The purpose of this Standard Operating Procedure for Preventive Maintenance of Brine Chiller is to establish guidelines for the systematic and effective preventive maintenance of brine chillers. Proper maintenance ensures the optimal performance, longevity, and energy efficiency of the chiller, while minimizing unplanned downtime.
SOP for Preventive Maintenance of Brine Chiller
- OBJECTIVE:
- To lay down the Procedure for preventive maintenance of Brine chiller.
- SCOPE:
- This SOP is applicable to preventive maintenance of Brine chiller installed in technical area .
- RESPONSIBILITY:
- Technician/ Operator shall be responsible for proper execution of preventive maintenance as per SOP.
- Engineering – Head shall be responsible for reviewing the SOP and for ensuring proper execution of preventive maintenance.
- ACCOUNTABILITY:
- Engineering – Head shall be accountable for proper implementation of the SOP.
- DEFINITIONS:
- Nil
- PROCEDURE:
- Preventive maintenance shall be executed as per the SOP No.: SOP/EN/XXXYYY – Execution of Preventive Maintenance.
- Ensure that the spare parts are available at the time of preventive maintenance.
Preventive Maintenance of Brine Chiller – Mechanical
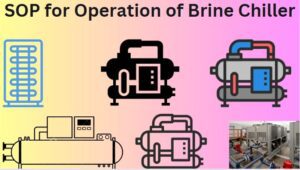
- Clean all water strainers in chilled water and condensing water piping system
- Shut down the pumps
- Close the isolation valve of pump.
- Drain out the strainer by drain plug provided at the bottom.
- Open the flanges of strainer, remove the mesh, clean and replace if required.
- Put the mesh inside the strainer, tight the nut and bolts of flanges.
- Open the valve
- Cleaning of water strainer shall be done after every month.
- Checking of the valves
- Check the valves for smooth closing and opening, it should not be hard, if it is so, the valve preventive maintenance should be carried out as follows.
- Switch off the pump.
- Close the nearby upward and downward side valves.
- Open the valve flanges lightly to drain out the water.
- After draining the water open the full flanges.
- Check the valve internals for any damage, for valve seal, gaskets, stem locking nut tightness; if required clean or replace the internals.
- Refit the valve, open the both side nearby valves, check for any leakages, check for normal closing and opening operation. If found okay, put the system on or otherwise replace the valve.
- The valve checking frequency shall be after every month.
- Checking the refrigerant leakage
- Check the refrigerant pressure in the refrigerant circuit after every three months.
- If the temperature of the filter is lower than the upstream temperature the filter should be replaced.
- Checking shall be done on quarterly basis.
- Removing and charging of compressor oil
- The oil is compressor oil sump is under a constant positive pressure at ambient temperature.
- To remove oil, open the service valves located on the bottom of the oil sump and drain the oil into a suitable container using the procedure as below
- Connect a line to the oil sump drain valve.
- Open the valve and allow the desired amount of oil into the container and close the charging valve.
- Measure the exact amount of oil removed from the unit.
- It is critical to fill the oil lines feeding the compressor when charging a system with oil. It is recommended that to call the service engineer for replacing / charging the oil.
- Checking of oil filter in Preventive Maintenance of Brine Chiller
- Run the chiller on fully unloaded condition for approximately 20 minutes.
- Check the oil filter differential pressure by calculating the difference between the condenser suction pressure and oil pressure.
- Checking shall be done on monthly basis.
- Checking of Chilled water pump in Preventive Maintenance of Brine Chiller
- Check for any leakages from the mechanical seal, if found rectify the same.
- Check the lubrication of mechanical seal and coupling if required lubricate the same with recommended lubricating grease.
- Check the condition of coupling between pump and motor, if found damage replaces the same.
- Check the pump for any abnormal sound if found, check the bearing impeller and other moving parts, if found damage rectifies the same.
- Clean the strainers.
- Checking shall be done on quarterly basis.
- Checking of instruments in Preventive Maintenance of Brine Chiller
- Check the instruments for proper installations.
- Check the instruments for tight end connections and tight contacts; if required tight the same.
- The online installed instrument are as follows
- Pressure gauge on condenser inlet line
- Temperature gauge on condenser inlet line.
- Pressure gauge on secondary pump discharge.
- Temperature gauge on evaporator outlet
- RTD sensor on the discharge of secondary pump.
- Checking shall be done on quarterly basis.
- Checking of Condenser pump in Preventive Maintenance of Brine Chiller
- Check for any leakages from the mechanical seal, if found rectify the same.
- Check the condition of coupling between pump and motor, if found damage replaces the same.
- Check the lubrication of mechanical seal and coupling if required lubricate the same with recommended lubricating grease.
- Check the pump for any abnormal sound if found, check the bearing impeller and other moving parts, if found damage rectifies the same.
- Clean the strainers.
- Checking shall be done on quarterly basis.
- Checking of chilled water pipeline and fittings in Preventive Maintenance of Brine Chiller
- Check all the pipe line supports and flange joints and tighten them if found loose.
- Check the flange joints nut and bolts on pipeline and fittings for leakages. If any leakage is present then check the gaskets, if found damaged replace the same and tighten the clamp.
- Check the insulation and cladding, if required repair the insulation and cladding.
- Checking shall be done six monthly.
- Preventive Maintenance of Brine Chiller – Electrical
- Checking of Crank case Heaters
- Switch ON the power supply of the chiller, machine should be in OFF position.
- Physically touch the oil sump from outside, it should be hot.
- Checking shall be done on quarterly basis.
- Checking of Terminals, Wiring and Components
- Ensure that the power supply to the machine is switched off.
- Clean the panel internally and externally by using vacuum cleaner.
- Visually check all the power and control wiring and terminals in the electric panel and at all the field instruments for any sign of overheating and loose terminals.
- Check and ensure by using appropriate tools that all the wires are properly tightened.
- Check and ensure that double earthing is provided to the panel.
- Ensure that there is no chance for the entry of dust into the panel.
- Ensure that all switches are working.
- Checking shall be done on quarterly basis.
- Checking of Contactors
- Ensure that the power supply to the machine is switched off.
- Open contactor contact points cover.
- Remove dust from control panel with air blower.
- Check all the contacts for pitting and carbon deposits in the contacts.
- Clean all the contacts with carbon tetra chloride or with contactor cleaner.
- Replace the contacts if found damaged or welded.
- Check the earthing of the panel body.
- A good earthing shall show less than 2 Volts between the Neutral Wire of the Incoming Power supply and Panel Body.
- Checking of contactors shall be done on quarterly basis.
- Checking of Pump Motor
- Check the insulation resistance of motor winding with the help of Megger.
- Check the phase continuity and winding continuity of motor with the help of Multimeter.
- Physically check the motor terminal box and terminal connections.
- Check the voltage and ampere ratings of motor with the help of tong tester.
- Check the direction of rotation; it should be as per recommended direction.
- Checking shall be done after every six month.
- Checking of Display
- Check the display
- Check the wiring contacts, if required tight the same.
- Checking of Display shall be done after every six month.
- Scheduling other maintenance and checks:
- Use a non destructive tube test to inspect the condenser and evaporator tubes at 3 year intervals.
- Post Preventive Maintenance – Check List
- Whenever any modifications and major works are carried out to the equipment, the same shall be mentioned in the equipment history card as per the respective SOP.
- Connect the equipment main power supply and start the equipment.
- Ensure that the equipment is running smoothly, without any abnormality.
- Record the Preventive maintenance details shall be record as per Format No. SOP/EN/XXXYYY.
- ABBREVIATIONS:
- CRF No. : Change Request Form number
- SOP : Standard Operating Procedure
- REFERENCES:
- Operational & Maintenance Manual of Chiller.
- DISTRIBUTION LIST:
- SOP shall be distributed to following departments Quality Assurance, Engineering as per user request.
- ANNEXURES:
- Preventive Maintenance Checklist & Record for Chiller : SOP/EN/XXXYYY
PREVENTIVE MAINTENANCE CHECKLIST & RECORD FOR BRINE CHILLER
Equipment Name | Location | ||
Equipment ID | Frequency |
Things to be done: | Check List | Remarks |
Monthly Check List | ||
Clean all water strainers in chilled water and condensing water piping. | ||
Checking of valves. | ||
Checking of oil sump level. | ||
Checking of oil filter. | ||
Quarterly Check List | ||
Checking of the refrigerant leakages. | ||
Checking of chilled water primary and secondary pump for abnormal sound, leakages, mechanical seal and lubrication. | ||
Checking of installed instruments for proper end connections and wiring contacts. | ||
Checking of condenser pumps for any abnormal sound; leakages; mechanical seal and lubrication. | ||
Checking of crank case heaters. | ||
Checking of terminals; wiring and components. | ||
Checking of contactors. | ||
Half Yearly Check List | ||
Checking of condenser and evaporator for scale and fouling. | ||
Checking of chilled water pipe line and fittings for any leakages, insulation; cladding. | ||
Checking of pump motor. | ||
Checking of display | ||
Checking of safety interlocks. | ||
Yearly Check List | ||
Checking of condenser and evaporator for scale and fouling and de-scaling of the same. |