistant to corrosion and compatible with the chemicals used in the scrubbing process. Common materials include:
- Stainless Steel: Stainless steel is highly resistant to corrosion and is often used in wet scrubber construction, especially when dealing with acidic gases.
- Fiberglass Reinforced Plastic (FRP): FRP is lightweight and corrosion-resistant, making it suitable for wet scrubbers in various applications.
- Corrosion-Resistant Alloys: Specialized alloys, such as Hastelloy or Inconel, are used when dealing with particularly corrosive environments.
- Coatings: Some wet scrubbers may have protective coatings to enhance resistance to corrosion and chemical attack.
The choice of material depends on factors such as the specific pollutants to be removed, the operating environment, and cost considerations, and it is essential to select materials that can withstand the conditions encountered in the application.
What is the purpose of a wet scrubber in an industrial setting?
Answer: The primary purpose of a wet scrubber in an industrial setting is to remove airborne contaminants from exhaust gas streams, thereby improving air quality, complying with environmental regulations, and ensuring the safety of workers and the surrounding environment.
How does a wet scrubber capture and remove pollutants from gas streams?
Answer: Wet scrubbers capture and remove pollutants through mechanisms such as absorption, condensation, impaction, and chemical reactions. As contaminated gas encounters a scrubbing liquid, pollutants transfer to the liquid phase, making the gas cleaner before discharge.
What factors influence the selection of a specific wet scrubber type for an industrial application?
Answer: The choice of wet scrubber type depends on factors like the type of pollutants to be removed, gas flow rates, space constraints, temperature, and the presence of corrosive substances. Different scrubber types excel in specific applications due to their design and operating principles.
How does the liquid-to-gas ratio (L/G ratio) affect the performance of a wet scrubber?
Answer: The L/G ratio is a critical parameter in wet-scrubber design. Increasing the L/G ratio generally improves pollutant removal efficiency as it increases the contact between the gas and liquid phases. However, excessively high ratios can lead to increased water consumption and operational costs.
What are the key maintenance considerations for wet scrubbers?
Answer: Proper maintenance of wet-scrubbers includes monitoring and adjusting parameters such as liquid flow rate, pH levels, and pressure. Regular inspections, cleaning, and servicing of components like mist eliminators, pumps, and nozzles are essential to ensure optimal performance and prevent corrosion.
How can wet scrubbers handle high-temperature gas streams effectively?
Answer: Wet scrubbers can handle high-temperature gas streams by incorporating materials and designs that are heat-resistant. Additionally, cooling the gas stream before it enters the scrubber can help reduce its temperature to a level suitable for the wet scrubbing process.
What are the environmental benefits of using wet scrubbers?
Answer: Wet-scrubbers contribute to environmental protection by reducing emissions of pollutants into the atmosphere. They help lower the concentration of harmful gases and particulate matter, improving air quality and minimizing the environmental impact of industrial operations.
How do wet scrubbers address the issue of odor control in industrial processes?
Answer: Wet-scrubbers can effectively remove odorous compounds from gas streams by absorbing them in the scrubbing liquid or chemically converting them into less odorous compounds. This makes wet-scrubbers valuable tools for mitigating odor issues in various industrial applications, including wastewater treatment and food processing.
What is the role of mist eliminators in wet scrubbers, and how do they work?
Answer: Mist eliminators are components in wet-scrubbers designed to capture and remove liquid droplets from the treated gas stream. They typically consist of a series of baffles, vanes, or mesh pads that allow the captured liquid to drain back into the scrubber while allowing clean gas to exit.
Can wet scrubbers be used for both particulate matter and gas removal in the same application?
Answer: Yes, wet-scrubbers are versatile and can be configured to remove both particulate matter and gases simultaneously. By adjusting parameters like liquid flow rate, pH, and the type of scrubbing liquid, wet-scrubbers can efficiently capture a wide range of pollutants in a single application.